The temperature of a furnace is measured using a combination of direct and indirect methods, depending on the specific requirements and conditions of the furnace. Direct methods involve placing temperature sensors, such as thermocouples, in contact with the furnace or its components to obtain precise readings. Indirect methods, such as infrared thermometers, measure temperature without physical contact by detecting thermal radiation. Additionally, advanced techniques like optical pyrometers and system accuracy tests ensure reliable and accurate temperature monitoring. These methods are often complemented by external monitoring devices and cross-referencing techniques to maintain consistent and accurate furnace performance.
Key Points Explained:
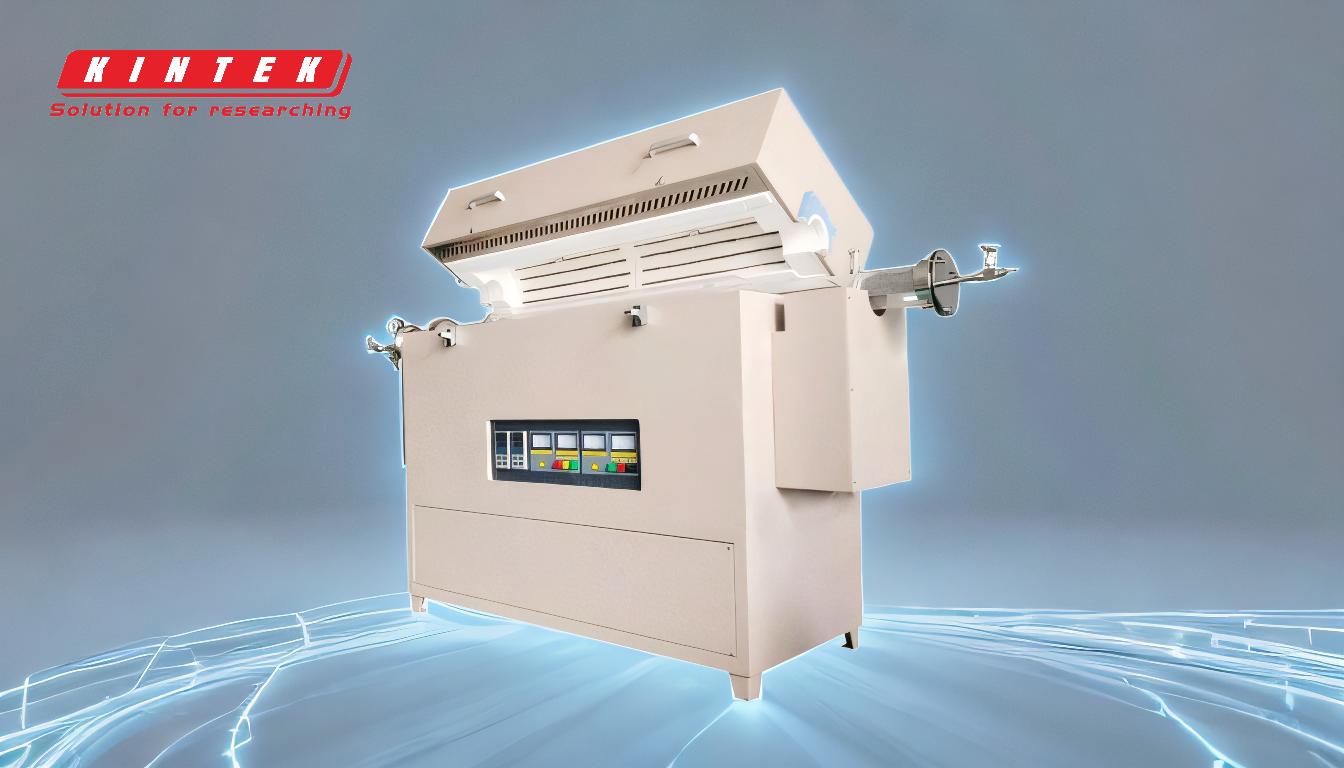
-
Direct Temperature Measurement:
- Thermocouples: These are the most common sensors used for direct temperature measurement in furnaces. They are placed in direct contact with the furnace tubes or other components to provide real-time temperature readings. Thermocouples are highly accurate and can withstand high temperatures, making them ideal for industrial applications.
- Load Thermocouples: These are used to simulate the temperature of the parts being processed in the furnace. By placing a thermocouple on or near the load, operators can ensure that the parts are being heated to the desired temperature.
- System Accuracy Tests: Regular tests are conducted to ensure that the temperature readings from thermocouples are accurate. These tests help identify any discrepancies and ensure the furnace is performing as expected.
-
Indirect Temperature Measurement:
- Infrared Thermometers: These devices measure temperature by detecting the thermal radiation emitted by the furnace tubes. They are used when direct contact is not feasible, such as when measuring the temperature of moving parts or through a peek window. Infrared thermometers provide a non-contact method of temperature measurement, which can be useful in hazardous or hard-to-reach areas.
- Optical Pyrometers: These are specialized devices that measure temperature by analyzing the intensity of light emitted by the furnace. They are particularly useful in minimizing the exposure of thermocouples to harsh environments, thereby extending their lifespan.
-
Monitoring and Control:
- Control Panels: Modern furnaces are equipped with digital control panels that display real-time temperature readings. These panels allow operators to monitor and adjust the furnace temperature as needed.
- External Monitoring Devices: For added precision, external temperature monitoring devices, such as additional thermocouples, can be used to cross-reference the furnace’s built-in temperature sensors. This helps ensure that the temperature readings are consistent and accurate.
- Temperature Uniformity Surveys: These surveys are conducted to identify the hottest and coldest spots within the furnace. By placing thermocouples at these specific locations, operators can ensure that the temperature is uniform throughout the furnace, which is critical for consistent results.
-
Advanced Techniques:
- Dew Point Measurement: This method is used to monitor the moisture content in the furnace atmosphere. By controlling the dew point, operators can ensure that the furnace atmosphere is optimal for the process being carried out.
- Shim Stock Analysis: This technique involves placing thin metal strips (shim stock) in the furnace and analyzing them after exposure to determine the temperature and atmosphere conditions.
- Non-Dispersive Infrared (NDIR) Analyzers: These devices measure the concentration of specific gases in the furnace atmosphere, which can affect the temperature and overall process.
- Carbon Sensors: These sensors are used to monitor the carbon content in the furnace atmosphere, which is critical for processes like carburizing.
-
Corrosion-Resistant Sensors:
- Heated Manometers: These devices provide absolute pressure sensing, independent of the gas composition in the furnace. They are designed to withstand corrosive environments, ensuring long-term reliability and accuracy.
By combining these methods, operators can achieve precise and reliable temperature control in industrial furnaces, ensuring optimal performance and consistent results.
Summary Table:
Method | Description |
---|---|
Direct Measurement | Uses sensors like thermocouples in direct contact with furnace components. |
Indirect Measurement | Infrared thermometers and optical pyrometers measure without physical contact. |
Monitoring & Control | Digital control panels and external devices ensure consistent temperature. |
Advanced Techniques | Includes dew point measurement, shim stock analysis, and carbon sensors. |
Corrosion-Resistant | Heated manometers withstand harsh environments for reliable pressure sensing. |
Need precise furnace temperature measurement solutions? Contact our experts today!