Brazing is a versatile and efficient joining method that offers numerous advantages over other techniques like welding or soldering. It involves joining materials using a filler metal that melts at a lower temperature than the base metals, ensuring that the base materials remain intact. This process is widely used in industries such as automotive, aerospace, and electronics due to its ability to create strong, durable, and aesthetically pleasing joints. Below, we explore the key advantages of brazing in detail.
Key Points Explained:
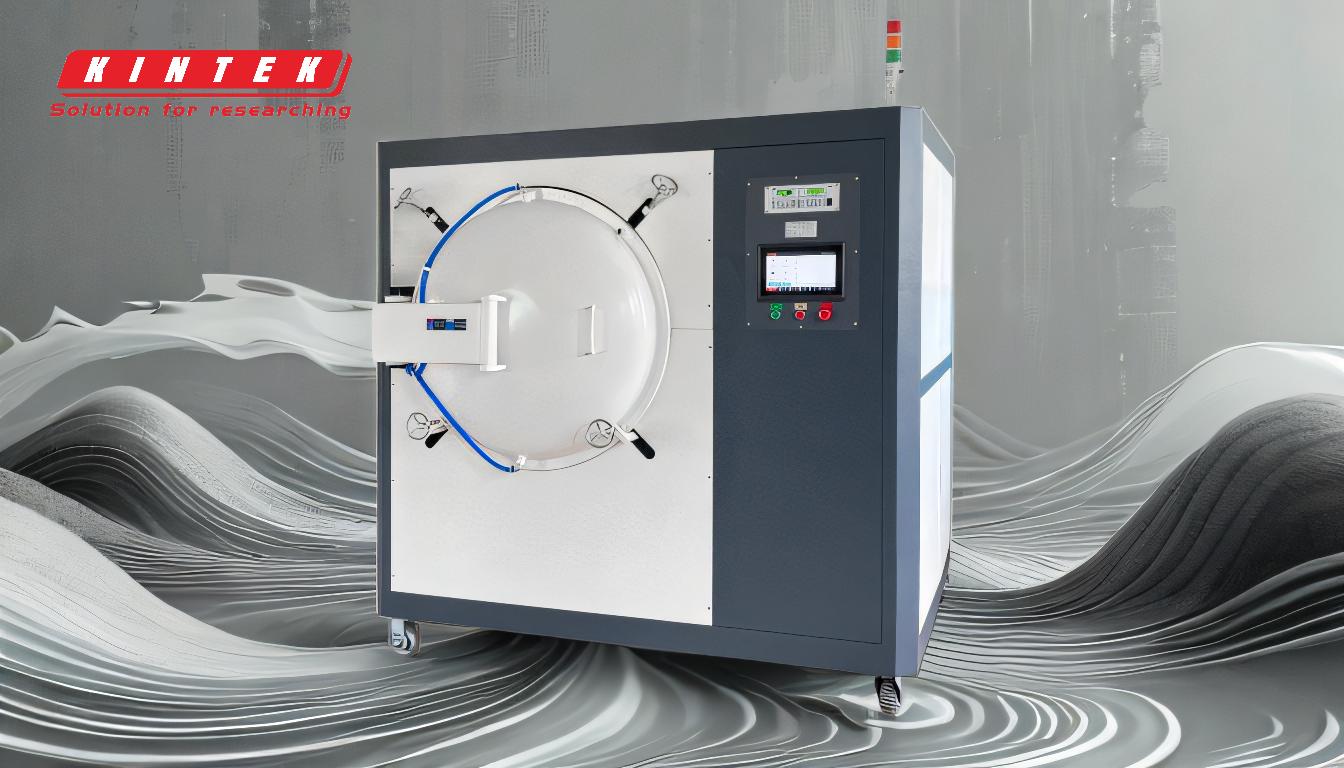
-
Preservation of Base Metal Integrity
- Brazing does not melt the base metals, which means the structural integrity and mechanical properties of the components remain unchanged.
- This allows for close tolerances and precise assembly, making it ideal for applications requiring high accuracy.
- Unlike welding, which can weaken the base material due to melting, brazing uses a filler metal to solidify the joint, resulting in a strong and durable connection.
-
Ability to Join Dissimilar Materials
- Brazing can effectively join dissimilar materials, including metals and nonmetals, which is often challenging with other methods.
- For example, it can bond ceramics to metals, enabling the creation of hybrid components with unique properties.
- This versatility makes brazing a cost-effective solution for complex assemblies in industries like electronics and aerospace.
-
Reduced Thermal Distortion
- Brazing operates at lower temperatures compared to welding, minimizing thermal distortion and stress in the joined parts.
- Uniform heating and precise temperature control in processes like vacuum brazing further reduce the risk of warping or deformation.
- This is particularly beneficial for high-precision assemblies where dimensional stability is critical.
-
Clean and Aesthetically Pleasing Joints
- Brazing, especially in controlled environments like vacuum or hydrogen brazing, produces clean, flux-free joints free from oxidation or contamination.
- The process eliminates hydrocarbon residues and improves capillary action, resulting in smooth and visually appealing joints.
- This makes brazing suitable for applications where both functionality and appearance are important.
-
High Efficiency and Scalability
- Brazing is highly efficient, allowing for the simultaneous joining of multiple seams in a single operation.
- It is well-suited for high-volume mass production, as it can be automated and integrated into manufacturing processes.
- Techniques like vacuum brazing also support step brazing using multiple alloys and enable heat treatments like hardening or annealing in the same cycle, saving time and costs.
In summary, brazing stands out as a superior joining method due to its ability to preserve base metal integrity, join dissimilar materials, minimize thermal distortion, produce clean joints, and support efficient mass production. These advantages make it an indispensable process in modern manufacturing and engineering applications.
Summary Table:
Advantage | Description |
---|---|
Preservation of Base Metal Integrity | Base metals remain intact, ensuring structural integrity and precise assembly. |
Ability to Join Dissimilar Materials | Bonds metals and nonmetals, ideal for hybrid components in aerospace and electronics. |
Reduced Thermal Distortion | Lower temperatures minimize warping and stress, critical for high-precision parts. |
Clean and Aesthetically Pleasing Joints | Produces smooth, flux-free joints, perfect for functional and visually appealing applications. |
High Efficiency and Scalability | Enables mass production with automation and cost-effective manufacturing processes. |
Unlock the full potential of brazing for your projects—contact us today to learn more!