Iron, while widely used and highly versatile, has several disadvantages that limit its application in certain scenarios. These drawbacks include susceptibility to corrosion, relatively high density, and challenges in recycling and environmental impact. Understanding these limitations is crucial for making informed decisions in material selection, especially in industries where durability, weight, and sustainability are critical factors.
Key Points Explained:
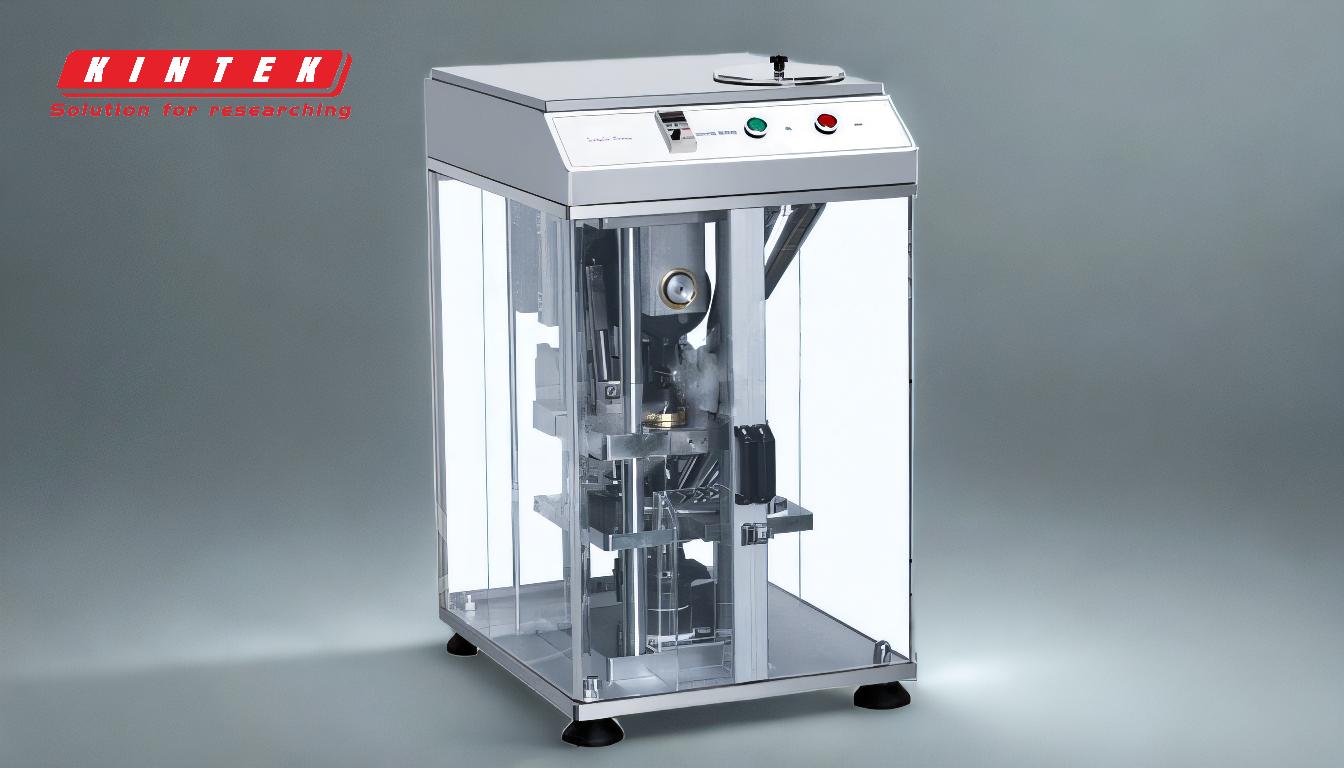
-
Susceptibility to Corrosion:
- Iron is prone to rust when exposed to moisture and oxygen, forming iron oxide. This corrosion weakens the material over time, reducing its structural integrity and lifespan.
- To mitigate this, protective coatings or alloying with other metals (e.g., stainless steel) are often required, which adds to the cost and complexity of using iron.
-
High Density:
- Iron has a relatively high density (7.87 g/cm³), making it heavier compared to materials like aluminum or titanium. This can be a disadvantage in applications where weight reduction is critical, such as in aerospace or automotive industries.
- The weight of iron-based components can also increase transportation and handling costs.
-
Recycling Challenges:
- While iron is recyclable, the process is energy-intensive and can lead to the degradation of material properties over multiple recycling cycles.
- Impurities introduced during recycling can affect the quality of the recycled iron, limiting its use in high-performance applications.
-
Environmental Impact:
- The production of iron, particularly through traditional methods like blast furnaces, generates significant carbon emissions, contributing to environmental pollution and climate change.
- Mining iron ore can also lead to habitat destruction and other ecological disruptions.
-
Magnetic Properties:
- While magnetic properties can be advantageous in some applications, they can also be a disadvantage in others. For instance, iron's magnetism can interfere with electronic devices or create safety hazards in certain environments.
-
Brittleness at Low Temperatures:
- Iron can become brittle at low temperatures, which limits its use in cryogenic applications. This is particularly problematic in industries like aerospace or energy, where materials must perform reliably under extreme conditions.
-
Thermal Conductivity:
- Iron has lower thermal conductivity compared to metals like copper or aluminum. This can be a disadvantage in applications requiring efficient heat dissipation, such as in heat exchangers or electronic components.
-
Cost of Maintenance:
- Due to its susceptibility to corrosion and wear, iron often requires regular maintenance, such as painting or galvanizing, to prolong its lifespan. This increases the overall cost of ownership.
By understanding these disadvantages, engineers and designers can make more informed decisions about when and where to use iron, and when alternative materials might be more suitable.
Summary Table:
Disadvantage | Description |
---|---|
Susceptibility to Corrosion | Iron rusts when exposed to moisture and oxygen, weakening its structure. |
High Density | Iron's density (7.87 g/cm³) makes it heavier, increasing transportation costs. |
Recycling Challenges | Recycling is energy-intensive and can degrade material quality over time. |
Environmental Impact | Iron production generates carbon emissions and disrupts ecosystems. |
Magnetic Properties | Iron's magnetism can interfere with electronics or create safety hazards. |
Brittleness at Low Temperatures | Iron becomes brittle in cryogenic conditions, limiting its use. |
Thermal Conductivity | Iron has lower heat dissipation compared to metals like copper or aluminum. |
Cost of Maintenance | Regular maintenance is required to prevent corrosion, increasing ownership costs. |
Need help choosing the right material for your project? Contact our experts today for tailored advice!