Sintering is a critical process in materials science and manufacturing, where powdered materials are transformed into dense, solid bodies through the application of heat and pressure, typically below the material's melting point. The key parameters influencing the sintering process include temperature, dwell time, pressure, particle size, composition, and the gaseous atmosphere. These parameters are carefully controlled to achieve the desired properties of the final product, such as density, strength, and durability. The choice of sintering conditions depends on the type of material being processed and the specific requirements of the end product. Understanding and optimizing these parameters is essential for producing high-quality sintered materials used in various industries, including metallurgy, ceramics, and plastics.
Key Points Explained:
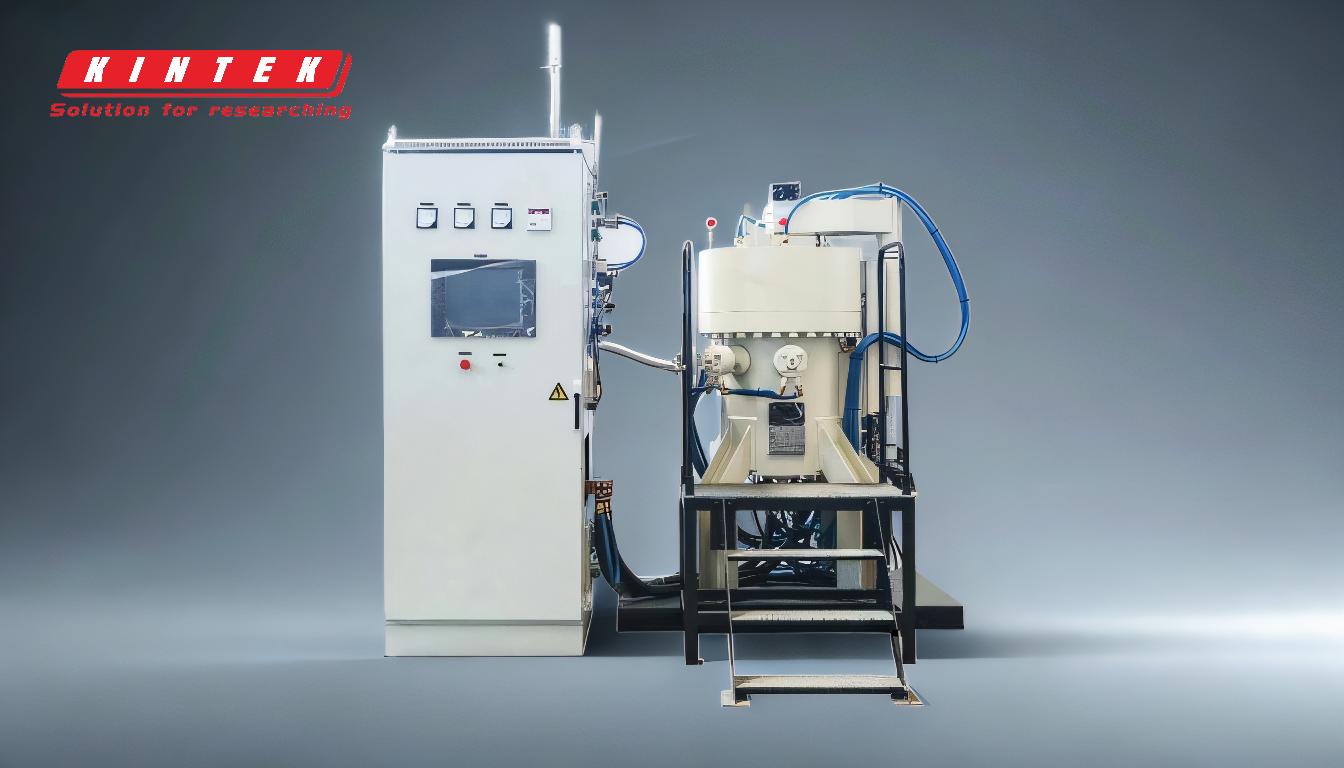
-
Temperature:
- Role: Temperature is one of the most critical parameters in sintering. It determines the kinetics of the sintering process and directly influences the material's properties, such as density and strength.
- Impact: Higher temperatures generally increase the rate of particle bonding and densification. However, the temperature must be carefully controlled to avoid melting the material, which could lead to deformation or loss of desired properties.
- Optimization: The optimal sintering temperature varies depending on the material. For example, metals with high melting points, like tungsten, require higher sintering temperatures compared to ceramics or plastics.
-
Dwell Time:
- Role: Dwell time refers to the duration for which the material is held at the sintering temperature.
- Impact: Longer dwell times allow for more complete diffusion of atoms across particle boundaries, leading to better bonding and densification. However, excessively long dwell times can lead to grain growth, which may degrade the material's mechanical properties.
- Optimization: The dwell time must be balanced to achieve sufficient densification without causing excessive grain growth. This balance is often determined through experimental trials.
-
Pressure:
- Role: Pressure is applied during sintering to enhance particle rearrangement and eliminate porosity.
- Impact: Higher pressures can improve the density and strength of the sintered product by forcing particles into closer contact and promoting bonding. However, too much pressure can cause deformation or cracking.
- Optimization: The applied pressure must be carefully controlled to achieve the desired density without compromising the integrity of the material.
-
Particle Size:
- Role: The size of the particles being sintered significantly affects the sintering behavior.
- Impact: Smaller particles have a higher surface area-to-volume ratio, which promotes faster diffusion and better densification. However, very fine particles can lead to issues like agglomeration, which may hinder uniform sintering.
- Optimization: The particle size distribution should be optimized to ensure uniform sintering and achieve the desired material properties.
-
Composition:
- Role: The composition of the powder, including any additives or reinforcements, influences the sintering process.
- Impact: Homogeneous compositions generally promote better densification and more uniform properties. Additives can be used to enhance certain properties, such as strength or thermal conductivity, but they must be compatible with the base material.
- Optimization: The composition should be carefully selected to achieve the desired properties while minimizing any negative effects on the sintering process.
-
Gaseous Atmosphere:
- Role: The atmosphere in which sintering takes place can affect the process and the final properties of the material.
- Impact: An inert or reducing atmosphere can prevent oxidation and other undesirable reactions. In some cases, a specific gas may be used to enhance certain properties, such as hardness or wear resistance.
- Optimization: The choice of atmosphere depends on the material being sintered and the desired properties of the final product. Common atmospheres include nitrogen, argon, and hydrogen.
-
Heating Rate:
- Role: The rate at which the material is heated to the sintering temperature can influence the densification process.
- Impact: A controlled heating rate ensures uniform temperature distribution and minimizes thermal stresses, which can lead to cracking or warping. Rapid heating can cause uneven sintering, while too slow heating can prolong the process unnecessarily.
- Optimization: The heating rate should be optimized based on the material's thermal properties and the desired outcome.
In summary, the sintering process is governed by a complex interplay of parameters, each of which must be carefully controlled to achieve the desired properties in the final product. Understanding and optimizing these parameters is essential for producing high-quality sintered materials used in various applications.
Summary Table:
Parameter | Role | Impact | Optimization |
---|---|---|---|
Temperature | Determines kinetics and influences properties like density and strength | Higher temperatures increase bonding but must avoid melting | Varies by material; higher for metals like tungsten |
Dwell Time | Duration held at sintering temperature | Longer times improve bonding but may cause grain growth | Balance densification with minimal grain growth |
Pressure | Enhances particle rearrangement and reduces porosity | Higher pressure improves density but can cause deformation | Control pressure to achieve density without compromising integrity |
Particle Size | Affects sintering behavior | Smaller particles promote faster diffusion but can lead to agglomeration | Optimize size distribution for uniform sintering |
Composition | Influences sintering process and final properties | Homogeneous compositions promote better densification | Select composition to achieve desired properties while minimizing negative effects |
Gaseous Atmosphere | Affects process and final properties | Inert or reducing atmospheres prevent oxidation | Choose atmosphere (e.g., nitrogen, argon, hydrogen) based on material and goals |
Heating Rate | Influences densification process | Controlled rates minimize thermal stresses; rapid heating causes unevenness | Optimize based on material's thermal properties |
Optimize your sintering process for superior material performance—contact our experts today!