Laser sintering tolerances are critical for ensuring the precision and quality of 3D-printed parts. The process involves using a laser to fuse powdered material layer by layer, and achieving tight tolerances is essential for applications requiring high accuracy. Based on the provided reference, tailored sintering techniques can achieve tolerances within one micron for linearity and concentricity. This level of precision is achievable through advanced control of laser parameters, material properties, and process optimization.
Key Points Explained:
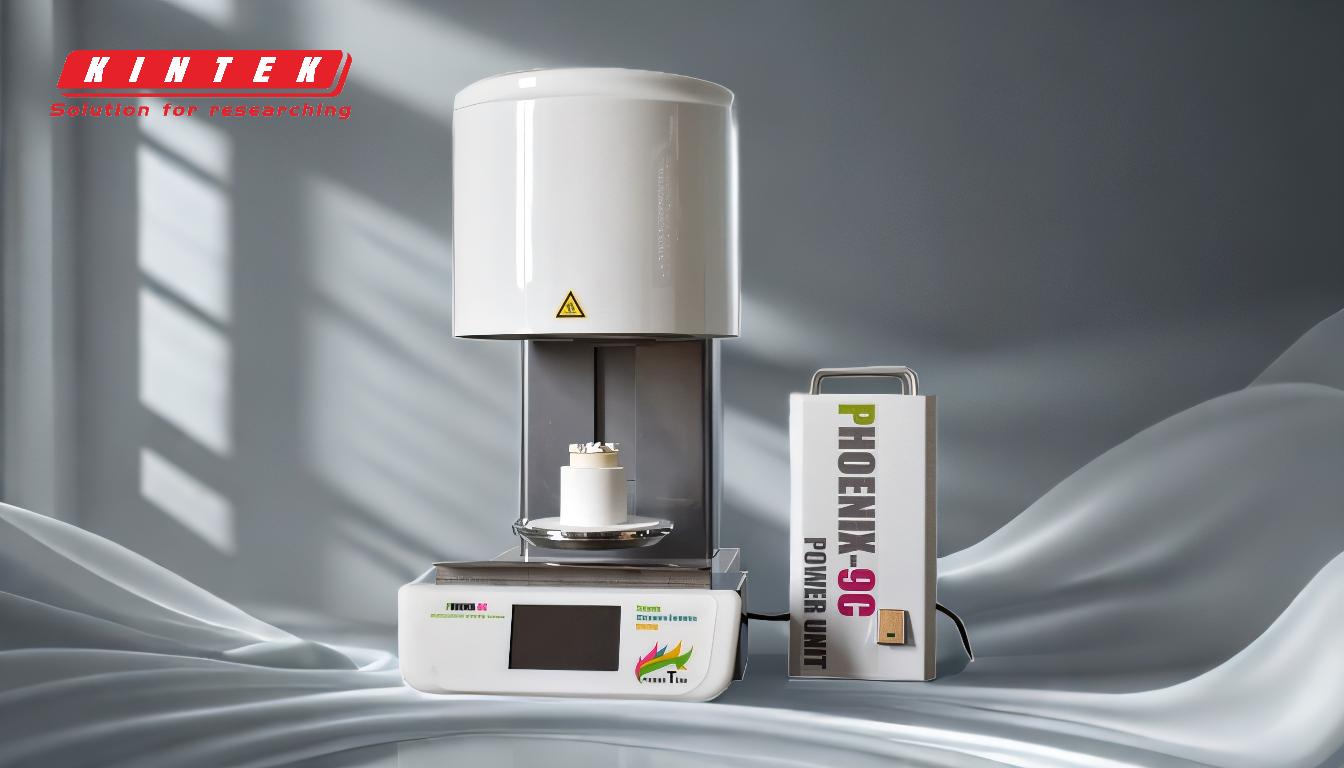
-
Definition of Tolerances in Laser Sintering:
- Tolerances refer to the allowable deviation from a specified dimension or geometry in a manufactured part.
- In laser sintering, tolerances are influenced by factors such as laser power, scanning speed, layer thickness, and material properties.
-
Achieving Tolerances Within One Micron:
- The reference states that tailored sintering techniques can ensure linearity and concentricity within one micron.
- This level of precision is achieved through:
- Advanced Laser Control: Precise control of laser power and scanning speed to minimize variations.
- Material Optimization: Using materials with consistent particle size and distribution to ensure uniform sintering.
- Process Monitoring: Real-time monitoring and adjustment of the sintering process to maintain tight tolerances.
-
Factors Influencing Tolerances:
- Laser Parameters: The intensity, focus, and scanning pattern of the laser significantly impact the accuracy of the sintered part.
- Layer Thickness: Thinner layers generally allow for higher precision but may increase build time.
- Material Properties: The thermal conductivity, melting point, and particle size of the material affect how well it sinters and the final dimensional accuracy.
- Machine Calibration: Regular calibration of the laser sintering machine is essential to maintain consistent performance.
-
Applications Requiring Tight Tolerances:
- Medical Devices: Components such as implants and surgical tools require high precision to ensure proper fit and function.
- Aerospace: Parts for aircraft and spacecraft must meet stringent tolerances to ensure safety and performance.
- Microelectronics: Small, intricate components for electronic devices often require tolerances within a few microns.
-
Challenges in Maintaining Tolerances:
- Thermal Distortion: The heat generated during sintering can cause parts to warp or deform, affecting dimensional accuracy.
- Material Shrinkage: Some materials shrink as they cool, which must be accounted for in the design and sintering process.
- Surface Finish: Achieving a smooth surface finish while maintaining tight tolerances can be challenging.
-
Strategies for Improving Tolerances:
- Process Optimization: Fine-tuning laser parameters and sintering strategies to minimize deviations.
- Post-Processing: Techniques such as machining or polishing can be used to achieve the desired tolerances and surface finish.
- Design for Additive Manufacturing (DfAM): Designing parts with sintering tolerances in mind, such as incorporating allowances for shrinkage or distortion.
In conclusion, laser sintering can achieve tolerances within one micron for linearity and concentricity through advanced techniques and careful control of process parameters. However, maintaining such tight tolerances requires a combination of optimized materials, precise laser control, and thorough process monitoring. These tolerances are essential for high-precision applications in industries such as medical, aerospace, and microelectronics.
Summary Table:
Key Aspect | Details |
---|---|
Tolerance Definition | Allowable deviation from specified dimensions in laser-sintered parts. |
Achieving 1-Micron Precision | Advanced laser control, material optimization, and real-time process monitoring. |
Influencing Factors | Laser parameters, layer thickness, material properties, and machine calibration. |
Applications | Medical devices, aerospace, and microelectronics. |
Challenges | Thermal distortion, material shrinkage, and surface finish. |
Improvement Strategies | Process optimization, post-processing, and Design for Additive Manufacturing (DfAM). |
Need precision laser sintering for your project? Contact our experts today to learn more!