Tempering is a heat treatment process used to improve the toughness of iron-based alloys, such as steel, by reducing brittleness and relieving internal stresses. The conditions for tempering depend on the material, desired properties, and application. Key factors include temperature, time, cooling rate, and the initial state of the material. Tempering typically follows quenching, where the material is heated to a high temperature and rapidly cooled. The tempering temperature is usually below the critical temperature of the material and ranges from 150°C to 700°C, depending on the desired balance between hardness and toughness. The process duration and cooling method also play critical roles in achieving the desired mechanical properties.
Key Points Explained:
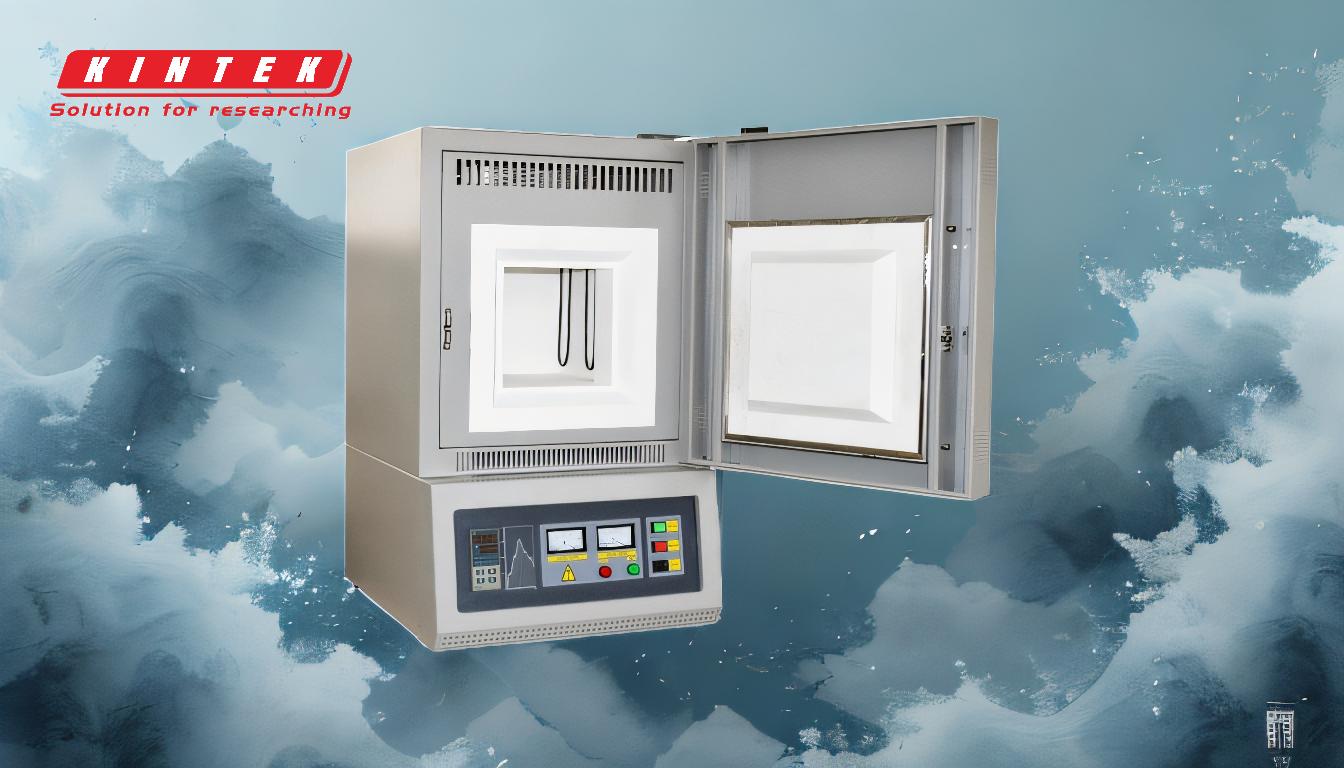
-
Purpose of Tempering:
- Tempering is performed to reduce the brittleness caused by quenching and to improve toughness and ductility.
- It relieves internal stresses and stabilizes the microstructure of the material.
-
Temperature Range:
- Tempering temperatures typically range from 150°C to 700°C, depending on the material and desired properties.
- Lower temperatures (150°C–250°C) are used for high hardness and wear resistance.
- Higher temperatures (400°C–700°C) are used for increased toughness and reduced hardness.
-
Time Duration:
- The material is held at the tempering temperature for a specific duration, usually ranging from 30 minutes to several hours.
- Longer durations allow for more complete stress relief and microstructural changes.
-
Cooling Rate:
- After tempering, the material is cooled slowly, often in still air, to avoid introducing new stresses.
- Rapid cooling can lead to residual stresses and reduced toughness.
-
Initial Material State:
- Tempering is performed after quenching, which hardens the material by forming a martensitic structure.
- The initial hardness and microstructure of the material influence the tempering conditions and outcomes.
-
Material-Specific Considerations:
- Different alloys require different tempering conditions. For example:
- Tool steels are tempered at higher temperatures to achieve a balance of hardness and toughness.
- Spring steels are tempered at moderate temperatures to maintain elasticity.
- Different alloys require different tempering conditions. For example:
-
Desired Mechanical Properties:
- The tempering conditions are tailored to achieve specific mechanical properties, such as:
- Hardness: Controlled by tempering temperature and time.
- Toughness: Improved by higher tempering temperatures.
- Ductility: Enhanced through stress relief and microstructural changes.
- The tempering conditions are tailored to achieve specific mechanical properties, such as:
-
Application-Specific Requirements:
- The intended use of the material determines the tempering conditions. For example:
- Cutting tools require high hardness and wear resistance, so they are tempered at lower temperatures.
- Structural components need higher toughness and are tempered at higher temperatures.
- The intended use of the material determines the tempering conditions. For example:
-
Monitoring and Control:
- Precise control of temperature and time is critical to achieving consistent results.
- Advanced furnaces with temperature sensors and timers are used to ensure accuracy.
-
Post-Tempering Treatments:
- Additional treatments, such as stress relieving or surface hardening, may be applied after tempering to further enhance properties.
By carefully selecting and controlling these conditions, tempering can significantly improve the performance and durability of materials in various applications.
Summary Table:
Key Factor | Details |
---|---|
Temperature Range | 150°C to 700°C, depending on material and desired properties |
Time Duration | 30 minutes to several hours for stress relief and microstructural changes |
Cooling Rate | Slow cooling (e.g., still air) to avoid residual stresses |
Initial Material State | Performed after quenching to harden material and form martensitic structure |
Desired Properties | Balance hardness, toughness, and ductility based on application needs |
Optimize your tempering process for superior material performance—contact our experts today!