Annealing is not exclusive to steel; it is a versatile heat treatment process applicable to a wide range of metals, including copper, aluminium, and brass. The primary purpose of annealing is to alter a material's physical and sometimes chemical properties by relieving internal stresses, improving machinability, and enhancing ductility. This is achieved by heating the material above its recrystallization temperature, maintaining that temperature for a specific duration, and then cooling it at a controlled rate. Annealing is particularly useful for reversing work hardening, facilitating further forming processes, and increasing dimensional stability. While steel is commonly associated with annealing, other metals also benefit significantly from this process.
Key Points Explained:
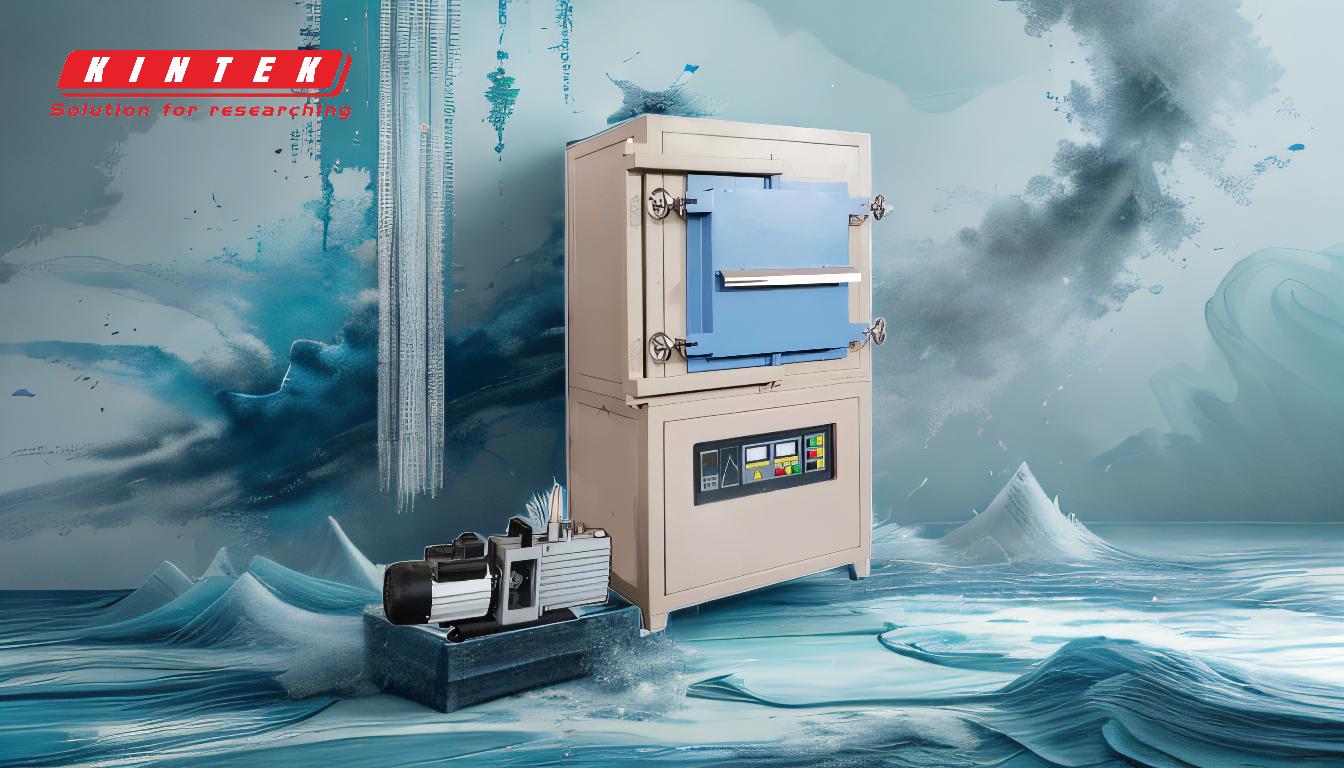
-
Annealing is Not Limited to Steel:
- While steel is one of the most commonly annealed materials, the process is also widely used for other metals such as copper, aluminium, and brass. These metals benefit from annealing in similar ways to steel, including stress relief and improved ductility.
-
Purpose of Annealing:
- Stress Relief: Annealing helps to relieve internal stresses that are induced during fabrication processes such as casting, welding, or cold working. This is crucial for preventing material failure and ensuring dimensional stability.
- Improved Ductility: By reversing the effects of work hardening, annealing makes materials more ductile, allowing for further forming processes like drawing or bending.
- Enhanced Machinability: Annealing can improve the machinability of metals, making them easier to cut, shape, or machine.
- Microstructural Changes: The process can also produce desired changes in the microstructure of the material, which can enhance mechanical or electrical properties.
-
Annealing Process:
- Heating: The material is heated to a temperature above its recrystallization temperature. This temperature varies depending on the type of metal.
- Holding: The material is held at this temperature for a specific duration to allow for the necessary microstructural changes.
- Cooling: The material is then cooled at a controlled rate. The cooling rate can vary depending on the desired properties and the type of metal being annealed.
-
Applications of Annealing:
- Cold Working: Annealing is often used after cold working processes to make the material more ductile and easier to work with.
- Welding: It is also used to relieve stresses that occur when welds solidify, preventing cracking and other defects.
- Casting: Annealing can help to remove internal stresses induced during the casting process, improving the overall quality of the cast part.
-
Benefits for Non-Steel Metals:
- Copper: Annealing copper improves its ductility, making it easier to draw into wires or form into complex shapes.
- Aluminium: Annealing aluminium can enhance its machinability and reduce internal stresses, making it more suitable for further processing.
- Brass: Annealing brass can improve its workability and reduce the risk of cracking during forming processes.
In summary, annealing is a critical heat treatment process that is not limited to steel. It is equally beneficial for other metals like copper, aluminium, and brass, offering advantages such as stress relief, improved ductility, and enhanced machinability. The process involves heating the material above its recrystallization temperature, holding it at that temperature, and then cooling it at a controlled rate. This makes annealing a versatile and essential process in the fabrication and processing of a wide range of metals.
Summary Table:
Aspect | Details |
---|---|
Applicable Metals | Steel, copper, aluminium, brass |
Purpose | Stress relief, improved ductility, enhanced machinability |
Process | Heating above recrystallization temp, holding, controlled cooling |
Applications | Cold working, welding, casting |
Benefits for Non-Steel | Improved ductility (copper), enhanced machinability (aluminium), reduced cracking (brass) |
Want to optimize your metal processing with annealing? Contact our experts today!