Ceramic mold casting, while advantageous for certain applications, has several notable disadvantages. These include limitations in production scalability, non-reusability of the ceramic material, challenges in maintaining tight dimensional tolerances, and the need for additional machining and polishing. Additionally, the process involves a time-intensive cooling phase, which can slow down production timelines. These factors make ceramic mold casting less cost-effective for large-scale production runs and more suitable for small- to medium-sized batches, particularly for ferrous and high-temperature non-ferrous materials.
Key Points Explained:
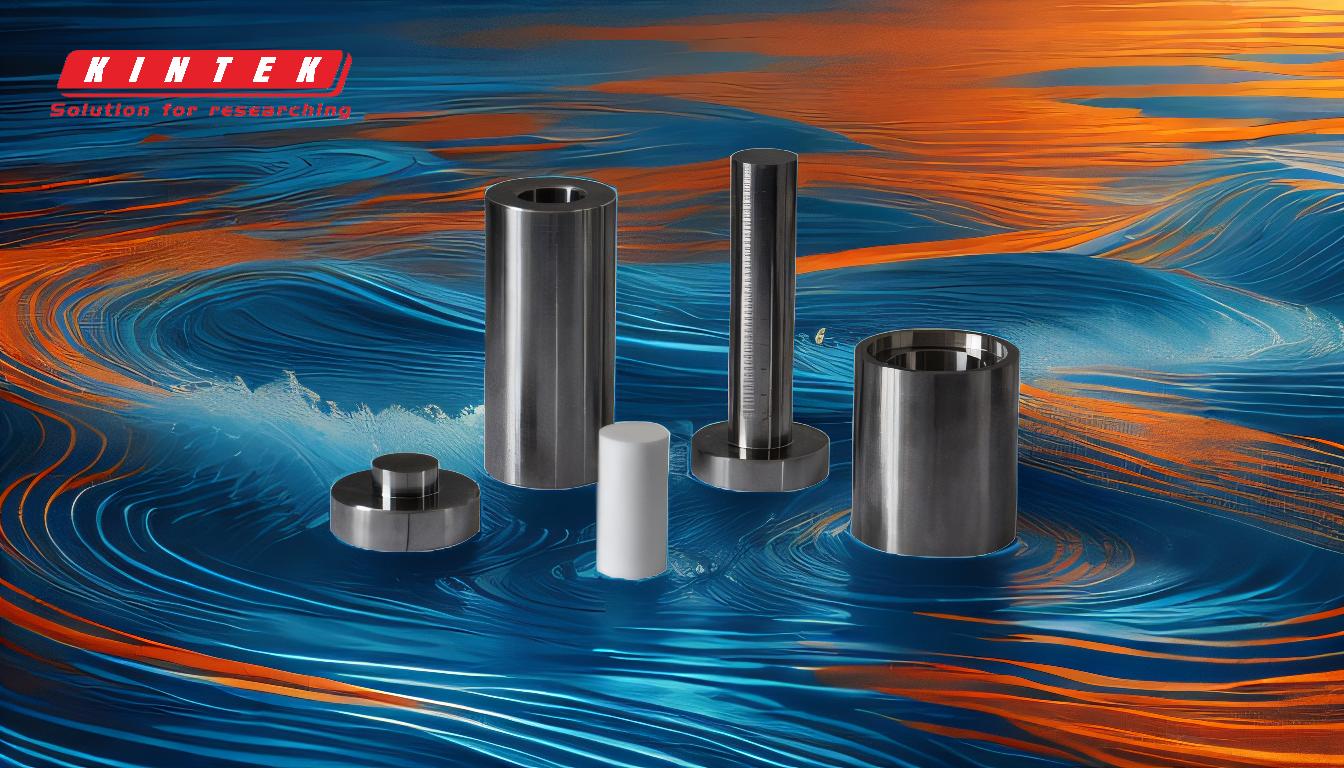
-
Limited Cost-Effectiveness for Large-Scale Production:
- Ceramic mold casting is most cost-effective for small- to medium-sized production runs. For large-scale manufacturing, the costs can become prohibitive due to the non-reusability of the ceramic molds and the additional machining required.
- This limitation makes it less suitable for industries that require high-volume production, where other casting methods might offer better economies of scale.
-
Non-Reusability of Ceramic Molds:
- Unlike some other casting methods, the ceramic molds used in this process are not reusable. Once a casting is completed, the mold is typically destroyed, leading to increased material costs and waste.
- This non-reusability can significantly impact the overall cost and sustainability of the process, especially for larger production volumes.
-
Difficulty in Maintaining Tight Dimensional Tolerances:
- Ceramic mold casting often struggles with maintaining tight dimensional tolerances. This can result in parts that require additional machining to meet precise specifications.
- The difficulty in achieving high precision can be a significant drawback for industries where exact dimensions are critical, such as aerospace or automotive manufacturing.
-
Need for Additional Machining and Polishing:
- Parts produced through ceramic mold casting often require additional machining and polishing to achieve the desired surface finish and dimensional accuracy.
- This additional processing not only increases the overall production time but also adds to the cost, making the process less efficient for certain applications.
-
Time-Intensive Cooling Process:
- The cooling process in ceramic mold casting is time-intensive, which can slow down the overall production timeline.
- This extended cooling period can be a bottleneck in manufacturing processes, particularly when quick turnaround times are essential.
-
Material Limitations:
- While ceramic mold casting is suitable for ferrous and high-temperature non-ferrous materials, it may not be the best choice for all types of metals. Materials like aluminum, copper, magnesium, titanium, and zinc alloys can be cast, but the process may not be optimal for all applications.
- This limitation can restrict the versatility of ceramic mold casting in industries that require a wide range of materials.
In summary, while ceramic mold casting offers several advantages for specific applications, its disadvantages—such as limited scalability, non-reusability of molds, challenges in maintaining tight tolerances, and additional machining requirements—make it less suitable for large-scale production and industries requiring high precision and quick turnaround times.
Summary Table:
Disadvantage | Description |
---|---|
Limited Cost-Effectiveness for Large-Scale | High costs due to non-reusable molds and additional machining; less suitable for high-volume production. |
Non-Reusability of Ceramic Molds | Molds are destroyed after use, increasing costs and waste. |
Difficulty in Tight Dimensional Tolerances | Parts often require additional machining to meet precise specifications. |
Additional Machining and Polishing | Extra processing increases production time and costs. |
Time-Intensive Cooling Process | Extended cooling slows production timelines. |
Material Limitations | Best suited for ferrous and high-temperature non-ferrous materials; less versatile for other metals. |
Need help choosing the right casting method for your project? Contact our experts today!