The PVD (Physical Vapor Deposition) coating process is a sophisticated method used to apply thin, durable, and highly adherent coatings to various substrates. The process generally involves several critical steps, including preparation of the substrate, creation of a high-vacuum environment, vaporization of the target material, transportation of vaporized atoms, reaction with gases if necessary, and deposition onto the substrate. These steps ensure the formation of a uniform, high-quality coating that enhances the substrate's properties, such as wear resistance, corrosion resistance, and aesthetic appeal. Below, the key steps and their significance are explained in detail.
Key Points Explained:
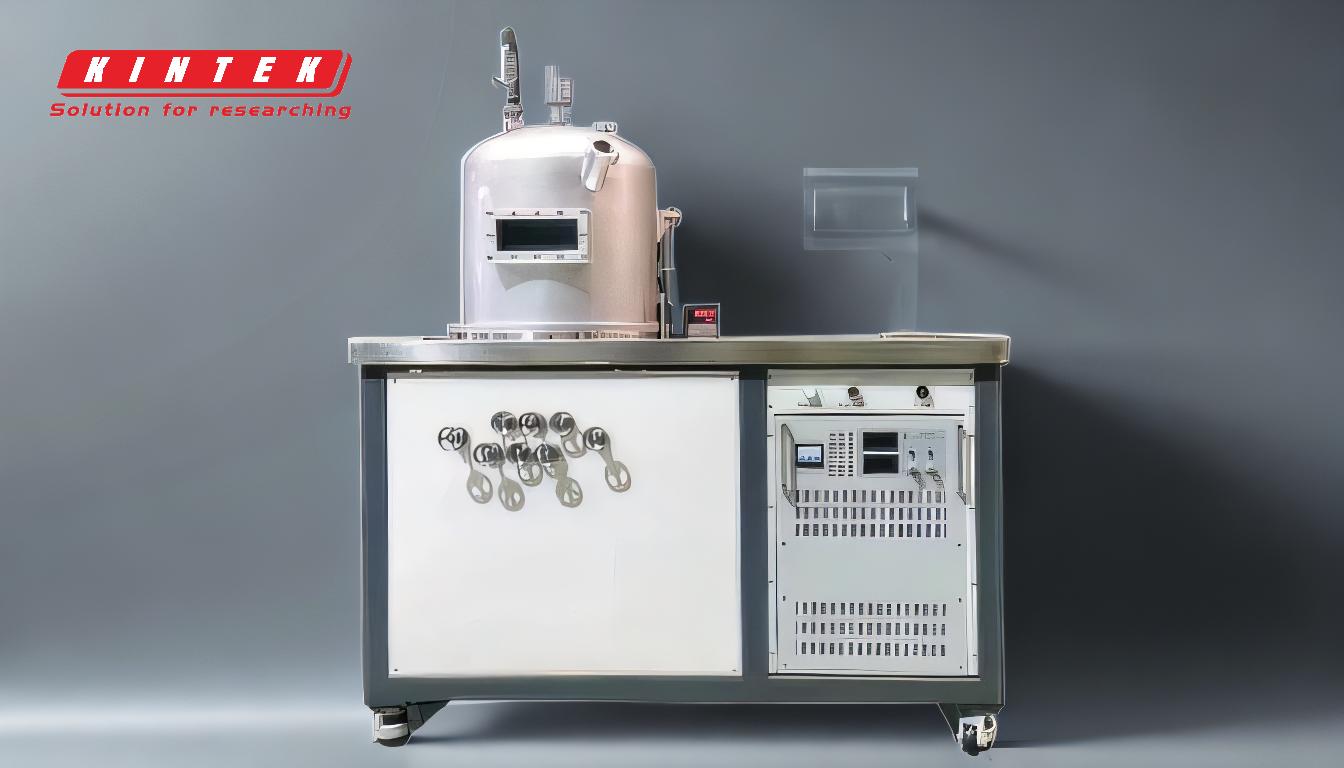
-
Substrate Preparation
- Cleaning: The substrate must be thoroughly cleaned to remove any contaminants, such as oils, dust, or oxides, that could interfere with coating adhesion. This is typically done using chemical cleaning, ultrasonic cleaning, or plasma cleaning.
- Pretreatment: Pretreatment processes, such as ion etching or surface activation, are often employed to improve the substrate's surface energy and enhance the adhesion of the coating.
-
Creation of a High-Vacuum Environment
- The substrate and target material are placed in a vacuum chamber, which is then evacuated to create a high-vacuum environment. This step is crucial to prevent contamination from atmospheric gases and ensure a clean deposition process.
- The vacuum pressure is carefully controlled and maintained throughout the process to optimize the conditions for vaporization and deposition.
-
Vaporization of the Target Material
- The target material (e.g., titanium, chromium, or aluminum) is bombarded with high-energy sources, such as electrons, ions, or photons, to dislodge atoms from its surface. This process is known as evaporation or ablation.
- The vaporized atoms form a cloud of material within the vacuum chamber, ready for transportation to the substrate.
-
Transportation of Vaporized Atoms
- The vaporized atoms are transported from the target material to the substrate through the vacuum chamber. This step is critical for ensuring a uniform distribution of the coating material.
- The transportation process is influenced by factors such as the geometry of the chamber, the distance between the target and substrate, and the energy of the vaporized atoms.
-
Reaction with Gases (Optional)
- In some cases, the vaporized metal atoms react with introduced gases, such as nitrogen, oxygen, or acetylene, to form compounds like metal nitrides, oxides, or carbides. This step is essential for creating specific coating properties, such as hardness or color.
- The reaction is carefully controlled to achieve the desired chemical composition and coating characteristics.
-
Deposition onto the Substrate
- The vaporized atoms or compounds condense onto the substrate, forming a thin, uniform film. The deposition process is influenced by factors such as substrate temperature, deposition rate, and the energy of the incoming atoms.
- The coating bonds strongly with the substrate, creating a durable and adherent layer that enhances the substrate's performance.
-
Post-Deposition Processes
- Purging: After deposition, the chamber is purged with inert gases, such as argon, to remove any residual vapors and prevent contamination.
- Finishing: Additional finishing processes, such as polishing or annealing, may be applied to improve the coating's appearance or performance.
- Quality Control: The coated substrate undergoes rigorous quality control checks to ensure the coating meets specifications for thickness, adhesion, and other properties.
By following these steps, the PVD coating process produces high-quality coatings that are widely used in industries such as aerospace, automotive, medical devices, and consumer electronics. The process's precision and versatility make it a preferred method for applying functional and decorative coatings to a wide range of materials.
Summary Table:
Step | Description |
---|---|
1. Substrate Preparation | - Cleaning: Removes contaminants for better adhesion. |
- Pretreatment: Improves surface energy for enhanced coating adhesion. | |
2. High-Vacuum Environment | - Creates a contamination-free environment for deposition. |
3. Vaporization | - Target material is vaporized using high-energy sources. |
4. Transportation | - Vaporized atoms are transported to the substrate for uniform distribution. |
5. Reaction with Gases | - Optional step to create specific coating properties (e.g., hardness, color). |
6. Deposition | - Atoms condense onto the substrate, forming a durable, adherent coating. |
7. Post-Deposition | - Purging, finishing, and quality control ensure coating meets specifications. |
Discover how the PVD coating process can elevate your product's performance—contact us today for expert advice!