Diamond-like Carbon (DLC) coatings are advanced surface treatments that combine the hardness of diamond with the lubricity of graphite. These coatings are applied to various substrates to enhance their functional properties, such as wear resistance, corrosion resistance, and sliding performance. DLC coatings are created using a low-temperature deposition process involving hydrocarbons, which form a hard, durable layer on the surface. They are widely used in industries ranging from automotive to watchmaking, offering both functional and decorative benefits. Key attributes include high hardness, low friction, chemical resistance, and biocompatibility, making them suitable for protective, optical, and biomedical applications.
Key Points Explained:
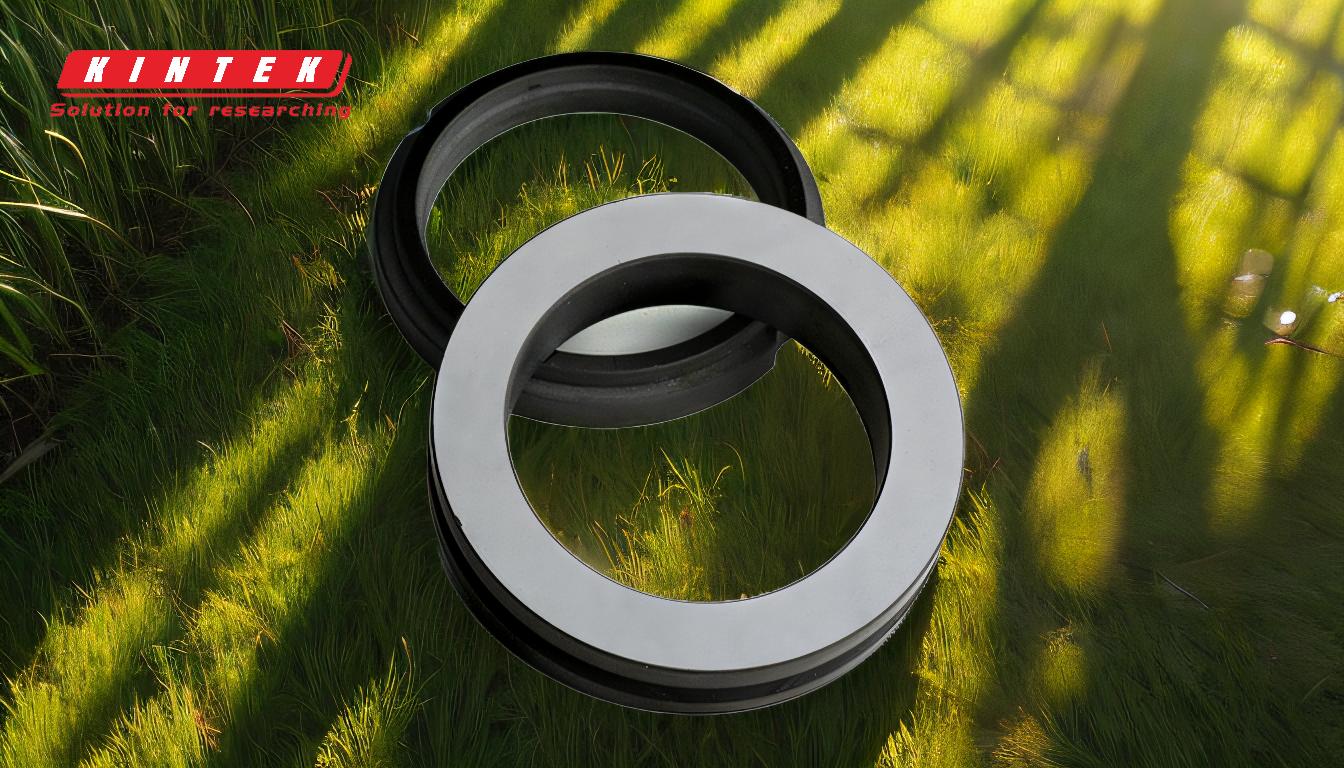
-
Composition and Structure of DLC Coatings:
- DLC coatings consist of a mixture of sp3 (diamond-like) and sp2 (graphite-like) carbon bonds.
- The sp3 bonds contribute to the coating's high hardness, while the sp2 bonds provide low friction and lubricity.
- This unique combination makes DLC coatings ideal for applications requiring both durability and smooth sliding properties.
-
Functional Properties:
- High Hardness: DLC coatings are exceptionally hard, making them resistant to wear and abrasion. This property is particularly useful in high-stress environments, such as automotive components or industrial tools.
- Low Coefficient of Friction: The graphite-like sp2 bonds reduce friction, enhancing sliding properties and reducing energy loss in moving parts.
- Corrosion Resistance: DLC coatings provide excellent protection against corrosive environments, extending the lifespan of coated materials.
- Chemical Resistance: These coatings are resistant to many chemicals, making them suitable for use in harsh industrial or biomedical settings.
- Biocompatibility: DLC coatings are safe for use in medical devices and implants due to their non-toxic and non-reactive nature.
-
Deposition Process:
- DLC coatings are deposited using a low-temperature process (around 300 °C), which makes them suitable for temperature-sensitive substrates.
- The process involves the use of hydrocarbons (hydrogen and carbon). These elements enter a plasma state, where they bond and recombine on the substrate surface to form the hard, durable coating.
- Adhesion Enhancement: To improve adhesion, silicon-based films are often predeposited on substrates like steel or hard metals.
-
Applications:
- Industrial Tools and Components: DLC coatings are used to enhance the durability and performance of cutting tools, molds, and bearings.
- Automotive Industry: They are applied to engine components, such as piston rings and fuel injectors, to reduce friction and wear.
- Decorative Uses: DLC coatings provide a sleek, black finish with high hardness, making them popular in luxury watches and jewelry.
- Optical and Biomedical Applications: Due to their precise control over thickness and refractive index, DLC coatings are used in antireflective coatings and optical sensors. They are also used in medical implants and devices for their biocompatibility and protective properties.
-
Advantages for Equipment and Consumable Purchasers:
- Extended Lifespan: DLC coatings significantly increase the durability of components, reducing the need for frequent replacements.
- Improved Performance: The low friction and high hardness of DLC coatings enhance the efficiency and functionality of moving parts.
- Cost-Effectiveness: By reducing wear and corrosion, DLC coatings lower maintenance and replacement costs over time.
- Versatility: DLC coatings can be applied to a wide range of materials, including metals, ceramics, and polymers, making them suitable for diverse applications.
-
Considerations for Implementation:
- Substrate Compatibility: Ensure the substrate material is compatible with the DLC coating process, especially for temperature-sensitive materials.
- Adhesion Requirements: For optimal performance, consider using bonding layers or predeposited films to enhance adhesion on specific substrates.
- Application-Specific Properties: Tailor the coating's properties (e.g., hardness, friction, thickness) to meet the specific needs of the application.
In summary, DLC coatings offer a unique combination of hardness, low friction, and chemical resistance, making them highly valuable for both functional and decorative applications. Their versatility and performance benefits make them an excellent choice for equipment and consumable purchasers looking to enhance durability, efficiency, and cost-effectiveness.
Summary Table:
Key Attribute | Description |
---|---|
High Hardness | Exceptional resistance to wear and abrasion. |
Low Friction | Reduces energy loss and enhances sliding performance. |
Corrosion Resistance | Protects against harsh environments, extending material lifespan. |
Chemical Resistance | Resistant to many chemicals, ideal for industrial and biomedical applications. |
Biocompatibility | Safe for medical devices and implants. |
Deposition Process | Low-temperature process using hydrocarbons, suitable for sensitive substrates. |
Applications | Automotive, industrial tools, decorative, optical, and biomedical uses. |
Learn how DLC coatings can improve your equipment's performance—contact us today!