Heat treatment is a critical process in metallurgy and materials science, involving the controlled heating and cooling of metals to alter their physical and mechanical properties. The chemicals used in heat treatment play a vital role in achieving desired outcomes such as hardness, toughness, and corrosion resistance. These chemicals include quenching media, surface treatment agents, and protective atmospheres, each serving specific functions during the heat treatment process. Understanding the types and applications of these chemicals is essential for optimizing the heat treatment process and ensuring the quality of the final product.
Key Points Explained:
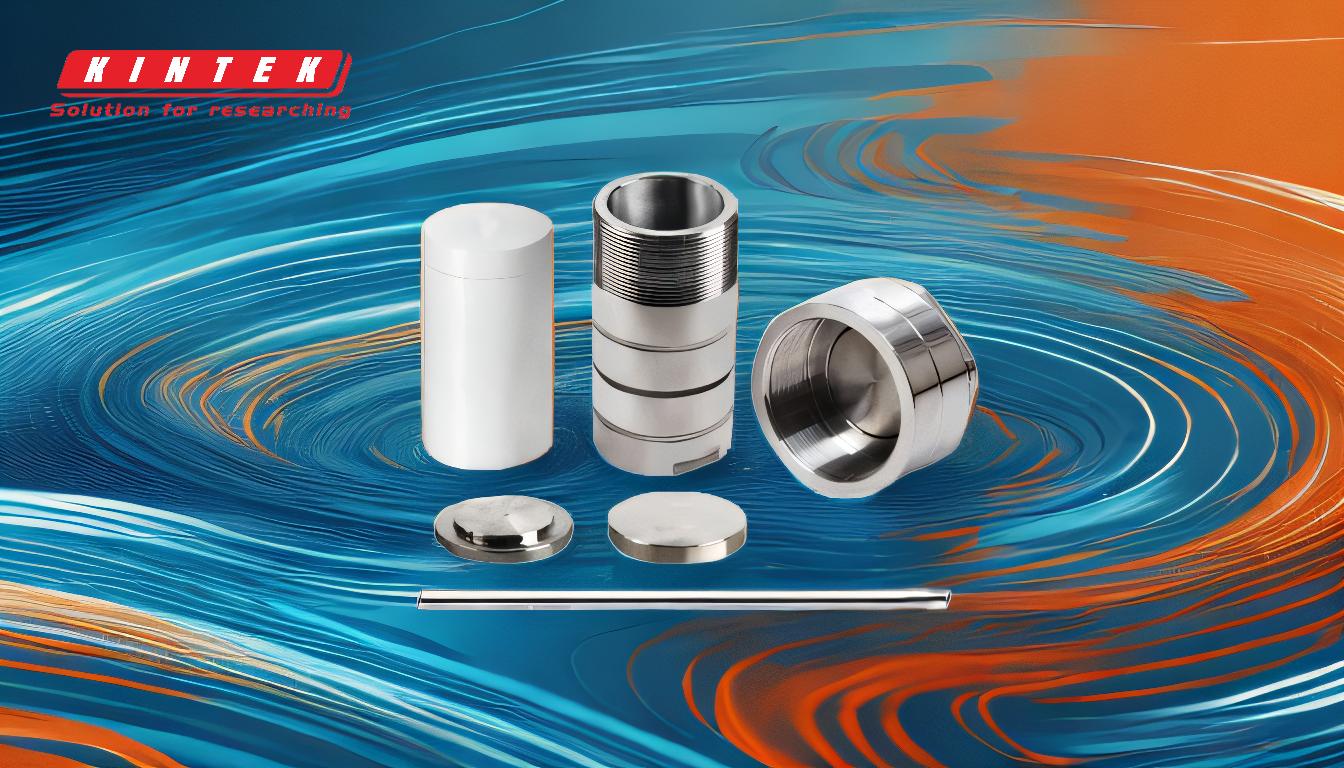
-
Quenching Media:
- Water: Commonly used for its high cooling rate, water is effective for hardening carbon steels. However, it can cause distortion or cracking due to rapid cooling.
- Oil: Oil quenching provides a slower cooling rate compared to water, reducing the risk of cracking. It is often used for alloy steels and tool steels.
- Polymer Solutions: These are water-based solutions with added polymers to control cooling rates. They offer a balance between water and oil, reducing distortion while maintaining hardness.
- Salt Baths: Molten salts are used for precise temperature control and uniform heating. They are particularly useful for tool steels and high-speed steels.
-
Surface Treatment Agents:
- Carburizing Compounds: These chemicals introduce carbon into the surface of low-carbon steels, enhancing surface hardness while maintaining a tough core. Common carburizing agents include methane, propane, and carbon monoxide.
- Nitriding Compounds: Used to introduce nitrogen into the surface of metals, nitriding compounds like ammonia gas improve wear resistance and fatigue strength. This process is typically used for alloy steels.
- Cyaniding and Carbonitriding: These processes involve the use of cyanide salts or gaseous mixtures to introduce both carbon and nitrogen into the metal surface, providing a hard, wear-resistant layer.
-
Protective Atmospheres:
- Inert Gases: Argon and nitrogen are used to create an oxygen-free environment, preventing oxidation and decarburization during heat treatment. These gases are essential for processes like annealing and brazing.
- Endothermic and Exothermic Atmospheres: These are gas mixtures generated by reacting natural gas or propane with air. Endothermic atmospheres are rich in carbon monoxide and hydrogen, used for carburizing, while exothermic atmospheres are leaner and used for annealing.
- Vacuum Environments: In some high-precision applications, heat treatment is conducted in a vacuum to eliminate any risk of oxidation or contamination.
-
Tempering Agents:
- Air: After quenching, metals are often tempered by reheating to a lower temperature and then cooling in air. This process reduces brittleness and improves toughness.
- Oil and Water: In some cases, tempering is followed by a second quenching step using oil or water to achieve specific mechanical properties.
-
Cleaning and Preparation Chemicals:
- Degreasers: Used to remove oils and contaminants from the metal surface before heat treatment. Common degreasers include alkaline solutions and solvents.
- Pickling Solutions: Acidic solutions like hydrochloric or sulfuric acid are used to remove scale and oxides from the metal surface, ensuring a clean surface for heat treatment.
-
Specialized Chemicals:
- Boronizing Agents: Used to introduce boron into the metal surface, creating a hard, wear-resistant layer. This process is used for specialized applications requiring extreme hardness.
- Aluminizing Compounds: These chemicals introduce aluminum into the metal surface, improving oxidation and corrosion resistance, particularly in high-temperature applications.
Understanding the role of these chemicals in heat treatment allows for the selection of the most appropriate agents based on the desired outcome, material type, and specific application requirements. Proper handling and application of these chemicals are crucial to achieving optimal results and ensuring the longevity and performance of the treated materials.
Summary Table:
Chemical Type | Examples | Function |
---|---|---|
Quenching Media | Water, Oil, Polymer Solutions, Salt Baths | Control cooling rates to achieve desired hardness and reduce distortion. |
Surface Treatment Agents | Carburizing Compounds, Nitriding Compounds, Cyaniding | Enhance surface hardness, wear resistance, and fatigue strength. |
Protective Atmospheres | Inert Gases, Endothermic/Exothermic Gases, Vacuum | Prevent oxidation and contamination during heat treatment. |
Tempering Agents | Air, Oil, Water | Reduce brittleness and improve toughness after quenching. |
Cleaning Chemicals | Degreasers, Pickling Solutions | Prepare metal surfaces by removing contaminants and oxides. |
Specialized Chemicals | Boronizing Agents, Aluminizing Compounds | Provide extreme hardness, wear resistance, and corrosion resistance. |
Need help selecting the right chemicals for your heat treatment process? Contact our experts today!