Activated carbon regeneration is a process that restores the adsorption capacity of spent activated carbon, making it reusable. The most common method is thermal regeneration, which involves heating the carbon to high temperatures to destroy or volatilize the adsorbed contaminants. This process typically occurs in three stages: drying, pyrolysis, and activation. Each stage plays a critical role in ensuring the carbon is effectively regenerated and ready for reuse. Below, we explore the key points of this process in detail.
Key Points Explained:
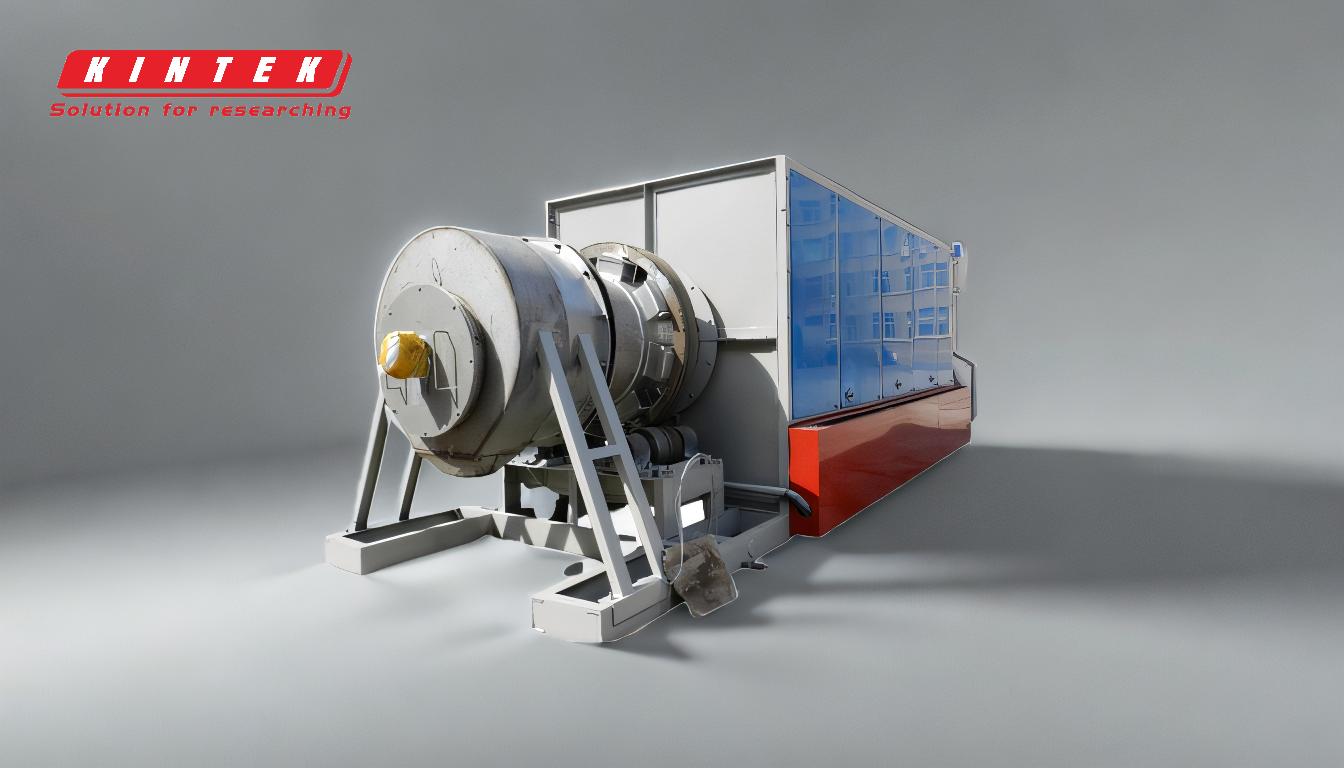
-
Thermal Regeneration Overview:
- Thermal regeneration is the most widely used method for regenerating activated carbon due to its effectiveness in removing a wide range of adsorbed contaminants.
- The process involves heating the spent carbon in a controlled environment, usually in a rotary kiln or a multiple-hearth furnace, to high temperatures (typically between 600°C and 900°C).
- This method is suitable for carbon contaminated with organic compounds, as the high temperatures decompose or volatilize these contaminants.
-
Three Stages of Thermal Regeneration:
-
Drying Stage:
- The first stage involves removing moisture from the spent carbon. This is done by heating the carbon to temperatures around 100°C to 200°C.
- Drying is essential to prepare the carbon for the subsequent pyrolysis stage, as moisture can interfere with the thermal decomposition of adsorbed contaminants.
-
Pyrolysis Stage:
- In this stage, the temperature is increased to between 400°C and 600°C. At these temperatures, the adsorbed organic compounds undergo thermal decomposition (pyrolysis).
- The organic contaminants break down into smaller molecules, which are either volatilized or converted into carbonaceous residues.
-
Activation Stage:
- The final stage involves raising the temperature to between 700°C and 900°C in the presence of a controlled amount of steam or carbon dioxide.
- This step reactivates the carbon by burning off the carbonaceous residues formed during pyrolysis, restoring its porous structure and adsorption capacity.
-
Drying Stage:
-
Factors Influencing Regeneration Efficiency:
-
Temperature Control:
- Precise temperature control is critical to ensure effective regeneration without damaging the carbon structure.
- Overheating can lead to excessive burn-off, reducing the carbon's mass and adsorption capacity.
-
Contaminant Type:
- The nature of the adsorbed contaminants affects the regeneration process. For example, some contaminants may require higher temperatures or longer exposure times to decompose fully.
-
Carbon Quality:
- The source material and initial quality of the activated carbon influence its ability to withstand the regeneration process without significant degradation.
-
Temperature Control:
-
Advantages of Thermal Regeneration:
-
Cost-Effectiveness:
- Regenerating activated carbon is often more economical than replacing it, especially for large-scale applications.
-
Environmental Benefits:
- Reusing activated carbon reduces waste and minimizes the need for new carbon production, which is energy-intensive.
-
Versatility:
- Thermal regeneration can be applied to carbon used in various industries, including water treatment, air purification, and chemical processing.
-
Cost-Effectiveness:
-
Limitations and Challenges:
-
Energy Consumption:
- The high temperatures required for thermal regeneration make it energy-intensive, which can increase operational costs.
-
Carbon Loss:
- Each regeneration cycle results in some loss of carbon mass due to burn-off, reducing the total lifespan of the carbon.
-
Contaminant Residues:
- Some contaminants may leave behind residues that cannot be fully removed, leading to a gradual decline in carbon performance over multiple regeneration cycles.
-
Energy Consumption:
-
Alternative Regeneration Methods:
-
Chemical Regeneration:
- This method involves using solvents or chemical reagents to desorb contaminants from the carbon. It is often used for specific contaminants that are difficult to remove thermally.
-
Biological Regeneration:
- Microorganisms are used to degrade adsorbed organic contaminants. This method is less common and typically used in niche applications.
-
Steam Regeneration:
- Steam is used to desorb volatile organic compounds (VOCs) from the carbon. This method is less energy-intensive than thermal regeneration but is limited to specific types of contaminants.
-
Chemical Regeneration:
-
Applications of Regenerated Activated Carbon:
-
Water Treatment:
- Regenerated carbon is commonly reused in water treatment plants to remove organic pollutants, chlorine, and other contaminants.
-
Air Purification:
- It is used in air filters to capture VOCs, odors, and other airborne pollutants.
-
Industrial Processes:
- Regenerated carbon finds applications in industries such as food and beverage, pharmaceuticals, and chemical manufacturing for purification and separation processes.
-
Water Treatment:
By understanding the thermal regeneration process and its stages, users can make informed decisions about maintaining and reusing activated carbon, ensuring cost savings and environmental sustainability.
Summary Table:
Key Aspect | Details |
---|---|
Thermal Regeneration | Heating spent carbon to 600°C–900°C to remove contaminants. |
Three Stages | 1. Drying (100°C–200°C) 2. Pyrolysis (400°C–600°C) 3. Activation (700°C–900°C) |
Advantages | Cost-effective, eco-friendly, and versatile for various industries. |
Limitations | High energy use, carbon loss, and potential residue buildup. |
Alternative Methods | Chemical, biological, and steam regeneration for specific contaminants. |
Applications | Water treatment, air purification, and industrial processes. |
Discover how activated carbon regeneration can save costs and reduce waste—contact our experts today!