The strength of a brazed joint is determined by a combination of factors, including the materials used, the design of the joint, the brazing process parameters, and the quality of the brazing operation. A well-designed and properly executed brazed joint can achieve strength that exceeds that of the parent metal. Key factors influencing the strength include the type of aluminum alloy and brazing brand, joint geometry, surface preparation, brazing temperature, heating and cooling rates, and the quality of the brazing filler material. Optimizing these factors through experimental screening ensures a strong and reliable joint.
Key Points Explained:
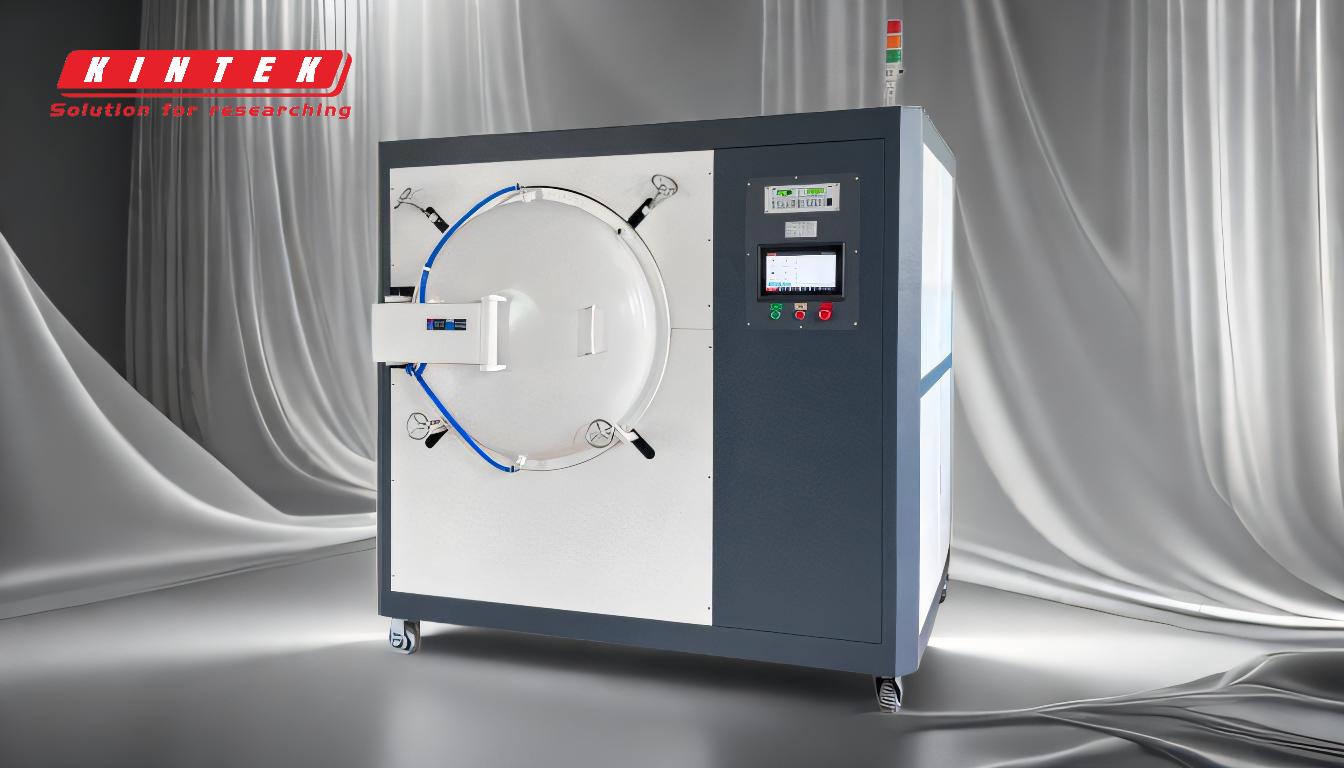
-
Material Selection:
- The type of aluminum alloy and brazing brand significantly impacts the strength of the brazed joint. Different alloys have varying mechanical properties and compatibility with brazing filler materials. Selecting the right combination ensures proper wetting, adhesion, and joint strength.
-
Joint Design:
- The shape and size of the parts being joined play a critical role in joint strength. Proper joint design ensures adequate surface area for bonding and minimizes stress concentrations. Common joint designs include lap joints, butt joints, and T-joints, each with specific advantages depending on the application.
-
Surface Preparation:
- Removing surface oxide films is essential for achieving a strong bond. The composition and concentration of the alkali used for cleaning, as well as the corrosion temperature and time, must be carefully controlled. Proper surface preparation ensures good wetting and adhesion of the brazing filler material.
-
Brazing Process Parameters:
- Heating Rate: A controlled heating rate ensures uniform temperature distribution and prevents thermal stress. Rapid heating can cause uneven melting of the filler material, while slow heating may lead to excessive oxidation.
- Holding Time: The duration at the brazing temperature affects the diffusion of the filler material into the base metal. Insufficient holding time may result in incomplete bonding, while excessive time can lead to excessive intermetallic formation.
- Cooling Rate: Proper cooling ensures the joint solidifies uniformly, minimizing residual stresses. Rapid cooling can cause cracking, while slow cooling may lead to grain growth and reduced strength.
-
Vacuum Level (for Vacuum Brazing):
- In vacuum brazing, the vacuum level must be carefully controlled to prevent oxidation and ensure proper wetting of the filler material. A high vacuum level reduces the presence of contaminants and improves joint quality.
-
Brazing Quality Requirements:
- The specific requirements for the brazed joint, such as strength, corrosion resistance, and appearance, influence the choice of materials and process parameters. Meeting these requirements ensures the joint performs as intended in its application.
-
Experimental Optimization:
- Due to the variability in materials and applications, experimental screening is often necessary to determine the optimal combination of process parameters. This involves testing different combinations of heating rates, holding times, cooling rates, and surface preparation methods to achieve the desired joint strength and quality.
By carefully considering and optimizing these factors, a brazed joint can achieve strength that exceeds that of the parent metal, ensuring reliable performance in various applications.
Summary Table:
Factor | Description |
---|---|
Material Selection | Choose the right aluminum alloy and brazing brand for proper wetting and adhesion. |
Joint Design | Optimize joint geometry (lap, butt, T-joints) to minimize stress concentrations. |
Surface Preparation | Remove oxide films and control cleaning parameters for better adhesion. |
Brazing Process Parameters | Control heating rate, holding time, and cooling rate for uniform bonding. |
Vacuum Level | Maintain high vacuum levels to prevent oxidation in vacuum brazing. |
Brazing Quality Requirements | Meet strength, corrosion resistance, and appearance standards. |
Experimental Optimization | Test and optimize process parameters for maximum joint strength and reliability. |
Need help optimizing your brazed joints? Contact our experts today for tailored solutions!