Carburizing is a heat treatment process that enhances the surface hardness of low-carbon steel by introducing additional carbon atoms into its surface and sub-surface layers. This process improves wear resistance, fatigue strength, and overall mechanical properties while maintaining a soft and ductile core. However, it also has limitations, such as potential distortion, high energy consumption, and the need for precise process control. Below, we explore the pros and cons of carburizing in detail, considering its applications, process variations, and operational challenges.
Key Points Explained:
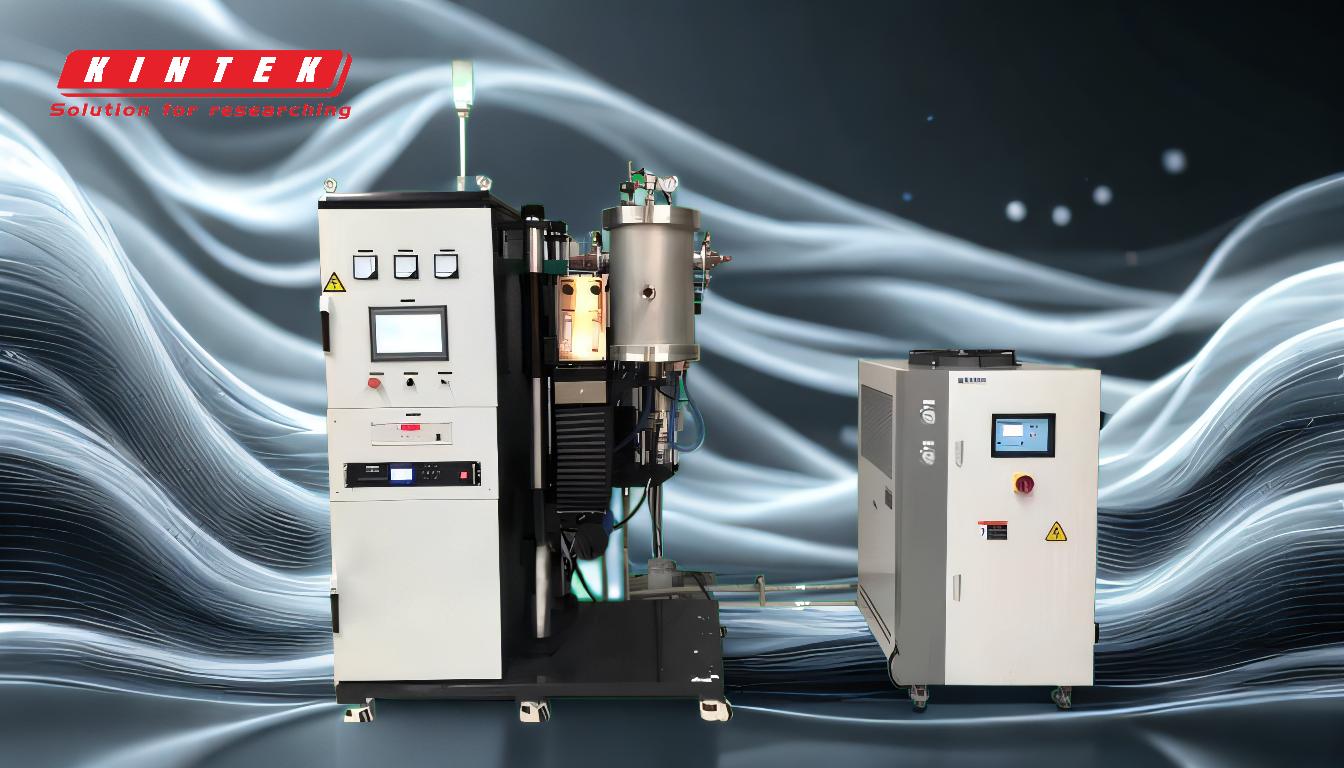
-
Advantages of Carburizing
-
Increased Surface Hardness:
Carburizing significantly enhances the surface hardness of low-carbon steel, making it suitable for applications requiring high wear resistance. The process diffuses carbon into the steel's surface, creating a hardened layer while maintaining a softer, more ductile core. -
Improved Wear Resistance:
The hardened surface layer resists abrasion and wear, extending the lifespan of components subjected to friction and mechanical stress. -
Enhanced Fatigue Strength:
Carburizing improves the fatigue strength of steel parts, allowing them to withstand cyclic loading and stress without failure. -
Versatility in Application:
The process can be applied to entire parts or specific areas by masking non-hardened regions with carbon-stopping paint. This flexibility makes it suitable for complex geometries and selective hardening. -
Cost-Effective for High-Volume Production:
Atmosphere carburizing, in particular, offers a low initial capital investment and high-volume output capability, making it economical for large-scale manufacturing. -
Automation and Process Control:
Modern carburizing methods, such as vacuum carburizing, allow for full automation, precise process control, and flexible cycle adjustments, improving efficiency and consistency.
-
Increased Surface Hardness:
-
Disadvantages of Carburizing
-
Potential for Distortion:
The high temperatures involved in carburizing can cause dimensional changes and distortion in the treated parts, requiring additional finishing processes. -
Energy Consumption:
Carburizing is energy-intensive, especially in atmosphere carburizing, where furnaces operate continuously at high temperatures. -
Process Complexity:
Achieving consistent results requires precise control of temperature, carbon concentration, and diffusion time. Any deviation can lead to uneven hardening or insufficient carbon penetration. -
Limited to Low-Carbon Steels:
Carburizing is primarily effective for low-carbon steels. High-carbon steels or alloys may not benefit as significantly from the process. -
Environmental Concerns:
Atmosphere carburizing involves the use of carbon-rich gases, which can pose environmental and safety risks if not properly managed. -
Cost of Advanced Methods:
While vacuum carburizing offers superior control and flexibility, it involves higher equipment and operational costs compared to traditional methods.
-
Potential for Distortion:
-
Comparison of Carburizing Methods
-
Atmosphere Carburizing:
- Pros: Low initial investment, high-volume capability, and well-established process knowledge.
- Cons: Higher energy consumption, potential for environmental hazards, and less precise control compared to vacuum carburizing.
-
Vacuum Carburizing:
- Pros: Precise process control, energy efficiency (consumption only when needed), and compatibility with higher temperatures and flexible cycles.
- Cons: Higher equipment costs and complexity, making it less suitable for small-scale operations.
-
Atmosphere Carburizing:
-
Applications of Carburizing
-
Automotive Industry:
Used for gears, shafts, and other components requiring high wear resistance and fatigue strength. -
Aerospace Industry:
Critical for parts subjected to extreme mechanical stress and abrasion. -
Tool Manufacturing:
Enhances the durability of cutting tools and dies. -
Industrial Machinery:
Improves the performance of components like bearings, rollers, and camshafts.
-
Automotive Industry:
-
Considerations for Equipment and Consumable Purchasers
-
Process Requirements:
Evaluate whether atmosphere or vacuum carburizing aligns better with production volume, part complexity, and budget constraints. -
Energy Efficiency:
Consider the long-term energy costs and environmental impact of the chosen method. -
Automation Needs:
For high-volume production, prioritize systems with full automation capabilities to ensure consistency and reduce labor costs. -
Maintenance and Troubleshooting:
Choose equipment with reliable control devices and established troubleshooting support to minimize downtime. -
Material Compatibility:
Ensure the carburizing process is suitable for the specific steel grades used in your applications.
-
Process Requirements:
In summary, carburizing is a highly effective method for enhancing the surface properties of low-carbon steel, offering significant benefits in terms of hardness, wear resistance, and fatigue strength. However, it also presents challenges such as potential distortion, high energy consumption, and process complexity. By carefully selecting the appropriate carburizing method and equipment, manufacturers can optimize the process to meet their specific needs while minimizing drawbacks.
Summary Table:
Aspect | Advantages | Disadvantages |
---|---|---|
Surface Hardness | Enhances surface hardness for wear resistance | Potential distortion due to high temperatures |
Wear Resistance | Extends component lifespan under friction and stress | High energy consumption, especially in atmosphere carburizing |
Fatigue Strength | Improves resistance to cyclic loading and stress | Requires precise control of temperature, carbon concentration, and diffusion time |
Versatility | Suitable for complex geometries and selective hardening | Limited to low-carbon steels |
Cost-Effectiveness | Economical for high-volume production with low initial investment | Environmental concerns with carbon-rich gases |
Process Control | Automation and precise control in modern methods like vacuum carburizing | Higher equipment costs for advanced methods |
Optimize your carburizing process for superior results—contact our experts today!