Sintering is a manufacturing process that involves the fusion of particles to form a solid mass, typically used for materials with high melting points such as metals, ceramics, and polymers. The choice of binder in sintering depends on the material being processed and the desired properties of the final product. Binders are crucial as they help in shaping the material before sintering and often burn off or decompose during the process. Common binders include organic compounds, polymers, and sometimes inorganic materials, depending on the application. For metals, binders like wax or polymers are often used, while ceramics may require organic additives to improve handling before sintering. The selection of a binder is critical to ensure the integrity and performance of the sintered product.
Key Points Explained:
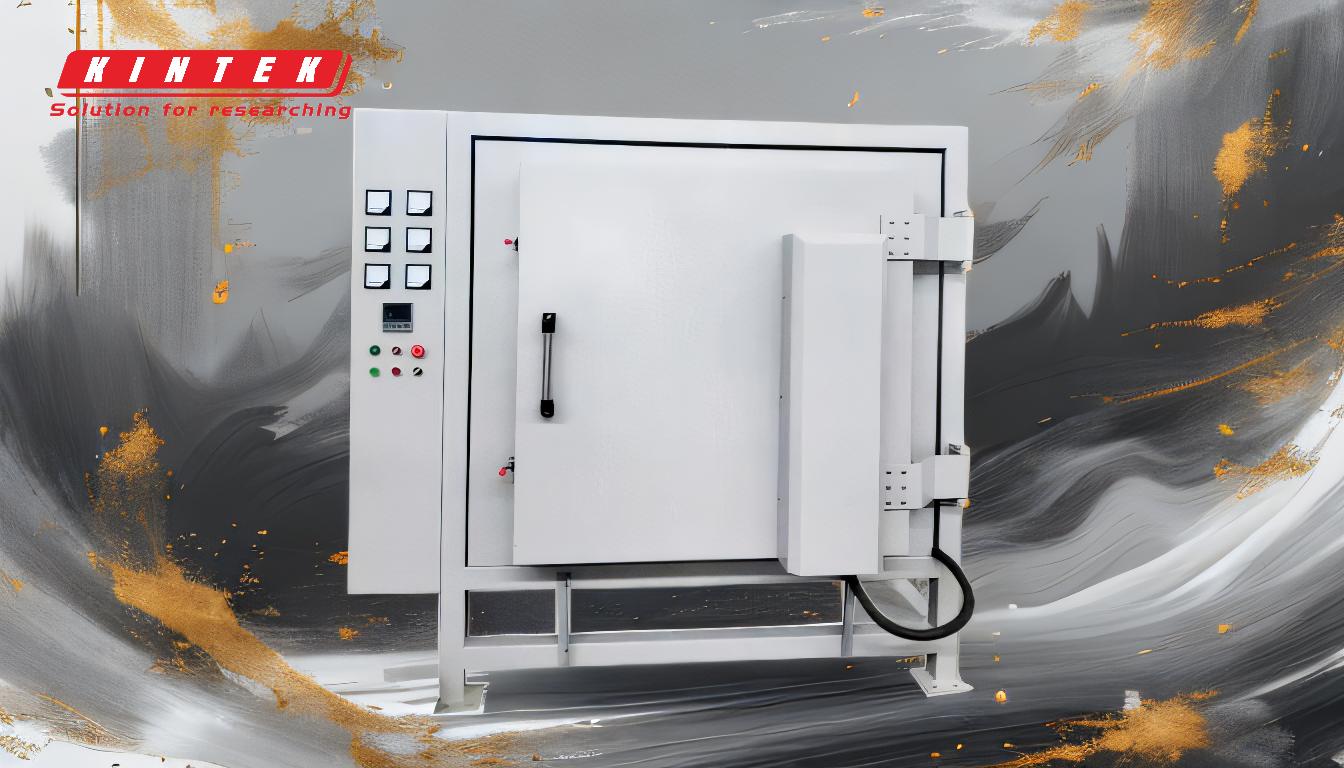
-
Role of Binders in Sintering:
- Binders are essential in the sintering process as they help in shaping the material into the desired form before the actual sintering occurs.
- They provide temporary strength to the green (unsintered) part, allowing it to be handled and transported without breaking.
- During sintering, binders typically burn off or decompose, leaving behind the sintered material with the desired properties.
-
Types of Binders Used:
- Organic Binders: These are commonly used in metal sintering. Examples include waxes, polymers, and other organic compounds that can be easily removed during the sintering process.
- Inorganic Binders: These are less common but may be used in specific applications, especially in ceramic sintering, where they can enhance certain properties of the final product.
- Polymeric Binders: These are widely used in both metal and ceramic sintering. They offer good adhesion and can be tailored to decompose at specific temperatures, which is crucial for the sintering process.
-
Application-Specific Binders:
- For Metals: Binders like polyethylene glycol (PEG) or polyvinyl alcohol (PVA) are often used. These binders are chosen for their ability to provide good green strength and their ease of removal during sintering.
- For Ceramics: Organic additives such as polyvinyl butyral (PVB) or acrylic resins are used to improve the handling and shaping of ceramic powders before sintering. These binders also help in reducing the water affinity of ceramic raw materials, making them easier to process.
- For Polymers: In polymer sintering, binders are typically not required as the polymer itself acts as both the material and the binder. However, in some cases, plasticizers or other additives may be used to improve the sintering process.
-
Considerations for Binder Selection:
- Compatibility: The binder must be compatible with the material being sintered. It should not react adversely with the material or degrade its properties.
- Decomposition Temperature: The binder should decompose at a temperature lower than the sintering temperature of the material. This ensures that the binder is completely removed during the sintering process, leaving no residue that could affect the final product.
- Environmental Impact: The choice of binder may also be influenced by environmental considerations. For example, some binders may release harmful gases during decomposition, which could be a concern in certain manufacturing environments.
-
Advancements in Binder Technology:
- With the advancement of sintering technologies, especially in additive manufacturing, there has been a push towards developing binders that offer better performance and environmental benefits.
- Newer binders are being designed to decompose more cleanly, reducing the environmental impact of the sintering process.
- There is also ongoing research into binders that can be recycled or reused, further enhancing the sustainability of the sintering process.
In summary, the choice of binder in sintering is a critical factor that influences the success of the process. The binder must be carefully selected based on the material being sintered, the desired properties of the final product, and environmental considerations. As sintering technologies continue to evolve, so too will the binders used in the process, leading to more efficient and sustainable manufacturing methods.
Summary Table:
Aspect | Details |
---|---|
Role of Binders | Shape materials, provide green strength, and decompose during sintering. |
Types of Binders | Organic (waxes, polymers), inorganic, and polymeric binders. |
Application-Specific | Metals: PEG, PVA; Ceramics: PVB, acrylic resins; Polymers: Rarely needed. |
Selection Criteria | Compatibility, decomposition temperature, environmental impact. |
Advancements | Cleaner decomposition, recyclable binders, and sustainable manufacturing. |
Optimize your sintering process with the right binder—contact our experts today for tailored solutions!