Regular furnace cleaning and maintenance are essential for ensuring the system's efficiency, longevity, and safety. The recommended frequency for cleaning and inspecting a furnace depends on various factors, including usage, the type of furnace, and environmental conditions. Generally, professional furnace maintenance should be scheduled annually, with duct cleaning every 3-5 years. Additionally, air filters should be replaced every 1-3 months, and burners should be inspected and cleaned regularly to prevent debris buildup and ensure proper function. Bi-annual inspections are also advised for a more thorough check of critical components.
Key Points Explained:
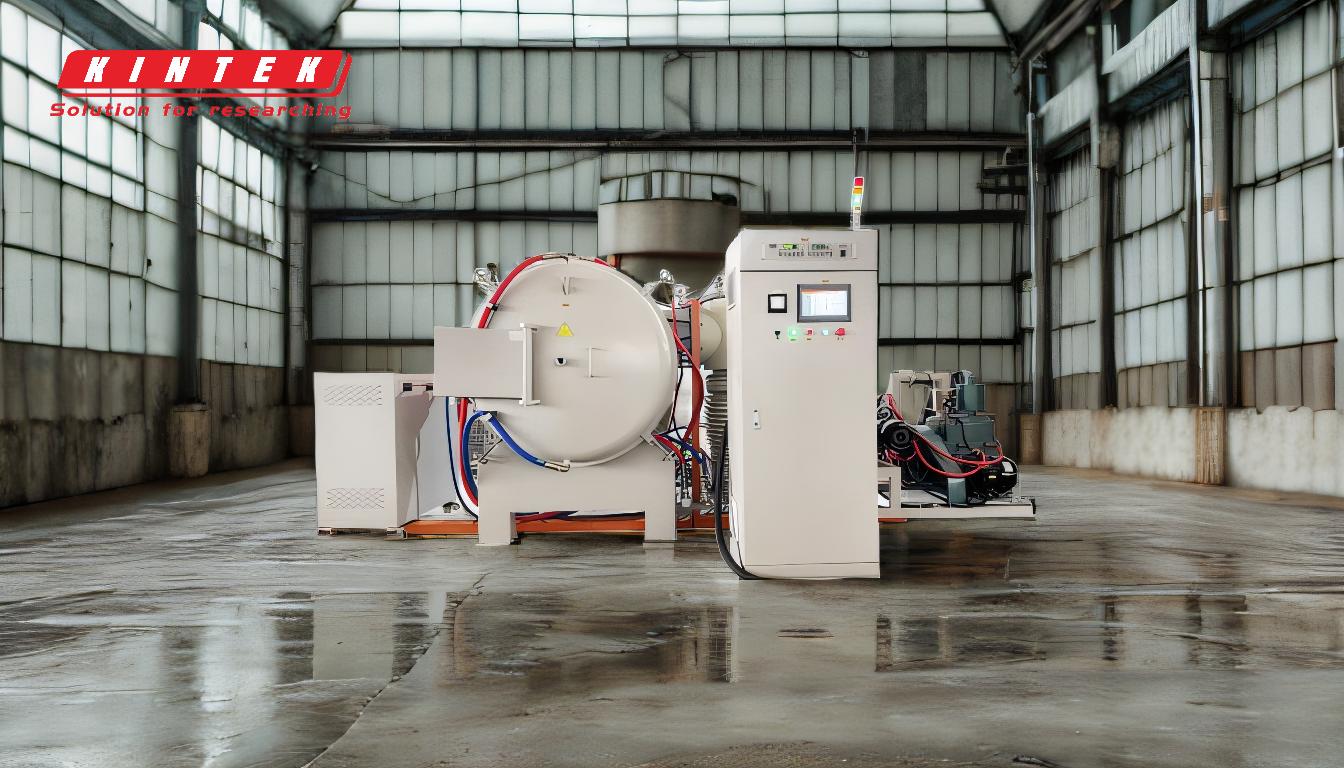
-
Annual Professional Maintenance:
- Why it's important: Annual maintenance ensures the furnace operates efficiently and safely. Professionals can identify and address potential issues before they become major problems.
- What it includes: A comprehensive inspection of the furnace, cleaning of internal components, and checking for wear and tear.
- Reference: "We usually advise that you schedule furnace maintenance every 1-2 years (ideally once a year)."
-
Duct Cleaning Every 3-5 Years:
- Why it's important: Clean ducts improve indoor air quality and ensure the furnace operates smoothly by reducing airflow restrictions.
- What it includes: Removing dust, debris, and other contaminants from the ductwork.
- Reference: "Duct cleaning at intervals of 3 to 5 years for a smooth-running system and excellent indoor air quality."
-
Air Filter Replacement:
- Why it's important: Clean air filters ensure proper airflow, improve air quality, and prevent the furnace from overworking.
- Frequency: Replace every 1-3 months, depending on filter type and usage.
- Reference: "The air filter in a furnace should be replaced at least every 3 months. Ideally, it should be changed every 1-2 months."
-
Regular Burner Inspection and Cleaning:
- Why it's important: Clean burners ensure efficient combustion and prevent issues like incomplete ignition or uneven heating.
- How to do it: Turn off power and gas, remove the cover panel, vacuum debris, and clean burners with a brass wire brush.
- Reference: "Furnace burners should be inspected regularly for cleanliness and proper function."
-
Bi-Annual Inspections:
- Why it's important: More frequent inspections help identify and address issues early, especially in critical areas like chamber penetrations.
- What it includes: A thorough check of the furnace when it's cold, focusing on areas prone to wear or damage.
- Reference: "A thorough bi-annual inspection of the furnace should be performed when the furnace is cold."
-
Timely Removal of Oxide and Debris:
- Why it's important: Removing oxide and debris ensures the furnace functions properly and extends its lifespan.
- How to do it: Regularly clean internal components and check for buildup.
- Reference: "Keep the furnace clean and remove any oxide in the furnace in a timely manner to ensure its proper functioning and longevity."
By following these guidelines, you can maintain your furnace's efficiency, improve indoor air quality, and avoid costly repairs or replacements. Regular cleaning and inspections are small investments that yield significant long-term benefits.
Summary Table:
Maintenance Task | Frequency | Key Benefits |
---|---|---|
Annual Professional Maintenance | Once a year | Ensures efficient and safe operation, identifies potential issues early. |
Duct Cleaning | Every 3-5 years | Improves indoor air quality and reduces airflow restrictions. |
Air Filter Replacement | Every 1-3 months | Ensures proper airflow, improves air quality, and prevents furnace overworking. |
Burner Inspection & Cleaning | Regularly | Prevents debris buildup, ensures efficient combustion, and avoids uneven heating. |
Bi-Annual Inspections | Twice a year | Identifies and addresses issues early, especially in critical areas. |
Removal of Oxide & Debris | Regularly | Extends furnace lifespan and ensures proper functioning. |
Ensure your furnace runs efficiently and safely—contact our experts today for professional maintenance!