Refractories are essential materials used in high-temperature environments, such as furnaces, kilns, and reactors, to withstand extreme conditions while maintaining structural integrity and functionality. The requisites of refractories include the ability to endure high temperatures, resist thermal shock, handle mechanical loads, and withstand chemical and abrasive actions. Additionally, refractories must possess properties like low thermal conductivity, corrosion resistance, ease of installation, and maintenance. These characteristics ensure the longevity and efficiency of refractory linings in industrial applications.
Key Points Explained:
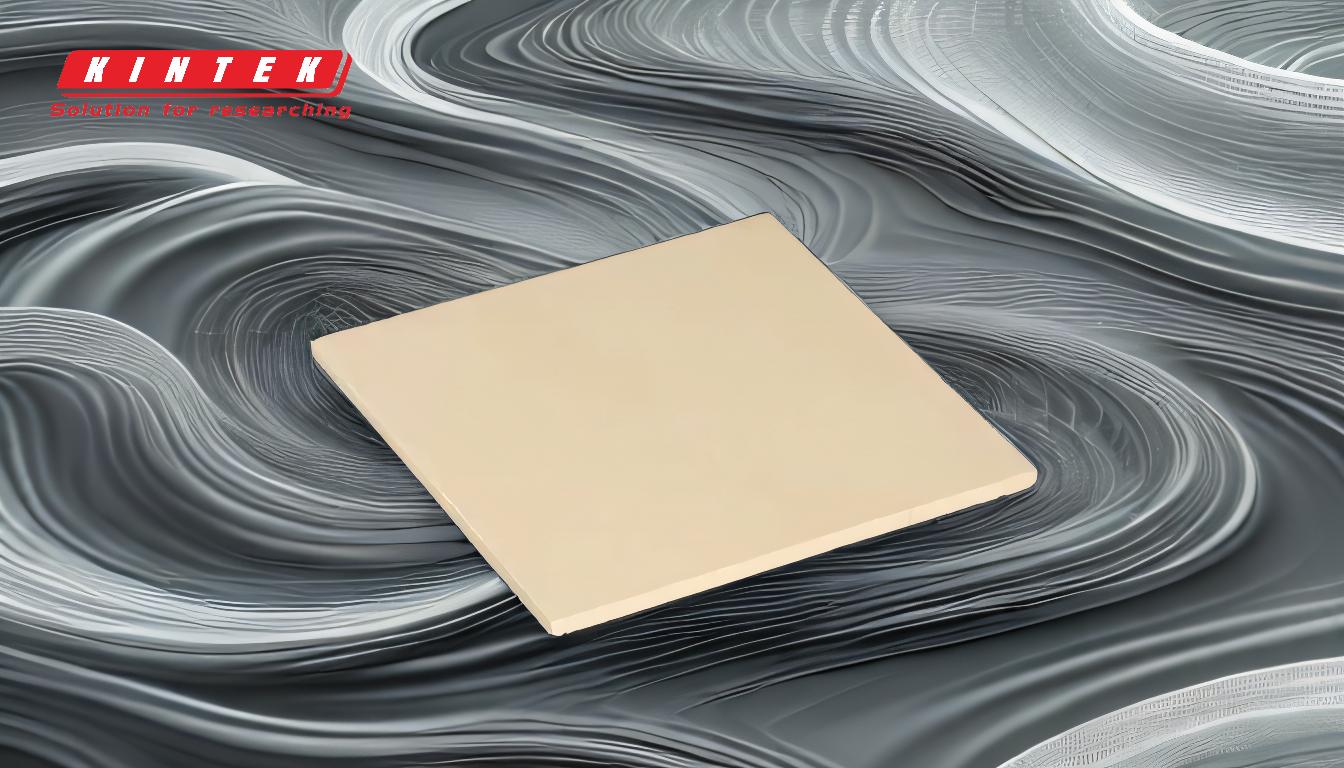
-
Ability to Withstand High Temperatures
- Refractories must endure extreme heat without melting, degrading, or losing structural integrity.
- This property ensures that heat is effectively contained within a confined area, such as a furnace, to optimize energy efficiency.
- High-temperature resistance is critical for applications like steelmaking, glass production, and cement manufacturing.
-
Resistance to Thermal Shock
- Refractories must handle sudden temperature changes without cracking or breaking.
- Thermal shock resistance is vital in processes where rapid heating or cooling occurs, such as in batch furnaces or during startup and shutdown cycles.
- Materials with low thermal expansion coefficients and high thermal conductivity are preferred for such applications.
-
Load-Bearing Capacity
- Refractories must support mechanical loads at high temperatures without deformation or failure.
- This includes withstanding the weight of the structure, pressure from molten materials, and mechanical stresses during operation.
- High compressive strength and structural stability are essential for load-bearing applications.
-
Chemical and Abrasive Resistance
- Refractories must resist chemical reactions with molten metals, slags, and gases, which can cause corrosion and degradation.
- They must also withstand abrasive actions from solid particles or flowing materials, such as in cement kilns or blast furnaces.
- Materials with high chemical inertness and hardness are selected for these environments.
-
Low Thermal Conductivity
- Refractories should have low thermal conductivity to minimize heat loss and improve energy efficiency.
- This property ensures that heat is retained within the system, reducing energy consumption and operational costs.
- Insulating refractories are often used in conjunction with dense refractories to achieve this balance.
-
Ease of Installation and Maintenance
- Refractories must be easy to install, repair, and replace to minimize downtime and labor costs.
- Prefabricated shapes, modular designs, and materials with good workability are preferred for ease of installation.
- Maintenance-friendly refractories reduce operational disruptions and extend the lifespan of the lining.
-
Corrosion Resistance
- Refractories must resist corrosion from acidic or basic environments, depending on the application.
- For example, acidic refractories are used in environments with acidic slags, while basic refractories are suitable for basic slags.
- Proper material selection ensures compatibility with the specific chemical environment.
-
Thermal Insulation and Energy Efficiency
- Refractories play a crucial role in thermal insulation, reducing heat loss and improving energy efficiency.
- Insulating refractories, such as ceramic fiber or lightweight bricks, are often used in conjunction with dense refractories to optimize thermal performance.
- This balance ensures both structural integrity and energy savings.
-
Durability and Longevity
- Refractories must have a long service life to minimize replacement frequency and associated costs.
- Durability depends on factors like material composition, operating conditions, and maintenance practices.
- High-quality refractories with superior properties ensure extended operational life and reduced downtime.
-
Cost-Effectiveness
- While refractories must meet stringent performance requirements, they should also be cost-effective.
- Balancing performance with cost ensures that the refractory solution is economically viable without compromising quality.
- Lifecycle cost analysis is often used to evaluate the overall cost-effectiveness of refractory materials.
In summary, the requisites of refractories encompass a combination of thermal, mechanical, chemical, and practical properties. These materials must be carefully selected and designed to meet the specific demands of high-temperature industrial processes, ensuring efficiency, durability, and cost-effectiveness.
Summary Table:
Property | Description |
---|---|
High-Temperature Resistance | Endures extreme heat without melting or degrading, critical for steelmaking and glass production. |
Thermal Shock Resistance | Handles sudden temperature changes without cracking, vital for batch furnaces. |
Load-Bearing Capacity | Supports mechanical loads at high temperatures, ensuring structural stability. |
Chemical Resistance | Resists corrosion from molten metals, slags, and gases. |
Low Thermal Conductivity | Minimizes heat loss, improving energy efficiency. |
Ease of Installation | Prefabricated shapes and modular designs reduce downtime and labor costs. |
Corrosion Resistance | Resists acidic or basic environments, ensuring compatibility with specific applications. |
Durability | Long service life reduces replacement frequency and operational costs. |
Cost-Effectiveness | Balances performance and cost for economically viable solutions. |
Need help selecting the right refractories for your high-temperature applications? Contact our experts today!