Quenching is a heat treatment process used to rapidly cool metals to achieve desired mechanical properties, such as increased hardness. However, it comes with several disadvantages, particularly when applied to materials like fine ceramics. These disadvantages include the risk of cracking, distortion, and residual stress, as well as challenges in maintaining uniform cooling rates. Additionally, quenching may not be suitable for all materials, especially those with low thermal conductivity or high brittleness, such as fine ceramics.
Key Points Explained:
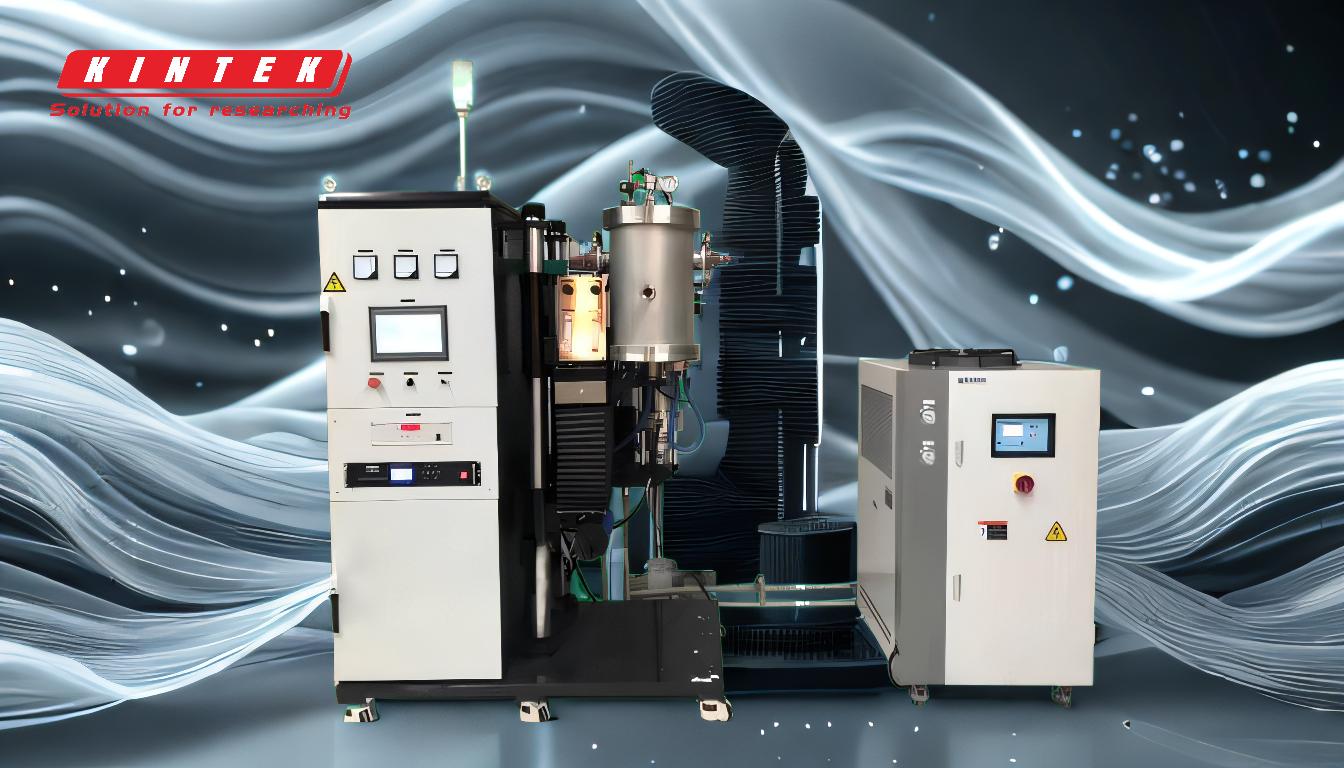
-
Risk of Cracking and Fracture:
- Quenching involves rapid cooling, which can create significant thermal stresses within the material. For brittle materials like fine ceramics, this can lead to cracking or even complete fracture. The sudden temperature change causes uneven contraction, making the material prone to structural failure.
-
Distortion and Warping:
- The rapid cooling process can cause uneven contraction across the material, leading to distortion or warping. This is particularly problematic for precision components where dimensional accuracy is critical. Fine ceramics, which often require high precision, are especially vulnerable to such deformations.
-
Residual Stress:
- Quenching can introduce residual stresses within the material due to uneven cooling rates. These stresses can compromise the material's mechanical properties and lead to premature failure under load. Fine ceramics, being brittle, are less capable of withstanding such internal stresses compared to ductile metals.
-
Unsuitability for Low Thermal Conductivity Materials:
- Materials with low thermal conductivity, such as fine ceramics, struggle to dissipate heat uniformly during quenching. This non-uniform cooling exacerbates the risk of cracking and distortion, making quenching an unsuitable process for such materials.
-
Limited Applicability to Brittle Materials:
- Fine ceramics are inherently brittle, and quenching can exacerbate this brittleness. The process may not improve the material's mechanical properties as effectively as it does for metals, making it less advantageous for ceramic applications.
-
Alternative Processes for Fine Ceramics:
- Given the disadvantages of quenching, alternative heat treatment processes, such as controlled cooling or annealing, are often preferred for fine ceramics. These methods allow for more uniform cooling and reduce the risk of cracking and distortion.
In summary, while quenching is a valuable process for enhancing the properties of metals, it poses significant challenges when applied to materials like fine ceramics. The risks of cracking, distortion, and residual stress, combined with the material's inherent brittleness and low thermal conductivity, make quenching less suitable for such applications. Alternative heat treatment methods are often more effective for fine ceramics.
Summary Table:
Disadvantage | Description |
---|---|
Risk of Cracking and Fracture | Rapid cooling creates thermal stresses, leading to cracks or fractures in brittle materials like fine ceramics. |
Distortion and Warping | Uneven contraction during cooling causes deformation, especially in precision components. |
Residual Stress | Uneven cooling rates introduce internal stresses, compromising mechanical properties. |
Unsuitability for Low Thermal Conductivity Materials | Materials like fine ceramics struggle with uniform heat dissipation, increasing risks. |
Limited Applicability to Brittle Materials | Quenching exacerbates brittleness, making it less effective for ceramics. |
Alternative Processes | Controlled cooling or annealing is preferred for fine ceramics to avoid these issues. |
Looking for a better heat treatment solution for fine ceramics? Contact our experts today to explore alternatives!