Solid-state sintering and liquid-phase sintering are two distinct processes used in the densification of ceramics and other materials, differing primarily in the mechanisms of particle bonding and the temperatures required. Solid-state sintering relies on diffusion mechanisms to transport material and achieve densification, typically at higher temperatures, and is suitable for materials like zirconia and alumina. In contrast, liquid-phase sintering involves the introduction of a low-melting-point liquid phase, which facilitates particle rearrangement and bonding at lower temperatures, making it ideal for harder-to-densify materials like silicon nitride and silicon carbide. The presence of the liquid phase accelerates densification and influences pore closure, grain size, and mechanical properties.
Key Points Explained:
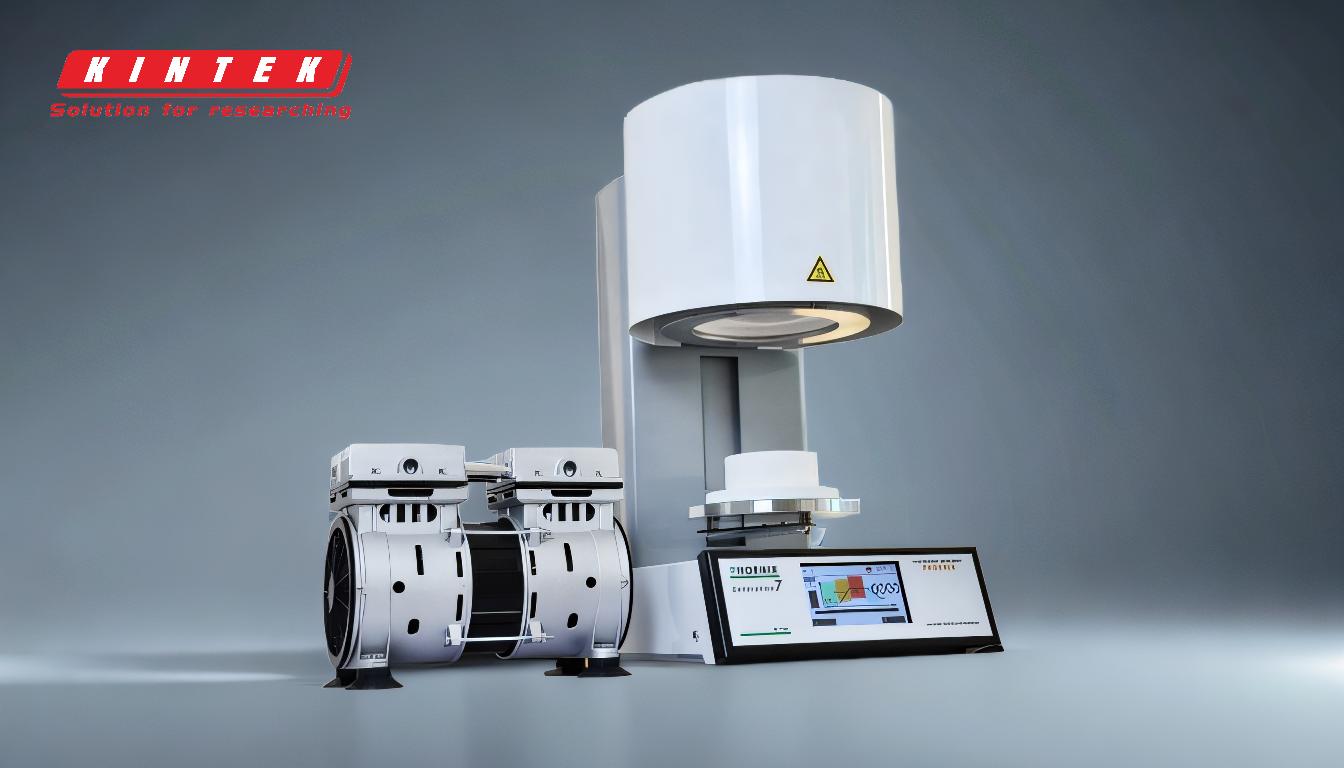
-
Sintering Temperature:
- Solid-State Sintering: This process occurs at relatively high temperatures, often close to the melting point of the primary material. For example, zirconia and alumina are sintered at temperatures around 1600°C. The high temperatures are necessary to activate diffusion mechanisms, which are the primary means of material transport and bonding.
- Liquid-Phase Sintering: This method operates at lower temperatures compared to solid-state sintering. The addition of a low-melting-point liquid phase reduces the overall sintering temperature required for densification. The liquid phase forms at the sintering temperature, enabling capillary forces to rearrange particles more efficiently.
-
Mechanisms of Densification:
- Solid-State Sintering: Densification is achieved through solid-state diffusion. Atoms move from areas of high chemical potential (e.g., particle surfaces) to areas of low chemical potential (e.g., necks between particles). This process is slower and requires higher temperatures to overcome the activation energy barriers for diffusion.
- Liquid-Phase Sintering: The liquid phase enhances densification by providing a high diffusivity path for atoms. Capillary forces drive particle rearrangement, and the liquid phase fills gaps between particles, promoting faster bonding and densification. This process is particularly effective for materials that are difficult to densify through solid-state mechanisms.
-
Pore Closure:
- Solid-State Sintering: Pore closure in solid-state sintering is a gradual process that relies on the slow diffusion of atoms. As sintering progresses, pores shrink and eventually close, but this can take a significant amount of time, especially at lower temperatures. The final microstructure may still contain some residual porosity, depending on the sintering conditions.
- Liquid-Phase Sintering: The presence of the liquid phase accelerates pore closure. The liquid fills pores and gaps between particles, leading to faster densification. The liquid phase also helps to redistribute material, reducing the overall porosity more effectively than in solid-state sintering. This results in a denser final product with fewer residual pores.
-
Grain Size and Microstructure:
- Solid-State Sintering: This process can lead to significant grain growth, especially at high temperatures. Larger grains can negatively impact mechanical properties, such as strength and toughness. The microstructure is typically characterized by larger, more uniform grains.
- Liquid-Phase Sintering: Liquid-phase sintering tends to produce smaller grain sizes due to the lower sintering temperatures and the presence of the liquid phase, which can inhibit grain growth. The resulting microstructure is finer, which can improve mechanical properties such as flexural strength and fracture toughness. Additionally, the fracture mode may shift from transgranular (through the grains) to intergranular (along grain boundaries), further enhancing toughness.
-
Material Suitability:
- Solid-State Sintering: This method is suitable for materials that can be densified through diffusion mechanisms, such as zirconia and alumina. These materials typically have high melting points and do not require the addition of a liquid phase for densification.
- Liquid-Phase Sintering: This method is ideal for materials that are difficult to densify through solid-state mechanisms, such as silicon nitride and silicon carbide. The addition of a liquid phase facilitates densification at lower temperatures and improves the overall sintering kinetics.
-
Mechanical Properties:
- Solid-State Sintering: The mechanical properties of materials sintered via solid-state methods are generally good, with high density and excellent high-temperature performance. However, the potential for grain growth at high temperatures can lead to reduced strength and toughness.
- Liquid-Phase Sintering: Materials sintered via liquid-phase methods often exhibit improved mechanical properties, including higher flexural strength and fracture toughness. The finer grain size and intergranular fracture mode contribute to these enhancements. Additionally, the lower sintering temperatures can help preserve the material's intrinsic properties.
In summary, the choice between solid-state and liquid-phase sintering depends on the material properties, desired microstructure, and mechanical performance. Solid-state sintering is suitable for materials that can be densified through diffusion, while liquid-phase sintering is advantageous for harder-to-densify materials, offering lower sintering temperatures, faster densification, and improved mechanical properties.
Summary Table:
Aspect | Solid-State Sintering | Liquid-Phase Sintering |
---|---|---|
Temperature | High temperatures (e.g., 1600°C for zirconia/alumina) | Lower temperatures due to the presence of a low-melting-point liquid phase |
Densification Mechanism | Relies on solid-state diffusion, slower process | Liquid phase enhances diffusion, faster particle rearrangement and bonding |
Pore Closure | Gradual, relies on slow diffusion; residual porosity possible | Accelerated by liquid phase, fewer residual pores |
Grain Size | Larger grains due to high temperatures | Smaller grains, finer microstructure |
Material Suitability | Suitable for zirconia, alumina, and other diffusion-friendly materials | Ideal for silicon nitride, silicon carbide, and harder-to-densify materials |
Mechanical Properties | Good density and high-temperature performance; potential grain growth reduces toughness | Improved flexural strength, fracture toughness, and finer microstructure |
Need help choosing the right sintering method for your materials? Contact our experts today!