Casting machines are essential equipment in manufacturing processes, particularly in metalworking, where they are used to shape molten metal into desired forms. The two primary types of casting machines are die casting machines and continuous casting machines. Die casting machines are used for high-pressure injection of molten metal into reusable molds, making them ideal for producing complex, high-precision parts. Continuous casting machines, on the other hand, are used for producing long, uniform metal shapes like billets, slabs, or rods by solidifying molten metal in a continuous process. Both types of machines have unique applications, advantages, and limitations, depending on the manufacturing requirements.
Key Points Explained:
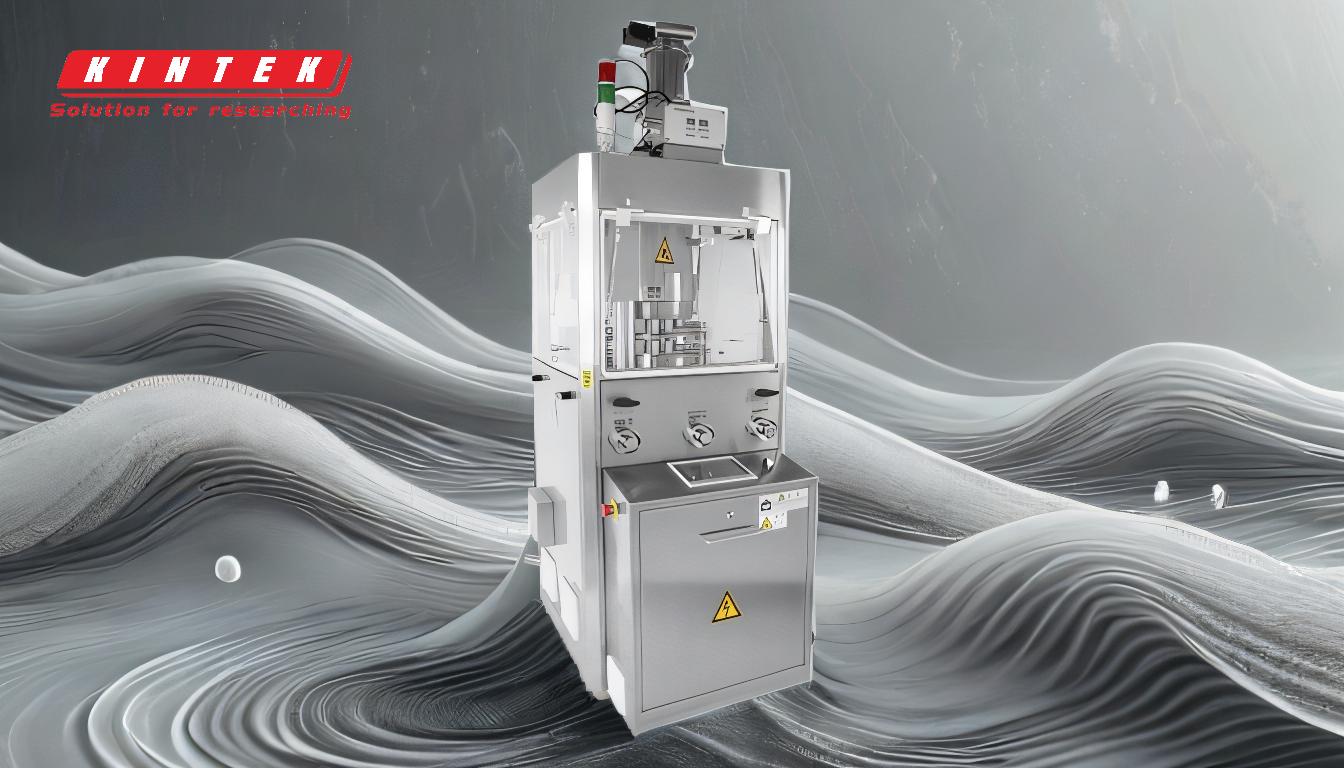
-
Die Casting Machines
- Die casting machines are designed for high-pressure injection of molten metal into reusable steel molds, known as dies.
- These machines are widely used in industries requiring high-volume production of intricate metal parts, such as automotive, aerospace, and consumer electronics.
- The process involves melting metal (typically aluminum, zinc, or magnesium) and injecting it into the die under high pressure.
- Once the metal solidifies, the die is opened, and the part is ejected.
- Advantages:
- High production speed and efficiency.
- Excellent dimensional accuracy and surface finish.
- Ability to produce complex shapes with thin walls.
- Limitations:
- High initial cost for dies and machinery.
- Limited to non-ferrous metals due to high-pressure requirements.
-
Continuous Casting Machines
- Continuous casting machines are used to produce long, uniform metal shapes, such as billets, slabs, or rods, in a continuous process.
- This method is commonly used in the steel and aluminum industries for producing semi-finished products that are further processed into final products.
- The process involves pouring molten metal into a water-cooled mold, where it solidifies and is continuously drawn out as a solid strand.
- Advantages:
- High production efficiency and reduced material waste.
- Improved product quality with uniform microstructure.
- Suitable for large-scale production of standardized shapes.
- Limitations:
- Limited flexibility in producing complex shapes.
- High initial investment in machinery and infrastructure.
-
Comparison of Die Casting and Continuous Casting
- Applications: Die casting is ideal for producing small, intricate parts, while continuous casting is suited for large-scale production of standardized shapes.
- Materials: Die casting is primarily used for non-ferrous metals, whereas continuous casting is commonly used for steel and aluminum.
- Production Volume: Die casting is more suitable for high-volume production of small parts, while continuous casting is better for producing large quantities of semi-finished products.
- Cost: Die casting involves higher tooling costs due to the need for reusable dies, while continuous casting requires significant investment in machinery and infrastructure.
-
Choosing the Right Casting Machine
- The choice between die casting and continuous casting depends on the specific requirements of the manufacturing process, such as the type of metal, desired product shape, production volume, and budget.
- For high-precision, complex parts in non-ferrous metals, die casting is the preferred option.
- For large-scale production of standardized shapes in steel or aluminum, continuous casting is more suitable.
By understanding the differences and applications of these two types of casting machines, manufacturers can make informed decisions to optimize their production processes and achieve the desired outcomes.
Summary Table:
Aspect | Die Casting Machines | Continuous Casting Machines |
---|---|---|
Applications | High-precision, complex parts (e.g., automotive, aerospace) | Large-scale production of standardized shapes (e.g., steel billets, aluminum slabs) |
Materials | Non-ferrous metals (e.g., aluminum, zinc, magnesium) | Steel, aluminum |
Production Volume | High-volume production of small parts | Large quantities of semi-finished products |
Advantages | High speed, excellent accuracy, complex shapes | High efficiency, reduced waste, uniform microstructure |
Limitations | High tooling costs, limited to non-ferrous metals | Limited flexibility, high infrastructure investment |
Need help choosing the right casting machine for your manufacturing needs? Contact our experts today!