Heat treatment is a critical process in manufacturing that involves heating and cooling metals under controlled conditions to enhance their physical and chemical properties. The primary purposes of heat treatment include improving mechanical properties such as hardness, strength, ductility, and toughness, as well as enhancing surface characteristics like abrasion resistance and corrosion resistance. This process is widely used in industries such as automotive, aerospace, and general manufacturing to ensure that metal components meet specific performance and durability requirements. By carefully controlling the heating and cooling cycles, heat treatment can tailor the microstructure of metals to achieve desired outcomes, making it an indispensable technique in modern manufacturing.
Key Points Explained:
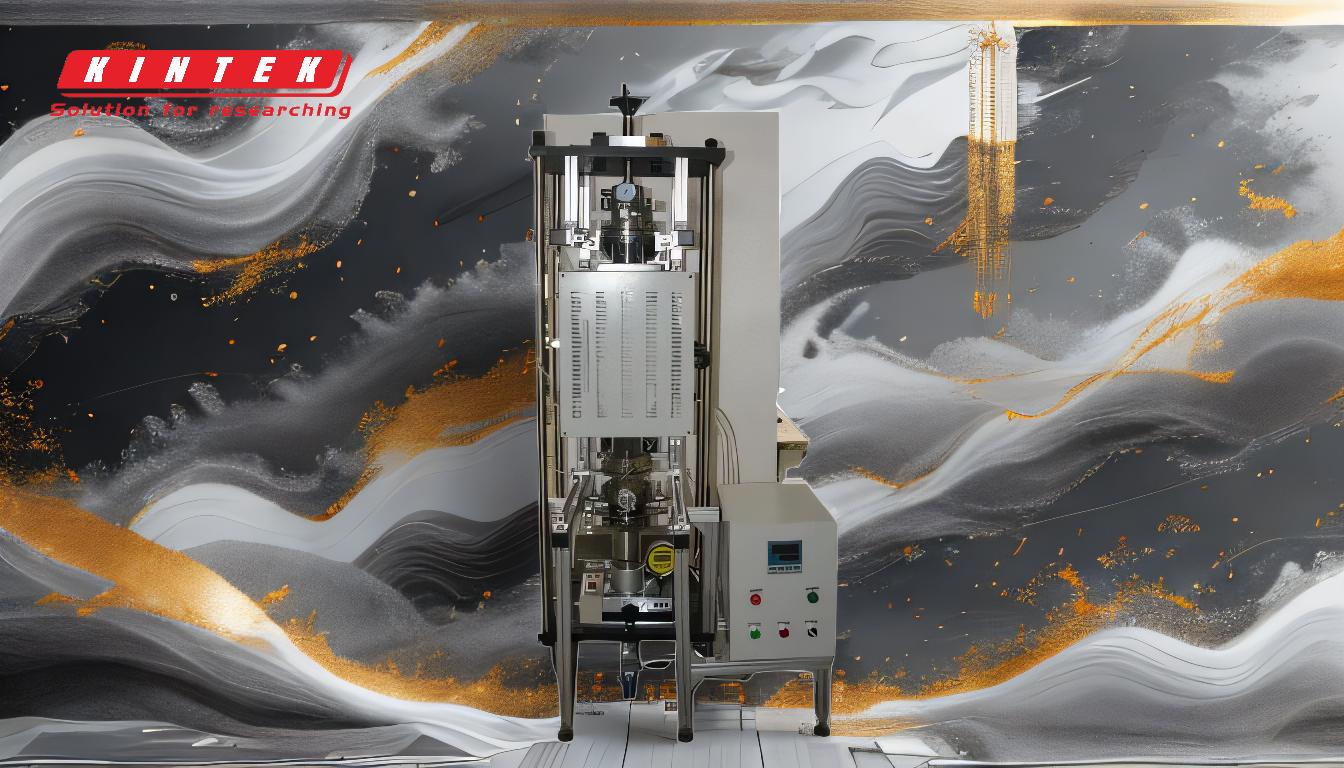
-
Improving Mechanical Properties:
- Hardness: Heat treatment can increase the hardness of metals, making them more resistant to wear and deformation. This is particularly important for components that are subject to high stress or friction, such as gears and bearings.
- Strength: By altering the internal structure of the metal, heat treatment can enhance its tensile and yield strength, allowing it to withstand greater loads without failing.
- Ductility: Heat treatment can also improve the ductility of metals, enabling them to be shaped or formed without breaking. This is crucial for manufacturing processes that involve bending, stretching, or drawing.
- Toughness: The process can increase the toughness of metals, which is the ability to absorb energy and deform plastically without fracturing. This is vital for components that are subject to impact or shock loading.
-
Enhancing Surface Characteristics:
- Abrasion Resistance: Heat treatment can create a hard surface layer on softer metals, improving their resistance to abrasion and extending their lifespan in applications where they are exposed to friction or wear.
- Corrosion Resistance: Certain heat treatment processes can form a protective layer on the surface of metals, enhancing their resistance to corrosion and making them suitable for use in harsh environments.
-
Tailoring Microstructure for Specific Applications:
- Controlled Heating and Cooling: The precise control of heating and cooling cycles during heat treatment allows for the modification of the metal's microstructure. This can lead to the formation of specific phases or grain structures that are optimal for the intended application.
- Phase Transformations: Heat treatment can induce phase transformations in metals, such as the conversion of austenite to martensite in steel, which significantly enhances hardness and strength.
-
Cost-Effectiveness and Versatility:
- Balancing Cost and Quality: Heat treatment offers a cost-effective way to enhance the properties of metals without the need for expensive alloying elements. This makes it an attractive option for industries looking to balance performance with cost.
- Wide Range of Applications: The versatility of heat treatment processes means they can be applied to a broad spectrum of metals and alloys, making them suitable for a wide range of industrial applications, from automotive components to aerospace parts.
-
Improving Durability and Longevity:
- Enhanced Durability: By improving the mechanical and surface properties of metals, heat treatment significantly enhances their durability, ensuring they can withstand the rigors of their intended use over a longer period.
- Longevity: The process extends the lifespan of metal components, reducing the need for frequent replacements and maintenance, which can lead to cost savings and increased reliability in industrial operations.
In summary, heat treatment is a versatile and essential process in manufacturing that improves the mechanical and surface properties of metals, enhances their durability and longevity, and allows for the customization of metal components to meet specific industrial requirements. By carefully controlling the heating and cooling cycles, manufacturers can achieve a balance between cost and quality, making heat treatment a cornerstone of modern metalworking.
Summary Table:
Key Benefits of Heat Treatment | Description |
---|---|
Improved Mechanical Properties | Enhances hardness, strength, ductility, and toughness for better performance. |
Enhanced Surface Characteristics | Increases abrasion and corrosion resistance for longer-lasting components. |
Tailored Microstructure | Customizes metal properties for specific applications through controlled heating and cooling. |
Cost-Effectiveness | Balances performance and cost without expensive alloying elements. |
Durability & Longevity | Extends the lifespan of metal components, reducing maintenance and replacement costs. |
Optimize your metal components with heat treatment—contact our experts today to learn more!