Tempering is a heat treatment process used to improve the mechanical properties of metals, particularly steel, by reducing brittleness and increasing toughness. The two main types of tempering methods are low-temperature tempering and high-temperature tempering. Low-temperature tempering is typically used to retain hardness while reducing brittleness, making it suitable for tools and components that require high wear resistance. High-temperature tempering, on the other hand, is used to achieve a balance between strength and toughness, making it ideal for structural components. Each method has specific temperature ranges and applications, depending on the desired mechanical properties of the material.
Key Points Explained:
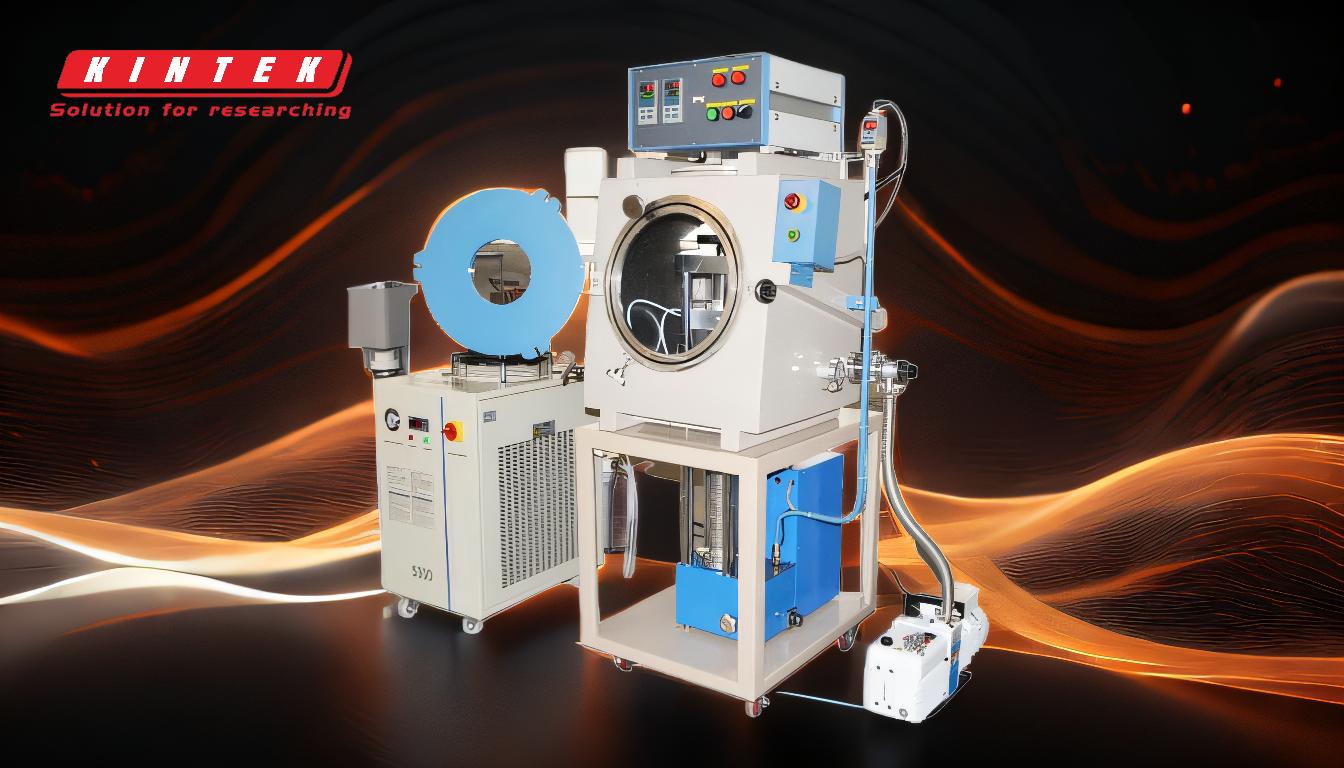
-
Low-Temperature Tempering
- Temperature Range: Typically between 150°C to 250°C (302°F to 482°F).
- Purpose: Retains a significant portion of the material's hardness while reducing brittleness.
- Applications: Commonly used for cutting tools, knives, and components requiring high wear resistance.
- Process: After quenching, the material is heated to the low-temperature range and held for a specific duration before cooling. This process helps relieve internal stresses without significantly reducing hardness.
- Result: The material maintains high hardness but gains improved toughness and reduced risk of cracking.
-
High-Temperature Tempering
- Temperature Range: Typically between 500°C to 650°C (932°F to 1202°F).
- Purpose: Achieves a balance between strength and toughness, making the material more ductile and less brittle.
- Applications: Ideal for structural components like gears, shafts, and machinery parts that require both strength and the ability to withstand impact.
- Process: The material is heated to the high-temperature range, held for a specific time, and then cooled. This process allows for the formation of tempered martensite, which provides a good combination of strength and toughness.
- Result: The material becomes more ductile and less prone to cracking under stress, while still retaining sufficient strength for structural applications.
-
Comparison of the Two Methods
- Hardness vs. Toughness: Low-temperature tempering prioritizes hardness, while high-temperature tempering emphasizes toughness.
- Microstructural Changes: Low-temperature tempering results in the formation of fine carbides within the martensitic structure, whereas high-temperature tempering leads to the coarsening of carbides and the formation of tempered martensite.
- Applications: The choice between the two methods depends on the intended use of the material—whether it requires high wear resistance (low-temperature tempering) or a balance of strength and toughness (high-temperature tempering).
-
Factors Influencing Tempering Method Selection
- Material Composition: The alloying elements in the steel can influence the tempering response and the optimal temperature range.
- Desired Mechanical Properties: The end-use requirements, such as hardness, toughness, and ductility, dictate the choice of tempering method.
- Quenching Process: The cooling rate during quenching can affect the microstructure and, consequently, the tempering behavior.
By understanding these two main tempering methods and their applications, equipment and consumable purchasers can make informed decisions about the heat treatment processes required for specific components, ensuring optimal performance and longevity.
Summary Table:
Tempering Method | Temperature Range | Purpose | Applications | Result |
---|---|---|---|---|
Low-Temperature | 150°C to 250°C (302°F to 482°F) | Retains hardness while reducing brittleness. | Cutting tools, knives, high wear resistance components. | High hardness, improved toughness, reduced cracking risk. |
High-Temperature | 500°C to 650°C (932°F to 1202°F) | Balances strength and toughness, increases ductility. | Gears, shafts, machinery parts requiring strength and impact resistance. | Improved ductility, reduced brittleness, sufficient strength. |
Need help selecting the right tempering method for your application? Contact our experts today for personalized guidance!