Sintering is a manufacturing process that involves compacting and forming a solid mass of material by applying heat and pressure without melting the material to the point of liquefaction. This technique is crucial in producing density-controlled materials and components from metal, ceramic, or plastic powders. Sintering enhances material properties such as strength, structural integrity, and reduced porosity, making it a vital process in industries like ceramics, metallurgy, and plastics. Understanding sintering is essential because it allows for the creation of durable, high-performance materials with tailored properties, even for metals with high melting points, without requiring complete liquefaction.
Key Points Explained:
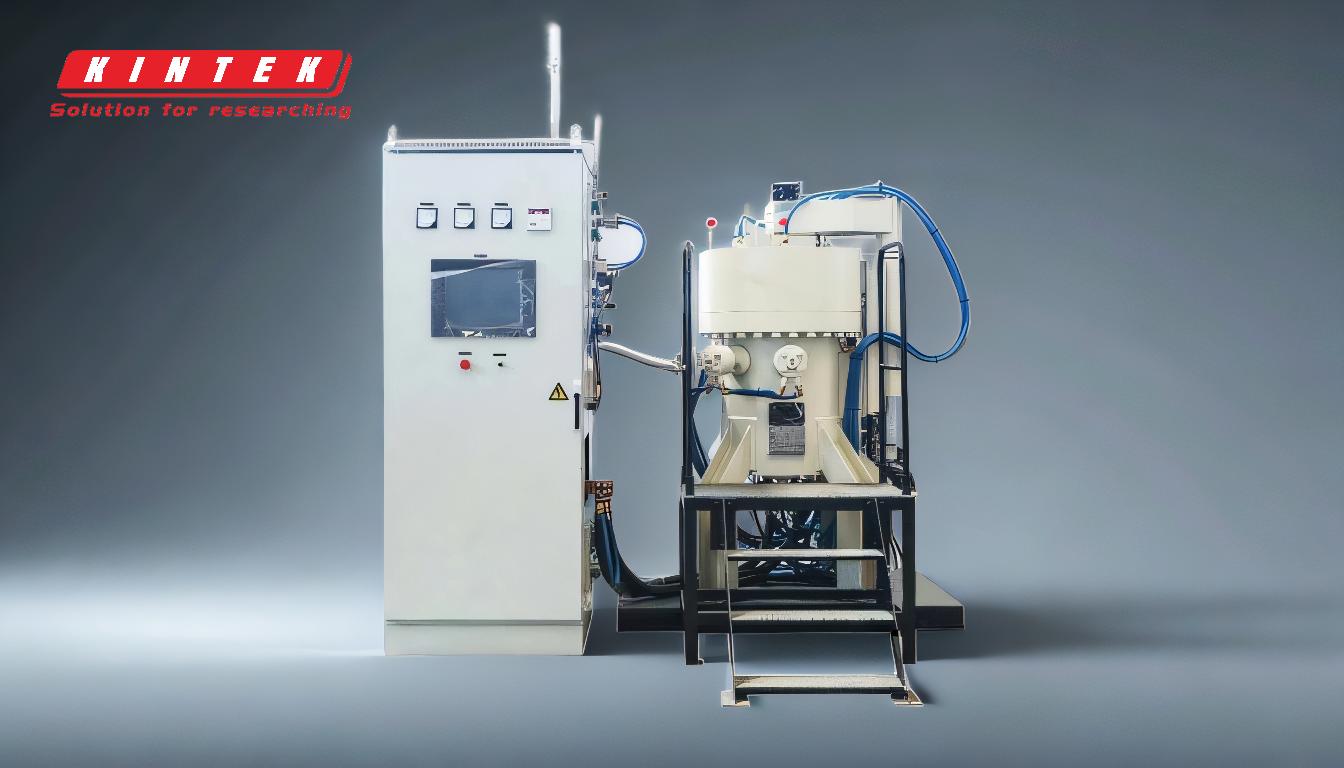
-
Definition of Sintering:
- Sintering is a process that uses heat and pressure to fuse particles of powder material into a solid mass without melting the material entirely.
- It involves atomic diffusion across particle boundaries, leading to the formation of a dense, compact structure.
-
Origin of the Term "Sintered":
- The term originates from the German word "sinter," meaning "cinder" or "ash."
- It entered the English language in the late 18th century and has since been associated with processes involving heat and compaction.
-
How Sintering Works:
- Powdered material is placed in a mold or shaped using high-pressure compression, often with a temporary binder.
- The material is heated to a temperature below its melting point, allowing atoms to diffuse across particle boundaries and fuse together.
- This process reduces porosity and compacts the material into a solid object.
-
Applications of Sintering:
- Ceramics: Used to create durable, high-strength ceramic components.
- Metals: Enables the production of metal parts with high melting points without needing to melt the material.
- Plastics: Used to form sintered plastics with enhanced properties.
- Natural Processes: Occurs naturally in mineral deposits, leading to the formation of dense rock structures.
-
Importance of Sintering:
- Enhanced Material Properties: Sintering improves strength, structural integrity, and reduces porosity.
- Customizable Density: Allows for the creation of materials with controlled density and tailored properties.
- Energy Efficiency: Since the material does not need to be fully melted, sintering is often more energy-efficient than other manufacturing processes.
- Versatility: Suitable for a wide range of materials, including those with high melting points.
-
Stages of Sintering:
- Initial Stage: Powder particles are compacted and begin to bond at contact points.
- Intermediate Stage: Porosity decreases as particles fuse further, and the material becomes denser.
- Final Stage: The material achieves maximum density and strength, with minimal porosity.
-
Advantages of Sintered Materials:
- Improved Electrical and Thermal Conductivity: Sintering enhances these properties, making the materials suitable for electronic and thermal applications.
- Translucency: In ceramics, sintering can produce translucent materials.
- Cost-Effectiveness: The process is often more economical than traditional melting and casting methods.
-
Why Understanding Sintering Matters:
- Material Selection: Knowing how sintering works helps in choosing the right materials for specific applications.
- Quality Control: Understanding the process ensures better control over the final product's properties.
- Innovation: Sintering enables the development of advanced materials with unique properties, driving innovation in various industries.
In summary, sintering is a critical process in materials science and manufacturing, offering a versatile and efficient method to create high-performance materials with tailored properties. Understanding sintering is essential for anyone involved in material selection, product design, or manufacturing processes.
Summary Table:
Aspect | Details |
---|---|
Definition | Fusing powder particles using heat and pressure without full melting. |
Origin of Term | From German 'sinter,' meaning 'cinder' or 'ash.' |
Process | Heat below melting point, atomic diffusion, reduced porosity. |
Applications | Ceramics, metals, plastics, natural mineral deposits. |
Key Benefits | Enhanced strength, reduced porosity, energy efficiency, customizable density. |
Stages | Initial bonding, intermediate densification, final maximum density. |
Advantages | Improved conductivity, translucency, cost-effectiveness. |
Importance | Essential for material selection, quality control, and innovation. |
Ready to explore how sintering can enhance your material manufacturing process? Contact our experts today!