Heat treatment process failures can lead to significant issues, including compromised metal quality, financial losses, safety hazards, and equipment damage. These failures often stem from improper control of the atmosphere during heat treatment, which can cause chemical reactions on the metal surface, leading to rejected parts, wasted time, and potential risks to employees and customers. Understanding these failures is critical for ensuring the quality and safety of heat-treated components.
Key Points Explained:
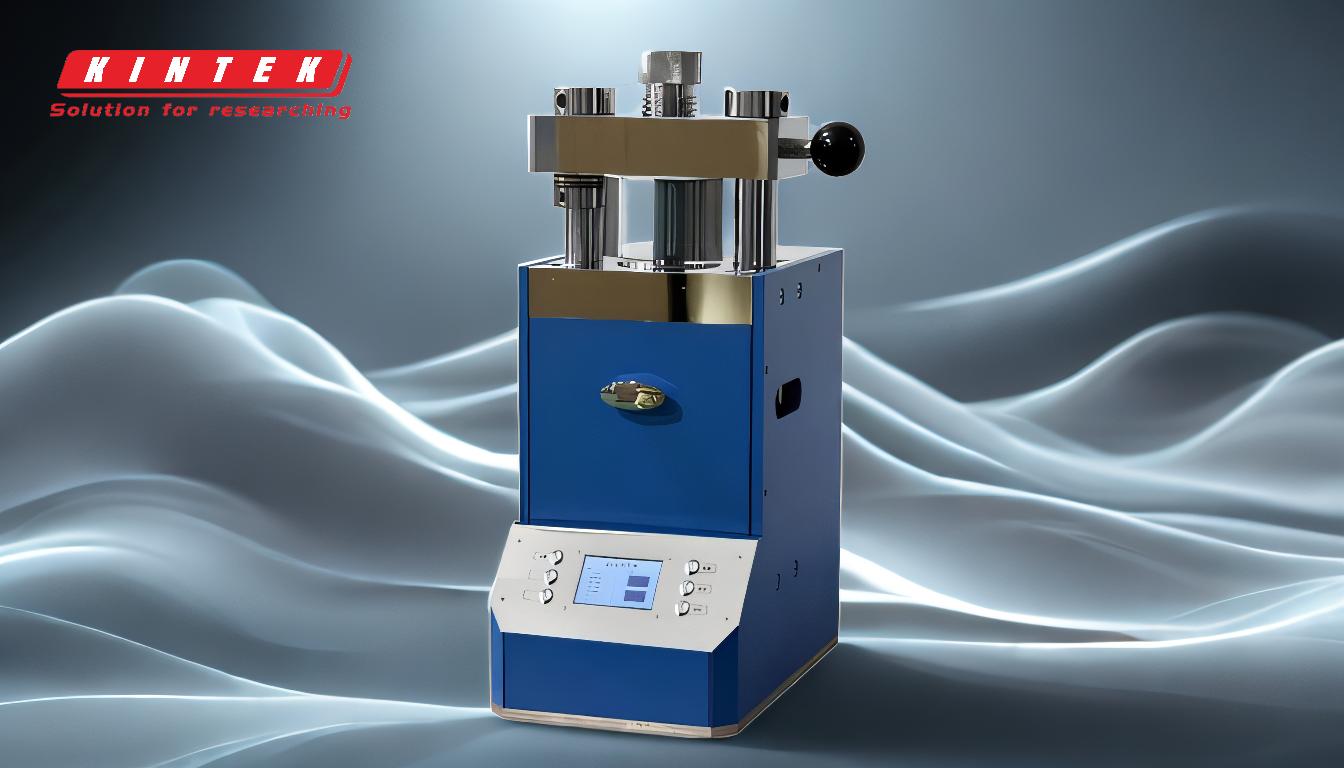
-
Improper Atmosphere Control
- Cause: Lack of a controlled or protective atmosphere during heat treatment.
- Effect: Chemical reactions occur on the metal surface, altering its properties and compromising quality.
-
Consequences:
- Rejected parts due to surface defects or weakened structural integrity.
- Financial losses from wasted materials and rework.
- Potential safety risks if defective parts are used in critical applications.
-
Surface Quality Degradation
- Cause: Exposure to uncontrolled atmospheres (e.g., oxygen, moisture, or contaminants).
- Effect: Oxidation, decarburization, or other surface reactions that degrade the metal's performance.
-
Consequences:
- Reduced hardness, wear resistance, or fatigue strength.
- Increased susceptibility to corrosion or cracking.
-
Furnace Damage
- Cause: Improper atmosphere control can lead to the buildup of harmful byproducts or excessive temperatures.
- Effect: Damage to furnace components, such as heating elements or insulation.
-
Consequences:
- Increased maintenance costs and downtime.
- Reduced furnace lifespan and efficiency.
-
Safety Hazards
- Cause: Uncontrolled atmospheres or improper handling of heat treatment processes.
- Effect: Potential for explosions, fires, or exposure to toxic gases.
-
Consequences:
- Risk of injury or harm to employees.
- Legal and financial liabilities for the organization.
-
Financial and Operational Impacts
- Cause: Rejected parts, furnace damage, and safety incidents.
- Effect: Increased costs and operational inefficiencies.
-
Consequences:
- Wasted time and resources on rework or repairs.
- Loss of customer trust and potential legal repercussions.
-
Preventive Measures
- Solution: Implement strict atmosphere control protocols, including the use of inert gases or vacuum systems.
-
Best Practices:
- Regularly monitor and maintain furnace conditions.
- Train employees on proper heat treatment procedures and safety protocols.
- Conduct quality inspections to detect and address issues early.
By addressing these key points, organizations can minimize heat treatment process failures, ensuring high-quality products, operational efficiency, and a safe working environment.
Summary Table:
Key Issue | Cause | Effect | Consequences |
---|---|---|---|
Improper Atmosphere Control | Lack of controlled or protective atmosphere | Chemical reactions on metal surface | Rejected parts, financial losses, safety risks |
Surface Quality Degradation | Exposure to uncontrolled atmospheres (oxygen, moisture, contaminants) | Oxidation, decarburization, or surface reactions | Reduced hardness, wear resistance, susceptibility to corrosion or cracking |
Furnace Damage | Buildup of harmful byproducts or excessive temperatures | Damage to furnace components (heating elements, insulation) | Increased maintenance costs, downtime, reduced furnace lifespan |
Safety Hazards | Uncontrolled atmospheres or improper handling | Explosions, fires, exposure to toxic gases | Risk of injury, legal and financial liabilities |
Financial & Operational Impacts | Rejected parts, furnace damage, safety incidents | Increased costs and inefficiencies | Wasted time, loss of customer trust, legal repercussions |
Preventive Measures | Implement strict atmosphere control protocols (inert gases, vacuum systems) | Enhanced product quality and operational safety | Regular monitoring, employee training, quality inspections |
Ensure your heat treatment processes are safe and efficient—contact our experts today for tailored solutions!