Annealing and heat treating are related processes, but they are not the same. Annealing is a specific type of heat treatment focused on softening materials, improving ductility, and refining microstructure. Heat treating, on the other hand, is a broader category that includes various processes like tempering, hardening, quenching, and annealing. While annealing aims to make materials softer and more workable, other heat treatment methods may focus on increasing hardness, strength, or other mechanical properties. Understanding the differences between these processes is crucial for selecting the right treatment for specific material requirements.
Key Points Explained:
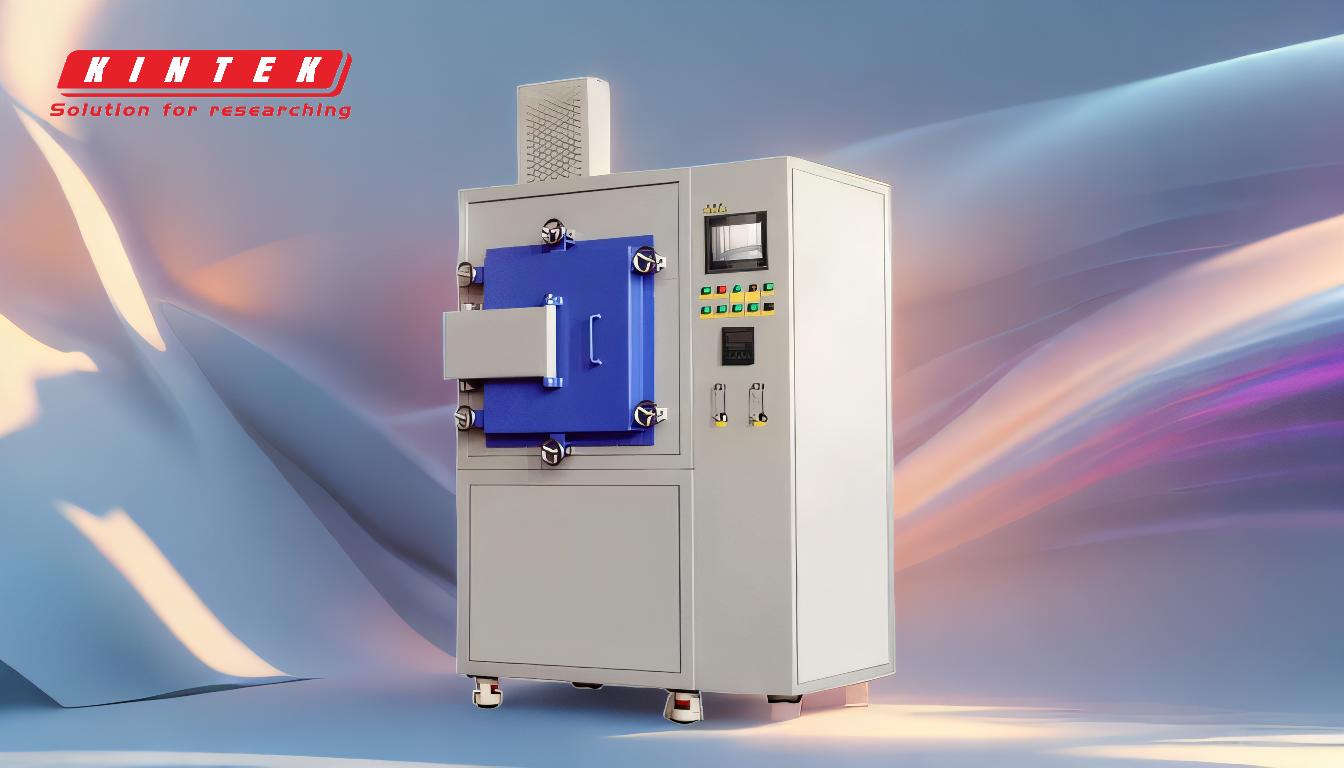
-
Definition of Heat Treating:
- Heat treating is a general term that encompasses a range of processes used to alter the physical and mechanical properties of materials, primarily metals. These processes involve heating materials to specific temperatures and then cooling them in controlled ways to achieve desired outcomes such as increased hardness, improved strength, or enhanced ductility.
-
Definition of Annealing:
- Annealing is a specific type of heat treatment process where materials are heated to a desired temperature, held for a specific period, and then slowly or rapidly cooled. The primary goal of annealing is to soften the material, improve its ductility, and refine its grain structure. This makes the material easier to machine and reduces internal stresses.
-
Purpose of Annealing:
- The main purpose of annealing is to make materials softer and more workable. This is achieved by heating the material to a temperature above or slightly below its transformation range and then allowing it to cool slowly. This process helps in:
- Refining the grain microstructure, making it more uniform.
- Improving ductility for further machining.
- Reducing potential stresses in castings.
- The main purpose of annealing is to make materials softer and more workable. This is achieved by heating the material to a temperature above or slightly below its transformation range and then allowing it to cool slowly. This process helps in:
-
Types of Annealing:
- There are three primary types of annealing:
- Full Annealing: Involves heating the material to a temperature above its upper critical temperature, holding it there for a period, and then allowing it to cool slowly in the furnace. This process results in a soft, coarse-grained structure.
- Process Annealing: This is used to soften the material for further cold working. It involves heating the material to a temperature below the lower critical temperature and then cooling it.
- Spheroidizing: This process involves heating the material to a temperature just below the lower critical temperature and holding it there for an extended period. This results in the formation of spheroidal carbides, which improve machinability.
- There are three primary types of annealing:
-
Heat Treating vs. Annealing:
- While annealing is a subset of heat treating, the two are not the same. Heat treating includes a variety of processes designed to achieve different material properties, such as:
- Hardening: Increasing the hardness and strength of the material.
- Tempering: Reducing brittleness and improving toughness after hardening.
- Quenching: Rapidly cooling the material to achieve high hardness.
- Annealing, in contrast, is specifically aimed at softening the material and improving its ductility and machinability.
- While annealing is a subset of heat treating, the two are not the same. Heat treating includes a variety of processes designed to achieve different material properties, such as:
-
Applications of Annealing:
- Annealing is commonly used in industries where materials need to be soft and workable for further processing. Examples include:
- Manufacturing of steel and other metals.
- Production of castings and forgings.
- Preparation of materials for cold working processes like drawing, stamping, and forming.
- Annealing is commonly used in industries where materials need to be soft and workable for further processing. Examples include:
-
Cooling Methods:
- The cooling method is a critical aspect of both annealing and other heat treatment processes:
- Annealing: Typically involves slow cooling, either in the furnace or in air, to allow the material to achieve a soft and uniform structure.
- Other Heat Treatments: May involve rapid cooling (quenching) or controlled cooling (tempering) to achieve specific mechanical properties.
- The cooling method is a critical aspect of both annealing and other heat treatment processes:
-
Material Suitability:
- Both annealing and other heat treatment processes are suitable for a wide range of materials, including ferrous and non-ferrous alloys. The choice of process depends on the desired outcome and the specific properties of the material being treated.
In summary, while annealing is a specific type of heat treatment aimed at softening and improving the ductility of materials, heat treating is a broader category that includes various processes designed to achieve a range of material properties. Understanding the differences between these processes is essential for selecting the appropriate treatment for specific applications.
Summary Table:
Aspect | Annealing | Heat Treating |
---|---|---|
Definition | A specific heat treatment process to soften materials and improve ductility. | A broader category of processes to alter material properties like hardness. |
Purpose | Soften materials, refine microstructure, and reduce internal stresses. | Achieve various properties like hardness, strength, or toughness. |
Cooling Method | Slow cooling (furnace or air). | Varies: rapid (quenching) or controlled (tempering). |
Applications | Used in steel manufacturing, castings, and cold working processes. | Includes hardening, tempering, and quenching for diverse industrial applications. |
Material Suitability | Suitable for ferrous and non-ferrous alloys. | Suitable for a wide range of materials, depending on desired outcomes. |
Need help choosing the right heat treatment process? Contact our experts today for tailored solutions!
For specialized processes like vacuum annealing furnace or vacuum hardening furnace, consult with our team for advanced solutions.