Brazed joints are known for their strength and durability, making them a reliable choice for various applications. The strength of a brazed joint depends on factors such as the materials being joined, the filler metal used, and the brazing process itself. When done correctly, brazed joints can achieve strength comparable to or even exceeding that of the base materials. This is because brazing creates a metallurgical bond between the filler metal and the base materials, resulting in a joint that is resistant to mechanical stress, thermal cycling, and corrosion. Additionally, brazed joints distribute stress evenly across the joint, reducing the risk of failure. Overall, brazed joints are strong, reliable, and suitable for demanding applications in industries such as automotive, aerospace, and HVAC.
Key Points Explained:
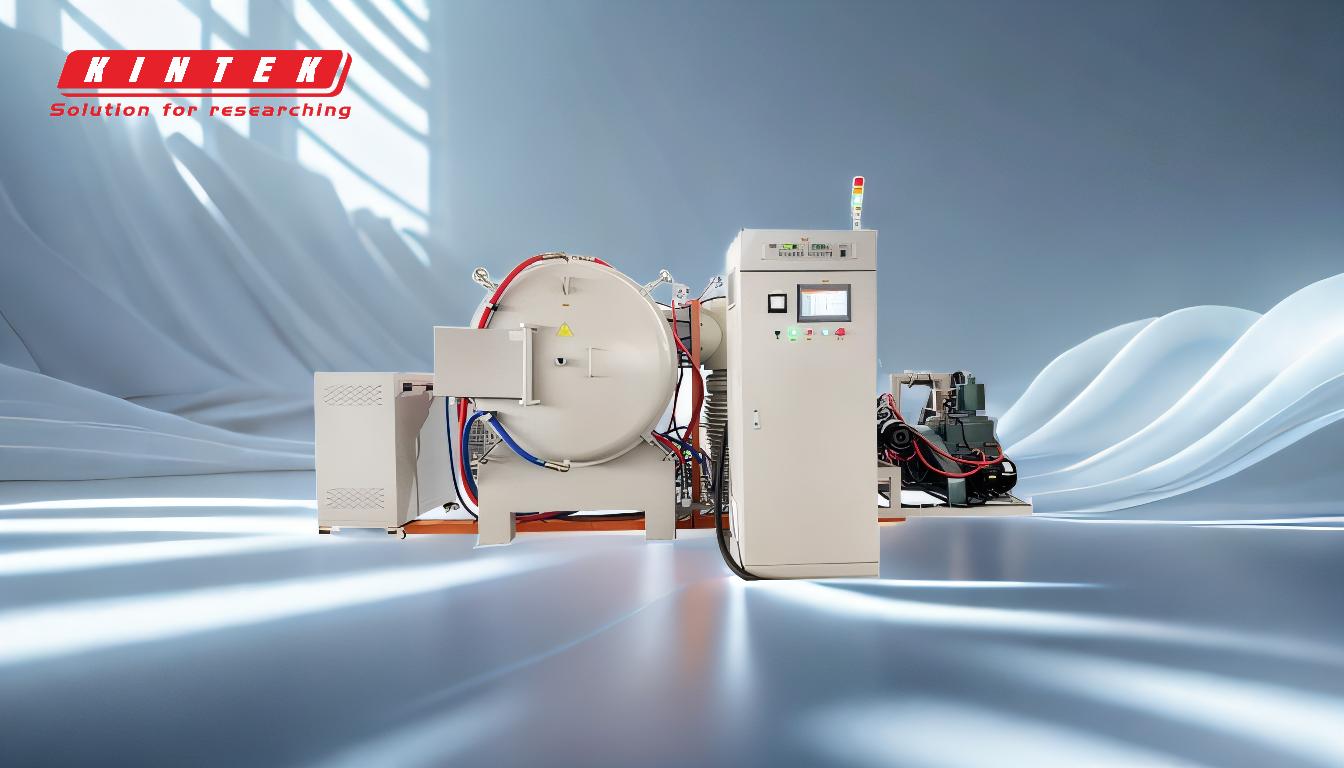
-
Strength of Brazed Joints:
- Brazed joints are inherently strong due to the metallurgical bond formed between the filler metal and the base materials. This bond is created through capillary action, which ensures the filler metal flows evenly and fills the joint completely.
- The strength of a brazed joint often approaches or exceeds the strength of the base materials, especially when proper brazing techniques and filler metals are used.
-
Factors Influencing Joint Strength:
- Base Materials: The compatibility of the base materials with the filler metal is critical. Materials with similar thermal expansion coefficients tend to produce stronger joints.
- Filler Metal: The choice of filler metal significantly impacts joint strength. Common filler metals include silver-based alloys, copper-based alloys, and nickel-based alloys, each suited for specific applications and materials.
- Joint Design: The design of the joint, including clearance and surface preparation, plays a crucial role. Proper clearance ensures optimal capillary action, while clean surfaces free of contaminants promote better bonding.
-
Stress Distribution:
- Brazed joints distribute stress evenly across the joint area, reducing localized stress concentrations that can lead to failure. This is particularly advantageous in applications subjected to mechanical loads or thermal cycling.
-
Resistance to Environmental Factors:
- Brazed joints exhibit excellent resistance to corrosion and thermal fatigue, making them suitable for harsh environments. The filler metal and base materials can be selected to match the environmental conditions, ensuring long-term durability.
-
Applications Across Industries:
- Brazed joints are widely used in industries such as automotive (e.g., radiators, air conditioning systems), aerospace (e.g., heat exchangers, turbine components), and HVAC (e.g., refrigeration systems). Their strength and reliability make them ideal for critical applications.
-
Comparison to Other Joining Methods:
- Compared to welding, brazing operates at lower temperatures, reducing the risk of thermal distortion and preserving the integrity of the base materials.
- Compared to soldering, brazing produces stronger joints due to the use of higher-melting-point filler metals and the formation of a metallurgical bond.
-
Testing and Quality Assurance:
- The strength of brazed joints can be verified through non-destructive testing methods such as ultrasonic testing, X-ray inspection, and dye penetrant testing. These methods ensure the joint's integrity and adherence to industry standards.
In summary, brazed joints are strong, durable, and versatile, making them a preferred choice for many industrial applications. Proper material selection, joint design, and brazing techniques are essential to achieving optimal joint strength and performance.
Summary Table:
Key Aspect | Details |
---|---|
Strength of Brazed Joints | Achieves strength comparable to or exceeding base materials. |
Key Factors | Base materials, filler metal, joint design, and brazing process. |
Stress Distribution | Evenly distributes stress, reducing failure risk. |
Resistance | Excellent resistance to corrosion, thermal fatigue, and mechanical stress. |
Applications | Automotive, aerospace, HVAC, and more. |
Testing Methods | Ultrasonic, X-ray, and dye penetrant testing for quality assurance. |
Need reliable brazed joints for your application? Contact our experts today for tailored solutions!