Tempering is a critical heat treatment process that follows quenching or hardening to improve the mechanical properties of metals, particularly steel. It reduces brittleness, removes internal stresses, and enhances toughness, ductility, and grain size. By heating the metal to a specific temperature below its transformation range and then cooling it, tempering achieves a balance between hardness and toughness, making the material more suitable for practical applications. This process also improves wear resistance and regulates the mechanical properties of the material, ensuring it meets the desired performance criteria.
Key Points Explained:
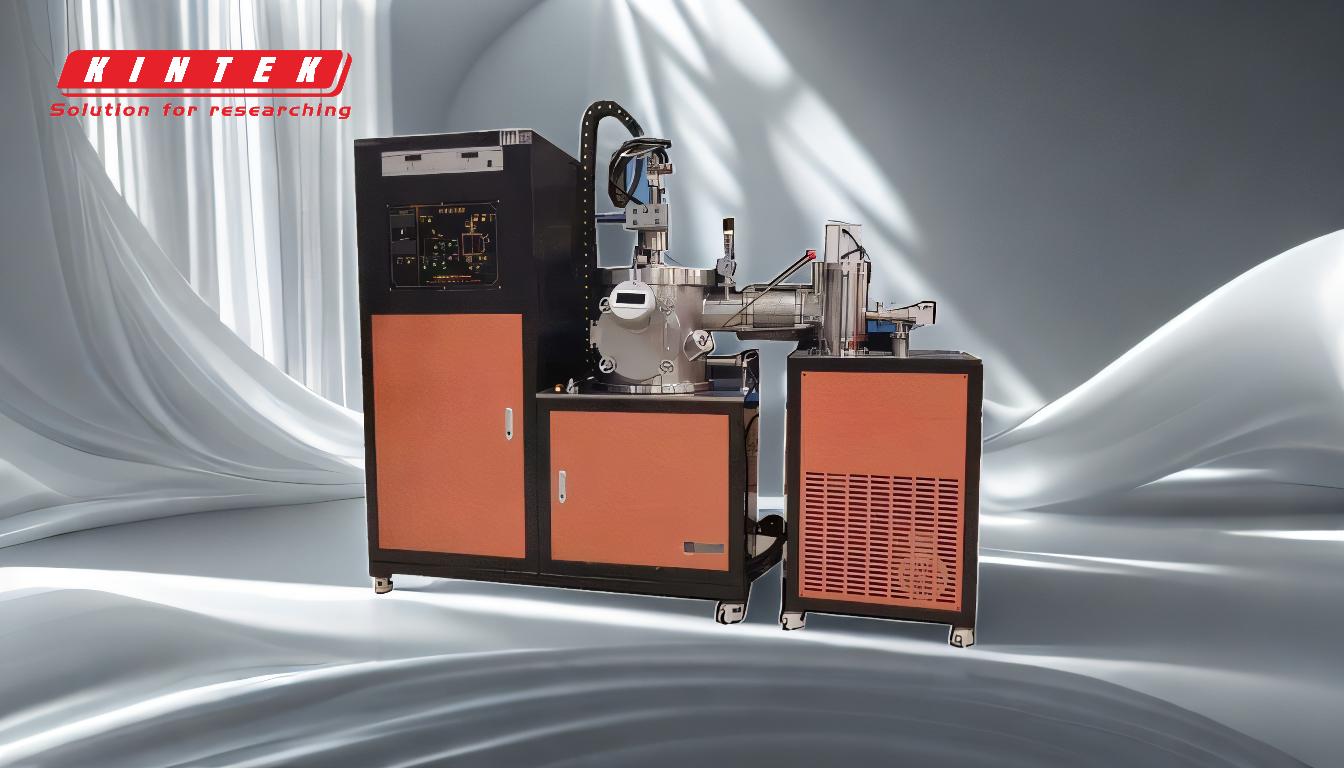
-
Reduction of Brittleness:
- After quenching, metals like steel become extremely hard but also brittle, making them prone to cracking or breaking under stress. Tempering reduces this brittleness by transforming the hard, unstable martensite structure into softer and tougher phases like troostite or sorbite. This makes the material more durable and less likely to fail under mechanical stress.
-
Removal of Internal Stresses:
- Rapid cooling during quenching introduces internal strains and stresses within the material. Tempering relieves these stresses by allowing the metal to undergo controlled heating and cooling, which redistributes the internal energy and stabilizes the microstructure. This results in a more uniform and stress-free material.
-
Enhanced Toughness and Ductility:
- Tempering increases the toughness and ductility of the metal, making it more resistant to impact and deformation. This is achieved by altering the grain structure and reducing hardness to a level that balances strength with flexibility. For example, troostite provides a softer and tougher structure, while sorbite offers greater ductility.
-
Improved Grain Size:
- The process of tempering promotes grain growth, which can enhance the material's mechanical properties. Larger grains improve ductility and toughness, making the metal more suitable for applications requiring resilience and resistance to wear.
-
Regulation of Hardness-to-Toughness Ratio:
- Tempering allows for precise control over the hardness and toughness of the material. By adjusting the tempering temperature and duration, manufacturers can tailor the material's properties to meet specific application requirements. For instance, higher tempering temperatures generally result in softer but tougher materials, while lower temperatures retain more hardness.
-
Complementary to Other Heat Treatments:
- Tempering works in conjunction with processes like vacuum quenching or normalizing to further enhance the material's properties. It ensures that the benefits of hardening are fully realized by refining the microstructure and optimizing mechanical performance.
-
Preparation of Tools and Components:
- In applications like crucible preparation, tempering removes moisture and stabilizes the material, making it ready for use. This ensures the longevity and reliability of tools and components subjected to high temperatures or mechanical stress.
-
Versatility Across Materials:
- While tempering is most commonly associated with steel, it can also be applied to other ferrous alloys and heat-treated metals. This versatility makes it a widely used process in industries ranging from automotive to aerospace.
By addressing brittleness, internal stresses, and mechanical properties, tempering plays a vital role in ensuring the reliability, durability, and performance of metal components in various industrial applications.
Summary Table:
Key Benefits of Tempering | Description |
---|---|
Reduction of Brittleness | Converts hard, brittle martensite into softer, tougher phases like troostite. |
Removal of Internal Stresses | Relieves stresses from quenching, stabilizing the microstructure. |
Enhanced Toughness & Ductility | Balances hardness and flexibility for impact resistance. |
Improved Grain Size | Promotes grain growth, enhancing ductility and toughness. |
Hardness-to-Toughness Control | Adjusts properties by varying tempering temperature and duration. |
Complementary to Heat Treatments | Works with quenching or normalizing for optimized performance. |
Preparation of Tools | Stabilizes materials for high-temperature or mechanical stress applications. |
Versatility Across Materials | Applicable to steel, ferrous alloys, and other heat-treated metals. |
Discover how tempering can optimize your metal components—contact our experts today!