Yes, PVD (Physical Vapor Deposition) is a coating process. It involves vaporizing a solid material in a vacuum and depositing it onto a substrate to form a thin, durable, and functional layer. This process is widely used to enhance the surface properties of materials, such as improving hardness, wear resistance, and chemical stability, while also allowing for customization of appearance. PVD coatings are typically very thin (0.5–5 μm) and can be composed of metals, metal-ceramics, or other compounds, depending on the application. The process is environmentally friendly and offers significant advantages over traditional coating methods like electroplating.
Key Points Explained:
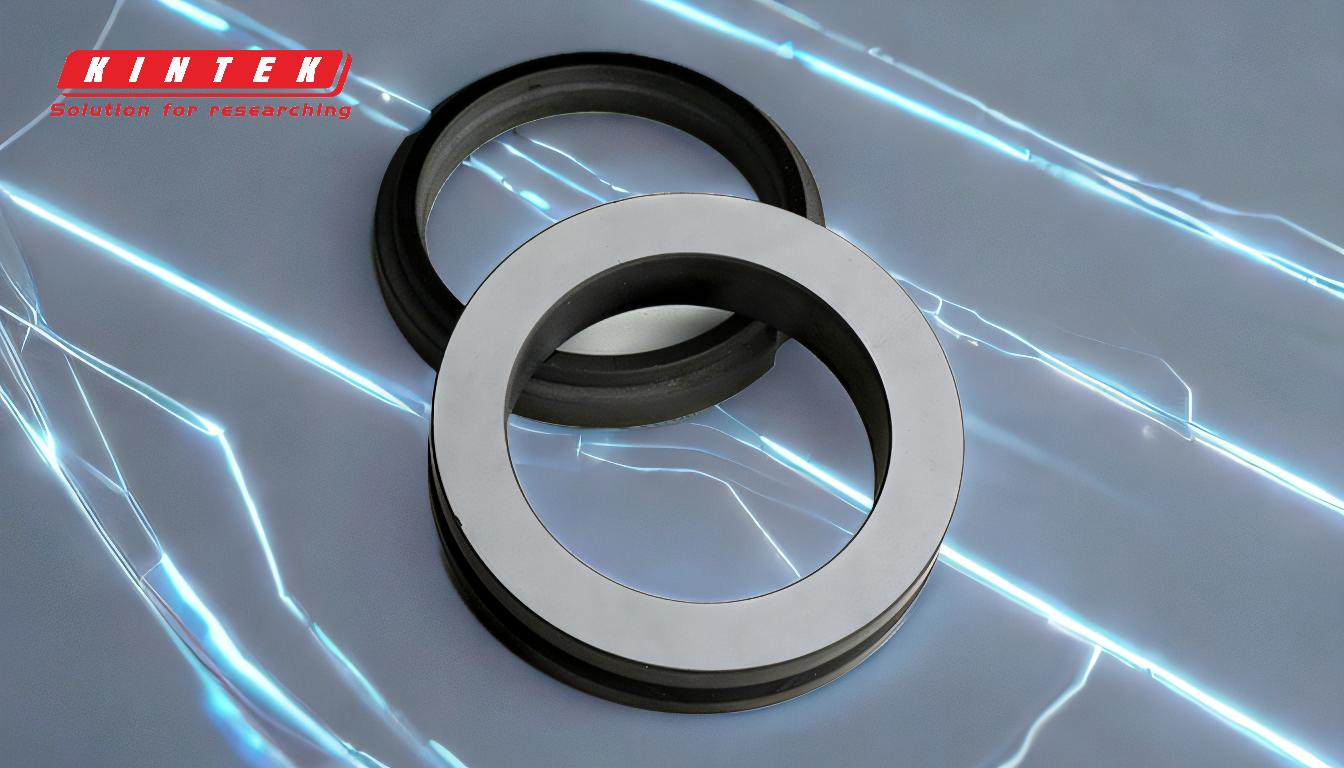
-
Definition of PVD Coating:
- PVD stands for Physical Vapor Deposition, a process where a solid material is vaporized in a vacuum and deposited onto a substrate to form a thin, bonded layer.
- It is a modern coating technique used to enhance the surface properties of materials, such as hardness, wear resistance, and chemical stability.
-
How PVD Coating Works:
- The process involves four key stages: evaporation, transportation, reaction, and deposition.
- A solid material (target) is vaporized using techniques like sputtering, cathodic arc, or electron beam evaporation.
- The vaporized material is transported through a vacuum and condenses onto the substrate (workpiece), forming a thin film.
-
Characteristics of PVD Coatings:
- PVD coatings are extremely thin, typically ranging from 0.5 to 5 micrometers (μm).
- They are highly durable and provide significant improvements in properties such as surface hardness, wear resistance, and chemical stability.
- The coatings can be customized to achieve specific mechanical, chemical, and optical properties.
-
Materials Used in PVD Coating:
- Common materials include metals like titanium, zirconium, and chromium.
- Reactive gases such as nitrogen, acetylene, or oxygen are often introduced during the process to form compound coatings like metal nitrides or oxides.
-
Applications of PVD Coatings:
- PVD coatings are applied to metals, ceramics, and polymers across various industries.
- They are used to improve the durability and functionality of tools, medical devices, automotive components, and decorative items.
-
Advantages of PVD Coating:
- Environmentally friendly compared to traditional coating methods like electroplating.
- Provides a strong bond between the coating and the substrate, ensuring long-lasting performance.
- Allows for precise control over coating composition and thickness, enabling tailored solutions for specific applications.
-
Comparison to Other Coating Methods:
- PVD is considered an alternative to electroplating, offering superior durability, adhesion, and environmental benefits.
- Unlike electroplating, PVD does not involve hazardous chemicals or produce harmful byproducts.
-
Technical Details of the Process:
- The process occurs in a vacuum chamber at a working pressure typically between 10^-2 to 10^-4 mbar.
- Energetic positively charged ions bombard the substrate to promote high-density coatings.
- Reactive gases can be introduced to modify the composition of the coating, resulting in tailored properties.
By understanding these key points, it becomes clear that PVD is not just a coating but a highly advanced and versatile process that delivers exceptional performance and customization for a wide range of applications.
Summary Table:
Aspect | Details |
---|---|
Definition | Physical Vapor Deposition (PVD) vaporizes solid material in a vacuum. |
Process Stages | Evaporation, transportation, reaction, deposition. |
Coating Thickness | 0.5–5 micrometers (μm). |
Materials Used | Metals (titanium, zirconium, chromium), reactive gases (nitrogen, oxygen). |
Applications | Tools, medical devices, automotive parts, decorative items. |
Advantages | Eco-friendly, durable, customizable, strong adhesion. |
Comparison | Superior to electroplating in durability and environmental impact. |
Ready to enhance your materials with PVD coating? Contact our experts today to learn more!