The melting range of a substance is influenced by several factors, including its chemical composition, purity, molecular structure, and external conditions such as pressure and heating rate. Impurities typically lower the melting point and broaden the melting range, while a well-defined molecular structure often results in a sharper melting point. External factors like pressure can shift the melting range, and the rate at which heat is applied can affect the observed melting behavior. Understanding these factors is crucial for material selection, quality control, and process optimization in industries like pharmaceuticals, metallurgy, and materials science.
Key Points Explained:
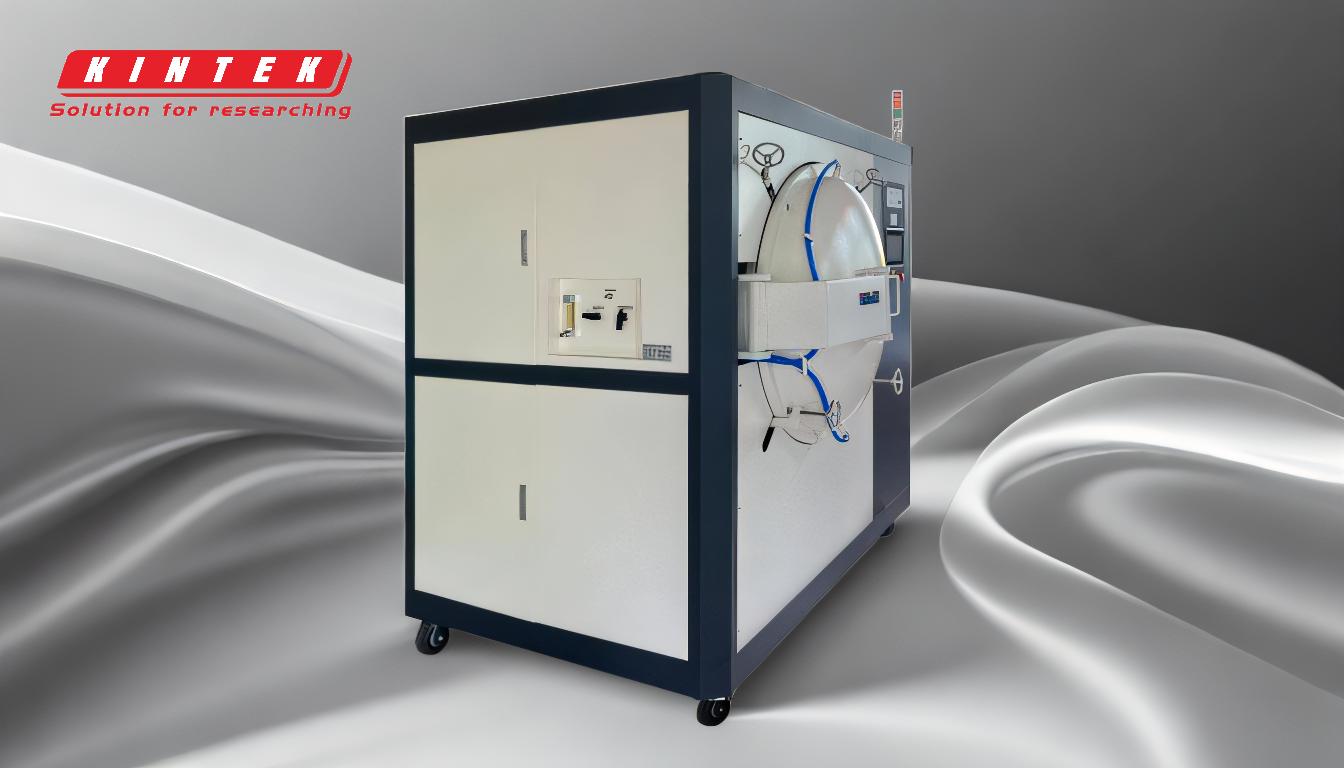
-
Chemical Composition:
- The melting range is directly influenced by the chemical composition of a substance. Pure substances with a single chemical component typically have a sharp melting point, whereas mixtures or compounds with multiple components exhibit a broader melting range.
- For example, alloys or polymers with varying compositions will have different melting behaviors compared to pure metals or single-component polymers.
-
Purity:
- The presence of impurities significantly affects the melting range. Impurities disrupt the regular crystalline structure of a substance, lowering its melting point and broadening the range over which melting occurs.
- In pharmaceuticals, for instance, even trace impurities can alter the melting behavior of active ingredients, impacting drug stability and performance.
-
Molecular Structure:
- The molecular arrangement and bonding within a substance play a critical role in determining its melting range. Substances with strong intermolecular forces, such as hydrogen bonding or ionic interactions, tend to have higher melting points and narrower melting ranges.
- Crystalline materials, which have a well-defined structure, usually melt at a specific temperature, while amorphous materials, lacking a regular structure, exhibit a broader melting range.
-
External Pressure:
- Changes in external pressure can shift the melting range. According to the Clausius-Clapeyron equation, increasing pressure generally raises the melting point of substances that expand upon melting (e.g., water) and lowers it for those that contract (e.g., most metals).
- This factor is particularly relevant in high-pressure industrial processes or geological studies.
-
Heating Rate:
- The rate at which heat is applied can influence the observed melting range. Rapid heating may lead to a higher apparent melting point due to thermal lag, while slow heating allows for more accurate determination of the melting range.
- In laboratory settings, controlling the heating rate is essential for precise measurements, especially in differential scanning calorimetry (DSC) experiments.
-
Particle Size and Morphology:
- Smaller particles or nanostructured materials often exhibit a lower melting point compared to bulk materials due to increased surface energy. This phenomenon is known as the Gibbs-Thomson effect.
- Morphology, such as the presence of defects or grain boundaries, can also influence the melting behavior by providing sites for easier initiation of melting.
-
Environmental Conditions:
- Environmental factors like humidity or the presence of reactive gases can alter the melting range. For example, hygroscopic materials may absorb moisture, which can lower their melting point and broaden the range.
-
Thermal History:
- The thermal history of a material, including its cooling rate during solidification, can affect its melting range. Rapid cooling may result in a metastable structure with a different melting behavior compared to a slowly cooled, equilibrium structure.
By understanding these factors, manufacturers and researchers can better predict and control the melting behavior of materials, ensuring optimal performance in applications ranging from drug formulation to metallurgical processes.
Summary Table:
Factor | Impact on Melting Range |
---|---|
Chemical Composition | Pure substances have sharp melting points; mixtures exhibit broader ranges. |
Purity | Impurities lower melting points and broaden the range. |
Molecular Structure | Strong intermolecular forces result in higher melting points and narrower ranges. |
External Pressure | Pressure shifts melting range based on substance behavior (expansion or contraction). |
Heating Rate | Rapid heating may increase apparent melting point; slow heating ensures accuracy. |
Particle Size/Morphology | Smaller particles or nanostructures melt at lower points due to increased surface energy. |
Environmental Conditions | Humidity or reactive gases can alter melting behavior. |
Thermal History | Cooling rate during solidification affects melting range and material stability. |
Need help understanding how melting range impacts your materials? Contact our experts today for tailored solutions!