The heating rate during heat treatment depends on a variety of factors, including the physical characteristics of the parts being treated, the design and operation of the furnace, and the specific requirements of the heat treatment process. Key factors include the surface-to-mass ratio of the parts, their color and surface finish, the furnace's temperature distribution, gas circulation, and the chosen cycle times and temperatures. Additionally, the type of heat treatment process, the material properties, and the desired outcomes also play a significant role in determining the heating rate.
Key Points Explained:
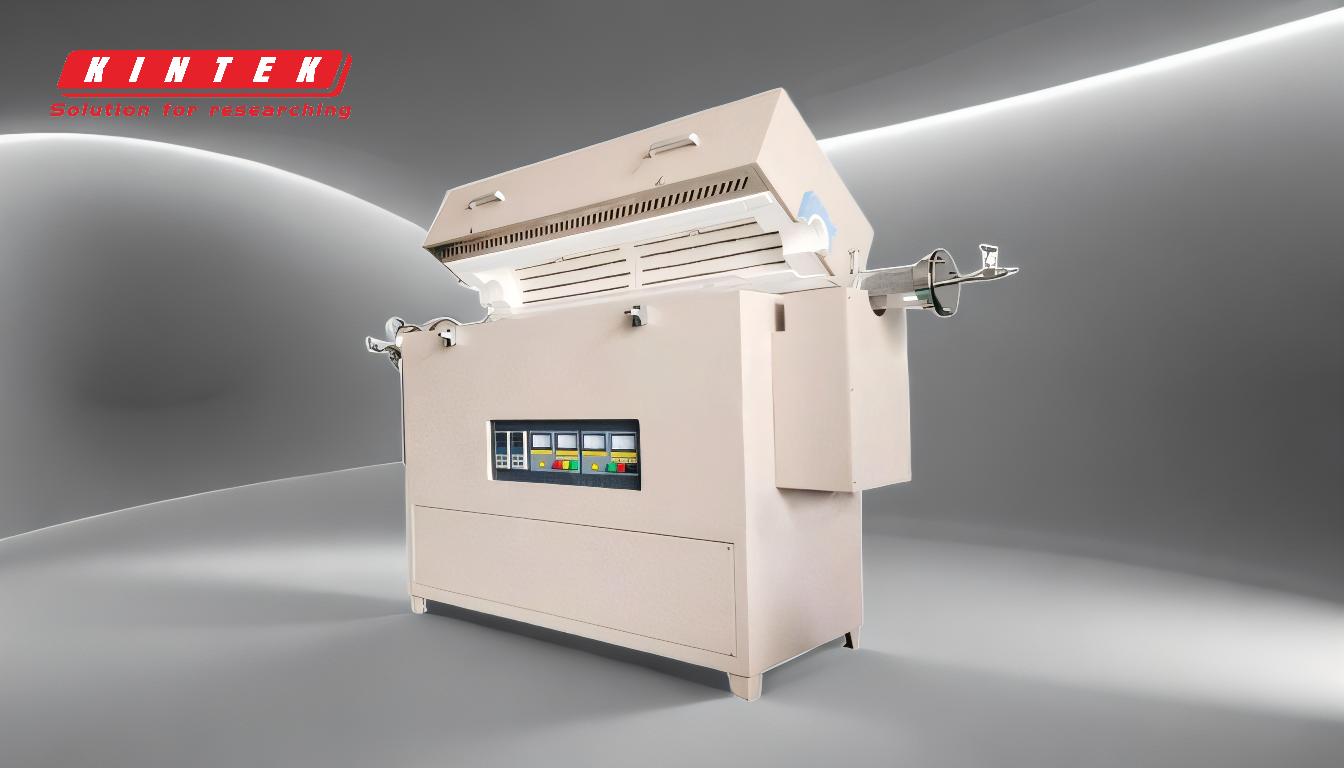
-
Physical Characteristics of the Parts:
- Surface-to-Mass Ratio: Thin and large parts with a high surface-to-mass ratio heat up faster because they have a larger surface area available for heat transfer. Thicker parts, on the other hand, take longer to heat up due to their lower surface-to-mass ratio.
- Color and Surface Finish: The color and surface finish of the parts can affect how efficiently they absorb heat. Darker colors and rougher surfaces tend to absorb heat more effectively than lighter colors and smoother surfaces.
-
Furnace Design and Operation:
- Uniform Temperature Distribution: Ensuring a uniform temperature distribution throughout the hot zone of the furnace is crucial for consistent heating rates. Non-uniform heating can lead to uneven heat treatment and potential quality issues.
- Gas Circulation: Proper gas circulation, including the use of partial pressure or quench gas, can influence the heating rate by affecting how heat is transferred to the parts.
- Cycle Times and Temperatures: The chosen cycle times and temperatures are critical in determining the heating rate. Longer cycle times and higher temperatures generally result in faster heating, but they must be carefully controlled to avoid damaging the parts.
-
Heat Treatment Process Requirements:
- Type of Heat Treatment: The specific heat treatment process used (e.g., annealing, quenching, tempering) will dictate the required heating rate. Different processes have different temperature and time requirements.
- Material Properties: The type of material being treated and its thermal properties (e.g., thermal conductivity, specific heat) will influence how quickly it heats up.
- Desired Outcomes: The desired mechanical properties (e.g., hardness, toughness) of the final product will also affect the heating rate. For example, rapid heating might be required for certain hardening processes, while slower heating might be necessary for annealing.
-
Furnace-Specific Factors:
- Inclination Angle and Rotational Speed (Rotary Tube Furnace): In rotary tube furnaces, the inclination angle and rotational speed of the tube can affect the heating rate by influencing how the material moves through the furnace and how evenly it is exposed to heat.
- Length of the Working Tube: The length of the working tube in a rotary tube furnace can also impact the heating rate, as longer tubes may require more time to achieve uniform heating.
- Flow Properties of the Batch Material: The flow properties of the material being processed, such as its density and viscosity, can affect how quickly it heats up. Materials that flow more easily may heat up more uniformly and quickly.
-
Anticipating Potential Problems:
- Maintenance and Downtime: Anticipating potential issues that could lead to maintenance or downtime is important for maintaining consistent heating rates. Regular maintenance and monitoring can help prevent unexpected delays and ensure that the furnace operates efficiently.
In summary, the heating rate during heat treatment is influenced by a complex interplay of factors related to the parts being treated, the furnace design and operation, and the specific requirements of the heat treatment process. Understanding and controlling these factors is essential for achieving the desired outcomes in heat treatment.
Summary Table:
Factor | Impact on Heating Rate |
---|---|
Surface-to-Mass Ratio | Thin parts heat faster; thicker parts take longer. |
Color and Surface Finish | Darker, rougher surfaces absorb heat more efficiently. |
Uniform Temperature | Ensures consistent heating; non-uniform heating leads to quality issues. |
Gas Circulation | Affects heat transfer; partial pressure or quench gas improves efficiency. |
Cycle Times and Temperatures | Longer cycles and higher temperatures speed up heating but require careful control. |
Material Properties | Thermal conductivity and specific heat influence heating speed. |
Desired Outcomes | Rapid heating for hardening; slower heating for annealing. |
Furnace-Specific Factors | Inclination angle, tube length, and material flow properties affect uniformity and speed. |
Need help optimizing your heat treatment process? Contact our experts today for tailored solutions!