Annealing is a heat treatment process used to alter the physical and sometimes chemical properties of a material, typically metals, to improve ductility, reduce hardness, and relieve internal stresses. The process involves three distinct stages: Recovery, Recrystallization, and Grain Growth. Each stage occurs as the material is heated to specific temperatures, held for a certain duration, and then cooled slowly. These stages help repair defects in the crystalline structure, form new grains, and enhance the material's overall mechanical properties. Understanding these stages is crucial for achieving the desired material characteristics in industrial applications.
Key Points Explained:
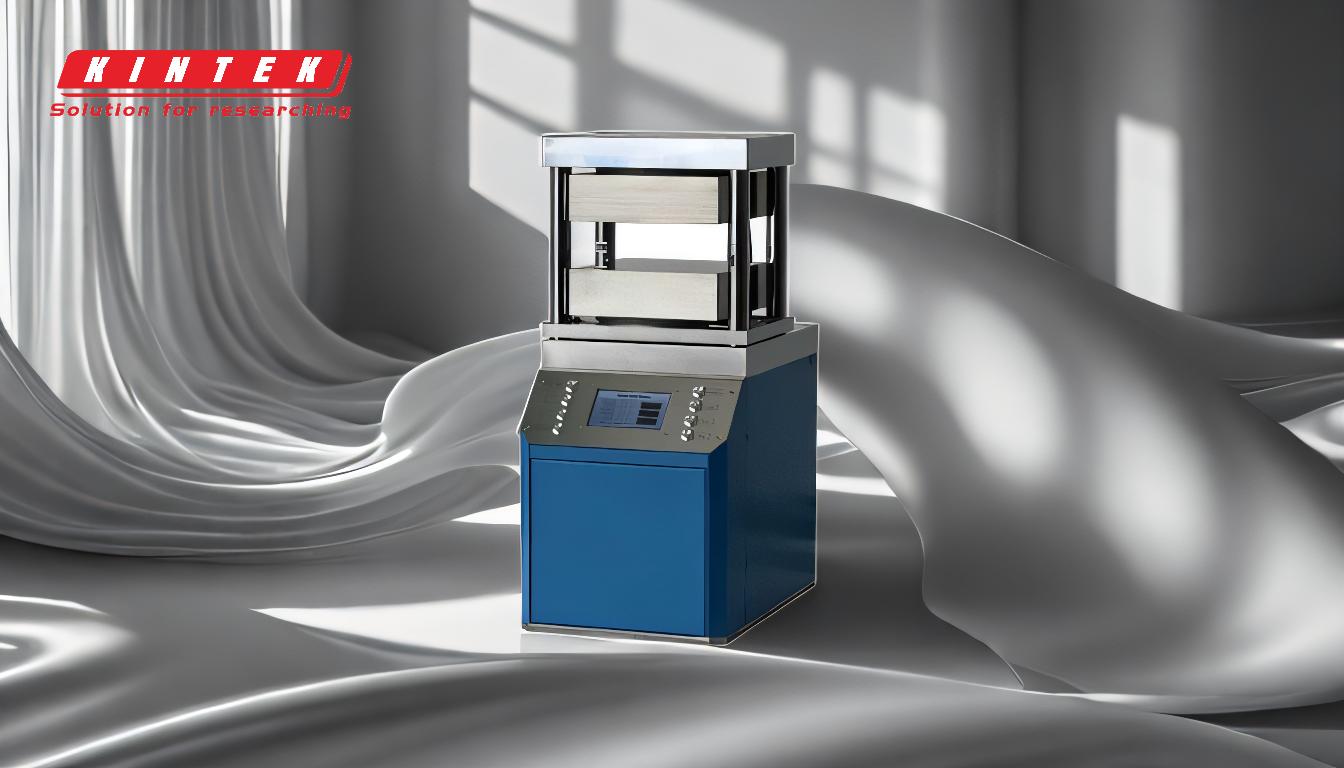
-
Recovery Stage
- Purpose: The primary goal of the recovery stage is to relieve internal stresses within the material without significantly altering its microstructure.
- Process: During this stage, the material is heated to a temperature below its recrystallization temperature. This allows dislocations (defects in the crystal lattice) to move and rearrange, reducing internal stresses.
- Outcome: The material becomes less brittle, and some of its mechanical properties, such as hardness, may slightly decrease. However, the overall grain structure remains largely unchanged.
- Importance for Purchasers: For equipment or consumable purchasers, understanding this stage ensures that the material is prepared for further processing, such as recrystallization, without compromising its structural integrity.
-
Recrystallization Stage
- Purpose: The recrystallization stage aims to form new, strain-free grains by heating the material above its recrystallization temperature but below its melting point.
- Process: At this stage, the material is held at a high temperature, allowing new grains to nucleate and grow. These new grains replace the deformed and stressed grains formed during prior mechanical working (e.g., rolling or forging).
- Outcome: The material becomes softer and more ductile, with a refined grain structure. This stage is critical for improving the material's workability and mechanical properties.
- Importance for Purchasers: For purchasers, this stage ensures that the material achieves the desired balance of strength and ductility, making it suitable for further manufacturing processes or end-use applications.
-
Grain Growth Stage
- Purpose: The grain growth stage focuses on allowing the newly formed grains to grow larger, further enhancing the material's ductility and reducing its hardness.
- Process: After recrystallization, the material is either held at a high temperature or cooled slowly, enabling the grains to grow. Larger grains generally result in a more ductile material.
- Outcome: The material becomes more pliable and easier to work with, though excessive grain growth can lead to reduced strength.
- Importance for Purchasers: For purchasers, this stage ensures that the material is optimized for specific applications, such as forming or shaping, where ductility is more critical than hardness.
By understanding these three stages, purchasers can make informed decisions about the annealing process and its impact on material properties. This knowledge is particularly valuable when selecting materials for specific applications, ensuring that the final product meets the required performance standards.
Summary Table:
Stage | Purpose | Process | Outcome | Importance for Purchasers |
---|---|---|---|---|
Recovery | Relieve internal stresses without altering microstructure. | Heat below recrystallization temperature; dislocations rearrange. | Material becomes less brittle; hardness slightly decreases. | Prepares material for further processing without compromising structural integrity. |
Recrystallization | Form new, strain-free grains to improve workability and mechanical properties. | Heat above recrystallization temperature; new grains nucleate and grow. | Material becomes softer, more ductile, with refined grain structure. | Ensures material achieves desired balance of strength and ductility for manufacturing. |
Grain Growth | Enhance ductility by allowing grains to grow larger. | Hold at high temperature or cool slowly; grains grow larger. | Material becomes more pliable; excessive growth can reduce strength. | Optimizes material for applications requiring ductility over hardness, such as shaping. |
Need help selecting the right annealing process for your materials? Contact our experts today for tailored solutions!