Heat treatment furnaces are critical in various industries for altering the physical and mechanical properties of materials. The two primary types of furnace technologies used in heat treatment are atmosphere-controlled furnaces and vacuum furnaces. Atmosphere-controlled furnaces use a controlled environment to prevent oxidation and decarburization, while vacuum furnaces operate in a vacuum to eliminate impurities and achieve high-quality surface finishes. Both technologies are essential for achieving precise heat treatment results, with vacuum furnaces being particularly valued for their ability to produce clean, bright, and transmutation-free surfaces.
Key Points Explained:
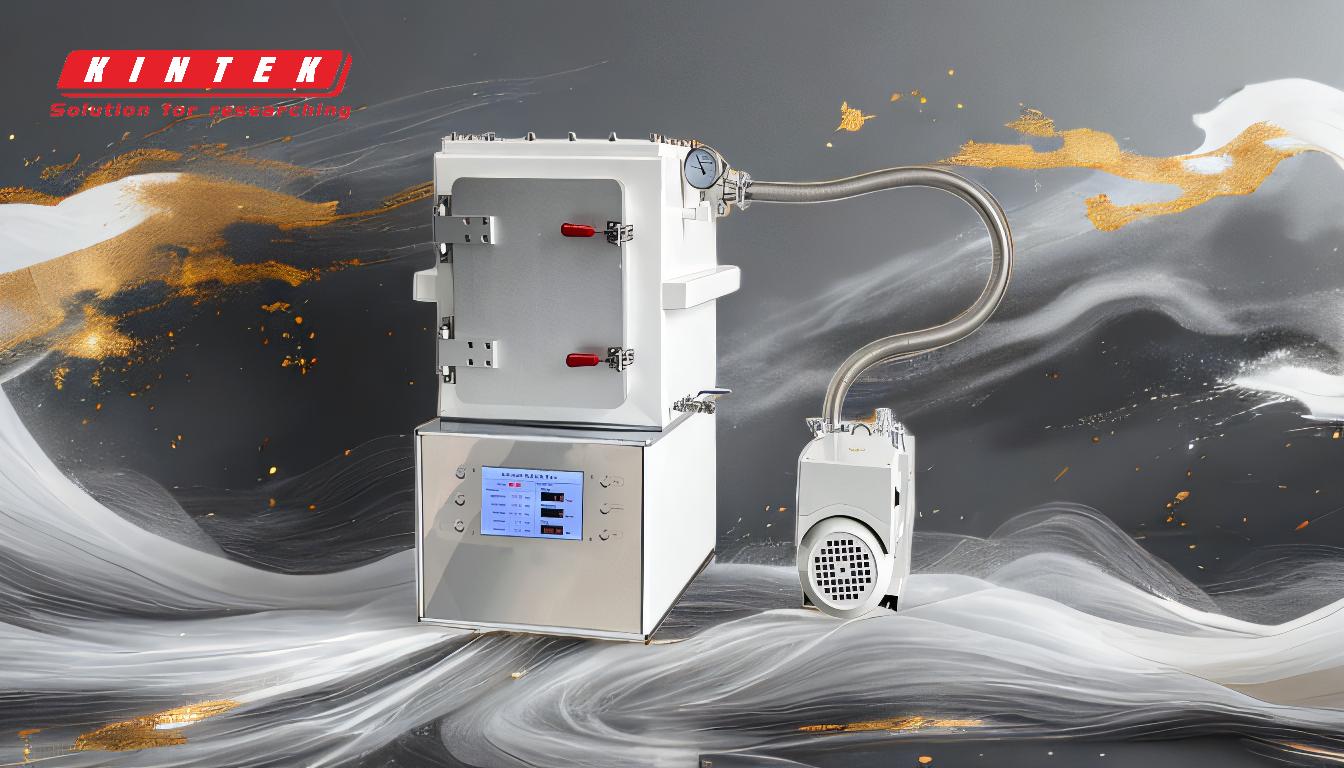
-
Atmosphere-Controlled Furnaces:
- These furnaces use a controlled atmosphere, such as inert gases (e.g., nitrogen or argon) or reducing gases (e.g., hydrogen), to protect the workpiece from oxidation and decarburization during heating.
- They are widely used in industries like automotive, aerospace, and tool manufacturing, where maintaining material integrity is crucial.
- The controlled environment allows for precise heat treatment processes, such as annealing, hardening, and tempering, without compromising the material's surface quality.
-
Vacuum Furnaces:
- Vacuum furnaces operate in a vacuum environment, which eliminates impurities and contaminants during the heating process. This results in a clean, bright, and transmutation-free surface, making them ideal for high-precision applications.
- They are commonly used in industries like aerospace, medical device manufacturing, and electronics, where surface quality and material purity are paramount.
- The absence of oxygen and other reactive gases prevents oxidation, ensuring that the workpiece retains its desired properties without surface defects.
-
Applications and Advantages:
- Atmosphere-Controlled Furnaces: Ideal for processes requiring consistent and repeatable results, such as case hardening and annealing. They are cost-effective for large-scale production and can handle a wide range of materials.
- Vacuum Furnaces: Best suited for high-value components where surface finish and material purity are critical. They are particularly advantageous for heat-treating materials like titanium, superalloys, and stainless steel.
-
Comparison of Technologies:
- Atmosphere-Controlled Furnaces: Offer flexibility and cost efficiency but may require additional steps to achieve high surface quality.
- Vacuum Furnaces: Provide superior surface quality and material purity but are typically more expensive to operate and maintain.
By understanding the strengths and applications of these two furnace technologies, industries can select the most appropriate method for their specific heat treatment needs.
Summary Table:
Furnace Type | Key Features | Applications | Advantages |
---|---|---|---|
Atmosphere-Controlled | Uses inert or reducing gases to prevent oxidation and decarburization. | Automotive, aerospace, tool manufacturing. | Cost-effective, flexible, and ideal for large-scale production. |
Vacuum Furnaces | Operates in a vacuum to eliminate impurities and achieve high-quality finishes. | Aerospace, medical devices, electronics. | Superior surface quality, material purity, and ideal for high-value components. |
Need help choosing the right furnace for your heat treatment needs? Contact our experts today for personalized advice!