Thin film deposition is a critical process in materials science and engineering, enabling the creation of thin layers of material on substrates for applications in electronics, optics, and coatings. The primary methods of thin film deposition can be broadly categorized into Physical Vapor Deposition (PVD) and Chemical Vapor Deposition (CVD), with additional advanced techniques like Atomic Layer Deposition (ALD) and Spray Pyrolysis. Each method has unique mechanisms, advantages, and applications, making them suitable for specific material and performance requirements. Below, we explore these methods in detail, focusing on their processes, key characteristics, and applications.
Key Points Explained:
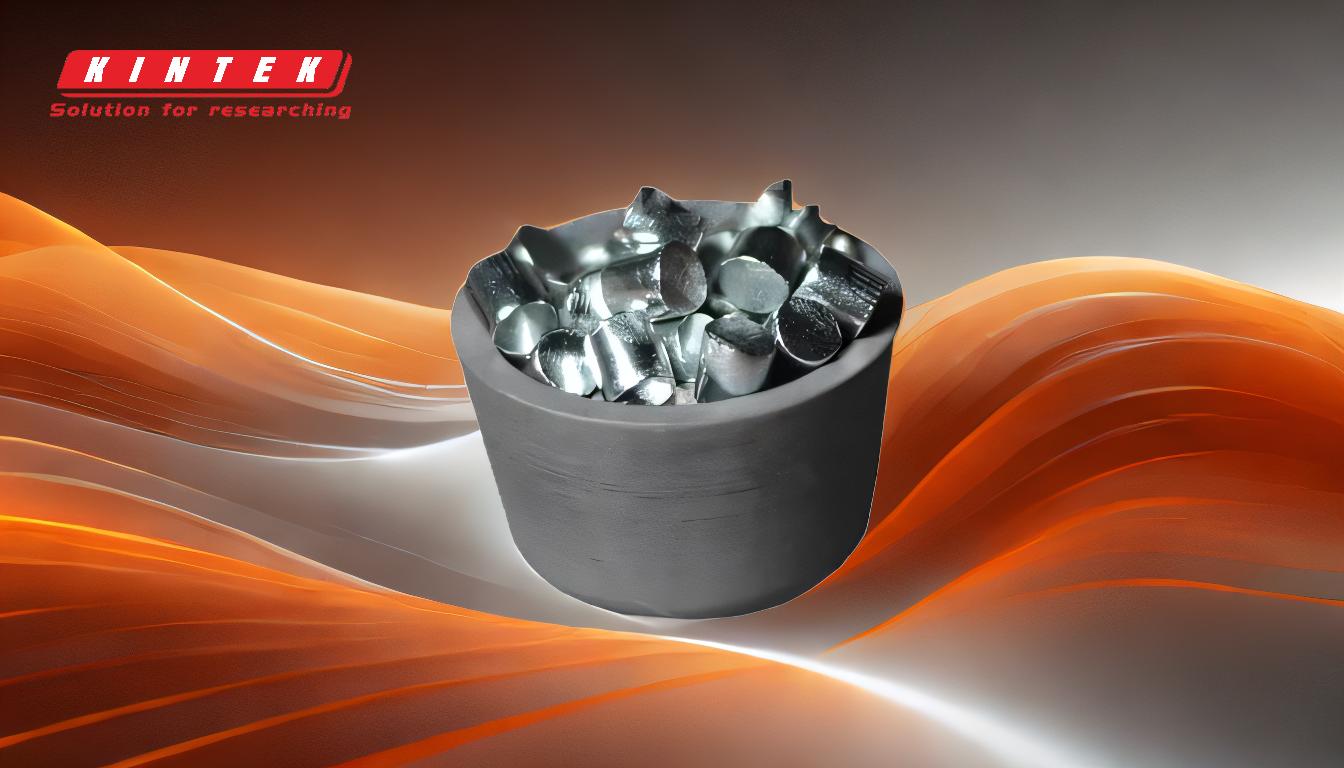
-
Physical Vapor Deposition (PVD)
- Definition: PVD involves the physical transfer of material from a source (target) to a substrate in a vacuum environment. The material is vaporized or sputtered and then condenses on the substrate to form a thin film.
-
Key Techniques:
- Thermal Evaporation: The target material is heated to its vaporization point, and the vapor condenses on the substrate. This method is simple and cost-effective but limited to materials with low melting points.
- Sputtering: High-energy ions bombard the target material, ejecting atoms that deposit on the substrate. Sputtering is versatile and can deposit a wide range of materials, including metals, alloys, and ceramics.
- Ion Beam Deposition: A focused ion beam is used to sputter the target material, offering precise control over film thickness and composition.
- Applications: PVD is widely used in semiconductor manufacturing, optical coatings, and wear-resistant coatings.
-
Chemical Vapor Deposition (CVD)
- Definition: CVD involves chemical reactions in the gas phase to produce a thin film on the substrate. The process typically requires high temperatures and controlled gas environments.
-
Key Techniques:
- Thermal CVD: The substrate is heated, and precursor gases react to form a solid film. This method is used for depositing silicon dioxide, silicon nitride, and other dielectric materials.
- Plasma-Enhanced CVD (PECVD): Plasma is used to lower the reaction temperature, making it suitable for temperature-sensitive substrates.
- Atomic Layer Deposition (ALD): A subset of CVD, ALD deposits films one atomic layer at a time, offering exceptional control over thickness and uniformity. It is ideal for nanoscale applications.
- Applications: CVD is essential in microelectronics, solar cells, and protective coatings.
-
Atomic Layer Deposition (ALD)
- Definition: ALD is a precision technique that deposits thin films one atomic layer at a time through sequential, self-limiting chemical reactions.
-
Key Characteristics:
- Extremely uniform and conformal coatings, even on complex geometries.
- Precise control over film thickness at the atomic level.
- Slow deposition rate compared to other methods.
- Applications: ALD is used in advanced semiconductor devices, MEMS, and nanotechnology.
-
Spray Pyrolysis
- Definition: This method involves spraying a solution containing the desired material onto a heated substrate, where the solvent evaporates, and the material decomposes to form a thin film.
-
Key Characteristics:
- Simple and cost-effective, suitable for large-area coatings.
- Limited to materials that can be dissolved in a suitable solvent.
- Applications: Spray pyrolysis is used in solar cells, transparent conductive coatings, and sensors.
-
Other Deposition Techniques
- Electroplating: A solution-based method where an electric current is used to deposit a metal film on a conductive substrate. Commonly used for decorative and protective coatings.
- Molecular Beam Epitaxy (MBE): A high-vacuum technique that deposits single-crystal films with atomic precision, primarily used in research and high-performance semiconductor devices.
- Chemical Bath Deposition: A low-cost method for depositing thin films from a chemical solution, often used for metal chalcogenides in solar cells.
-
Factors Influencing Thin Film Deposition
- Substrate Properties: Surface roughness, temperature, and chemical compatibility affect film adhesion and quality.
- Deposition Parameters: Pressure, temperature, and deposition rate influence film morphology and properties.
- Material Properties: The melting point, vapor pressure, and reactivity of the target material determine the choice of deposition method.
-
Applications of Thin Film Deposition
- Electronics: Thin films are used in transistors, capacitors, and interconnects in integrated circuits.
- Optics: Anti-reflective coatings, mirrors, and filters rely on thin film deposition.
- Energy: Thin films are critical in solar panels, batteries, and fuel cells.
- Coatings: Protective and decorative coatings in automotive, aerospace, and consumer goods industries.
In summary, thin film deposition methods are diverse and tailored to specific material and application requirements. PVD and CVD are the most widely used techniques, offering versatility and scalability, while ALD and spray pyrolysis provide specialized solutions for advanced applications. Understanding the strengths and limitations of each method is essential for selecting the appropriate technique for a given project.
Summary Table:
Method | Key Characteristics | Applications |
---|---|---|
Physical Vapor Deposition (PVD) | - Physical transfer in a vacuum environment - Techniques: Thermal Evaporation, Sputtering, Ion Beam Deposition |
Semiconductor manufacturing, optical coatings, wear-resistant coatings |
Chemical Vapor Deposition (CVD) | - Chemical reactions in gas phase - Techniques: Thermal CVD, PECVD, ALD |
Microelectronics, solar cells, protective coatings |
Atomic Layer Deposition (ALD) | - Deposits one atomic layer at a time - Precise control, uniform coatings |
Advanced semiconductor devices, MEMS, nanotechnology |
Spray Pyrolysis | - Spray solution onto heated substrate - Simple, cost-effective, large-area coatings |
Solar cells, transparent conductive coatings, sensors |
Need help selecting the right thin film deposition method for your project? Contact our experts today!