Intermittent (batch) and continuous furnaces are two primary classifications of furnaces based on their mode of operation and material handling. Intermittent furnaces process materials in batches, where the charge is loaded, heated according to a specific temperature curve, and then unloaded after completion. Continuous furnaces, on the other hand, handle materials in a continuous flow, with the charge being fed into the furnace at a constant speed or intervals and processed according to a predefined temperature profile. Continuous furnaces are ideal for high-volume production, offering uninterrupted heat treatment, while batch furnaces are simpler, more cost-effective, and suitable for smaller-scale or specialized applications. Understanding these differences is crucial for selecting the right furnace for specific industrial needs.
Key Points Explained:
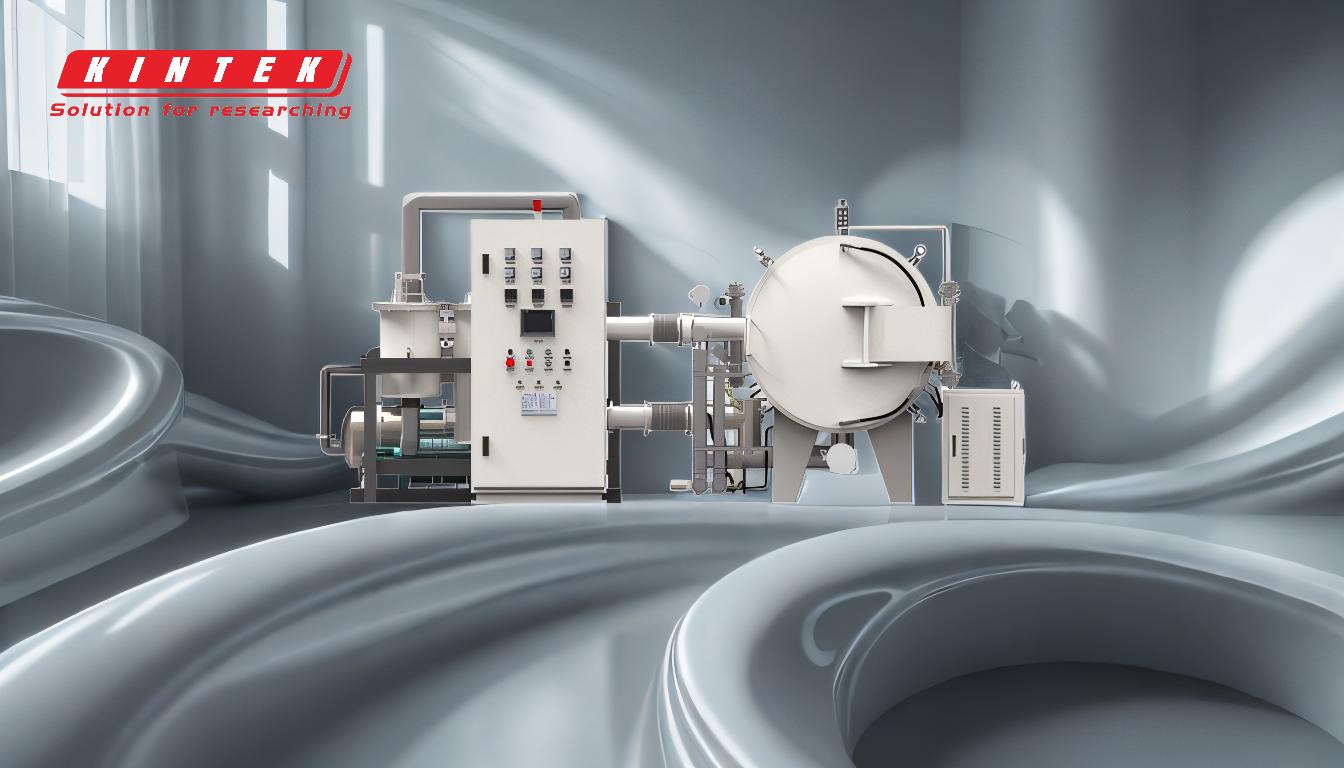
-
Definition and Operation of Intermittent (Batch) Furnaces:
- Intermittent furnaces, also known as batch furnaces, process materials in discrete batches.
- The charge is loaded into the furnace, heated according to a specific temperature curve, and then unloaded after the process is complete.
- These furnaces are typically used for smaller-scale production or specialized applications where precise control over the heating process is required.
- Examples include heat treatment of small metal parts or laboratory-scale experiments.
-
Definition and Operation of Continuous Furnaces:
- Continuous furnaces are designed to handle a continuous flow of materials.
- The charge is fed into the furnace at a constant speed or at regular intervals and moves through the furnace on a conveyor or roller system.
- The materials are heated according to a predefined temperature profile as they travel through the furnace.
- These furnaces are ideal for high-volume production, offering an uninterrupted heat treatment process.
- Examples include reheating semi-finished products for subsequent hot forming or large-scale industrial heat treatment.
-
Key Differences Between Intermittent and Continuous Furnaces:
- Material Handling: Batch furnaces process materials in discrete batches, while continuous furnaces handle materials in a continuous flow.
- Production Volume: Continuous furnaces are better suited for high-volume production, whereas batch furnaces are more appropriate for smaller-scale or specialized applications.
- Complexity and Maintenance: Continuous furnaces are generally more complex, require more frequent maintenance, and are more expensive to operate. Batch furnaces are simpler, easier to maintain, and less costly.
- Energy Consumption: Continuous furnaces often have lower overall energy consumption due to their continuous operation, while batch furnaces may require more energy per unit of material processed due to the need to heat and cool the furnace for each batch.
-
Applications of Intermittent and Continuous Furnaces:
- Batch Furnaces: Commonly used in industries requiring precise control over the heating process, such as aerospace, automotive, and laboratory research. They are also suitable for applications requiring cleanroom standards or inert atmospheres.
- Continuous Furnaces: Widely used in industries with high-volume production needs, such as steel manufacturing, glass production, and large-scale heat treatment of metal components.
-
Advantages and Disadvantages:
-
Batch Furnaces:
- Advantages: Simpler design, easier maintenance, lower initial and operational costs, suitable for small-scale or specialized applications.
- Disadvantages: Lower production capacity, higher energy consumption per unit of material, requires more work in process to form groups for loading.
-
Continuous Furnaces:
- Advantages: High production capacity, lower energy consumption per unit of material, continuous operation ideal for large-scale production.
- Disadvantages: More complex design, higher initial and operational costs, requires more frequent maintenance.
-
Batch Furnaces:
-
Considerations for Equipment Purchasers:
- Production Needs: Assess whether the production volume and process requirements align with the capabilities of batch or continuous furnaces.
- Budget and Maintenance: Consider the initial investment, operational costs, and maintenance requirements of each type of furnace.
- Material Handling: Evaluate the material handling requirements and whether the furnace can accommodate the specific needs of the production process.
- Energy Efficiency: Consider the energy consumption and efficiency of the furnace, especially for high-volume production where continuous furnaces may offer significant energy savings.
Understanding the distinctions between intermittent and continuous furnaces is essential for selecting the appropriate furnace type for specific industrial applications. Each type has its own set of advantages and disadvantages, and the choice depends on factors such as production volume, material handling requirements, and budget constraints.
Summary Table:
Aspect | Intermittent (Batch) Furnaces | Continuous Furnaces |
---|---|---|
Material Handling | Processes materials in discrete batches | Handles materials in a continuous flow |
Production Volume | Suitable for smaller-scale or specialized production | Ideal for high-volume production |
Complexity | Simpler design, easier maintenance | More complex, requires frequent maintenance |
Energy Consumption | Higher per unit of material | Lower overall energy consumption |
Applications | Aerospace, automotive, lab research | Steel manufacturing, glass production |
Need help choosing the right furnace for your production needs? Contact our experts today!