The strength of a brazed joint is influenced by a variety of factors, including the materials used, the design of the joint, and the brazing process parameters. A well-designed and properly executed brazing process should result in a joint that is stronger than the parent metal. Key factors include the type of aluminum alloy and brazing brand, the geometry and size of the parts, the quality requirements of the brazing, the composition and concentration of the alkali used for surface oxide removal, and the specific conditions of the brazing process such as temperature, time, vacuum level, heating rate, holding time, and cooling rate. These parameters must be carefully optimized through experimental testing to achieve the best possible joint strength.
Key Points Explained:
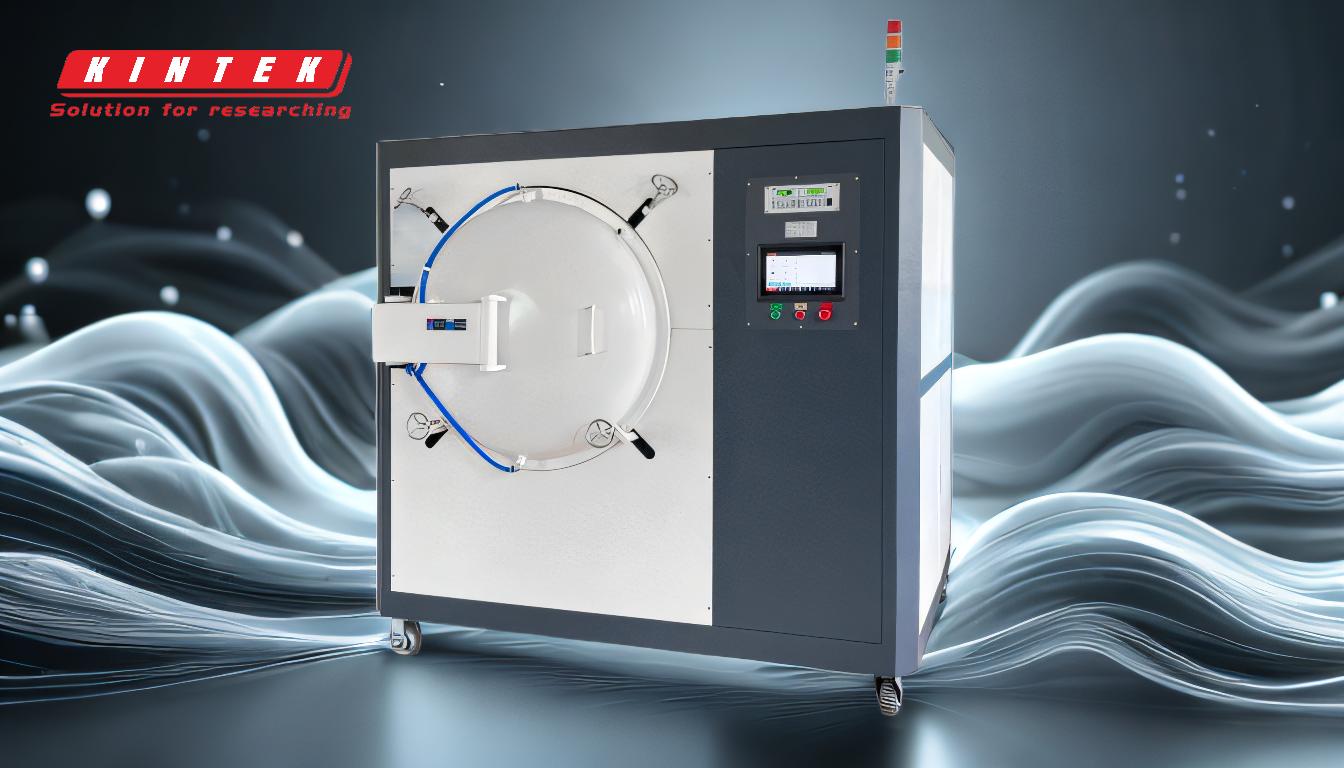
-
Material Selection:
- Aluminum Alloy and Brazing Brand: The type of aluminum alloy and the specific brazing brand used can significantly affect the strength of the brazed joint. Different alloys have varying melting points, thermal conductivities, and mechanical properties, which can influence how well they bond during the brazing process.
- Surface Preparation: The composition and concentration of the alkali used to remove surface oxide films play a crucial role. Proper surface preparation ensures that the brazing filler metal can wet and flow over the surfaces to be joined, leading to a stronger bond.
-
Joint Design and Geometry:
- Shape and Size of Parts: The design of the joint, including its shape and size, affects the distribution of stress and the overall strength of the brazed joint. A well-designed joint will distribute stresses evenly, reducing the likelihood of failure.
- Quality Requirements: The specific quality requirements for the brazed joint, such as the need for high strength or resistance to corrosion, will dictate the choice of materials and brazing parameters.
-
Brazing Process Parameters:
- Corrosion Temperature and Time: The temperature at which the brazing process occurs and the duration of exposure to this temperature are critical. If the temperature is too low or the time too short, the filler metal may not properly wet the surfaces. If the temperature is too high or the time too long, it could lead to excessive grain growth or other metallurgical changes that weaken the joint.
- Vacuum Level in Vacuum Brazing: In vacuum brazing, the level of vacuum is important as it affects the removal of oxides and other contaminants from the joint area. A higher vacuum level generally results in a cleaner joint and stronger bond.
- Heating Rate, Holding Time, and Cooling Rate: The rate at which the joint is heated, the time it is held at the brazing temperature, and the rate at which it is cooled all influence the microstructure of the joint and, consequently, its strength. Rapid cooling, for example, can lead to residual stresses that may weaken the joint.
-
Optimization Through Experimentation:
- Experimental Screening: Given the complexity of the interactions between these factors, it is often necessary to conduct experimental trials to determine the optimal combination of parameters for a specific application. This involves varying one parameter at a time while holding others constant and assessing the impact on joint strength.
By carefully considering and optimizing these factors, it is possible to produce brazed joints that are not only strong but also reliable and durable, meeting the specific requirements of the application.
Summary Table:
Factor | Key Details |
---|---|
Material Selection | - Aluminum alloy type and brazing brand affect joint strength. |
- Surface preparation with alkali ensures proper filler metal flow. | |
Joint Design | - Shape and size of parts influence stress distribution. |
- Quality requirements dictate material and parameter choices. | |
Brazing Process | - Temperature, time, vacuum level, heating rate, and cooling rate are critical. |
Optimization | - Experimental testing is essential to determine optimal parameters. |
Need help optimizing your brazing process for stronger joints? Contact our experts today!