Heat treatment of steels is a critical process in metallurgy, involving controlled heating and cooling to alter the material's physical and mechanical properties. Various types of furnaces are used for this purpose, each designed to meet specific requirements such as temperature control, atmosphere control, and uniformity of heating. The choice of furnace depends on the type of steel, the desired properties, and the scale of production. Common furnaces include box furnaces, continuous furnaces, pit furnaces, and vacuum furnaces, each offering unique advantages for different heat treatment processes like annealing, quenching, tempering, and case hardening.
Key Points Explained:
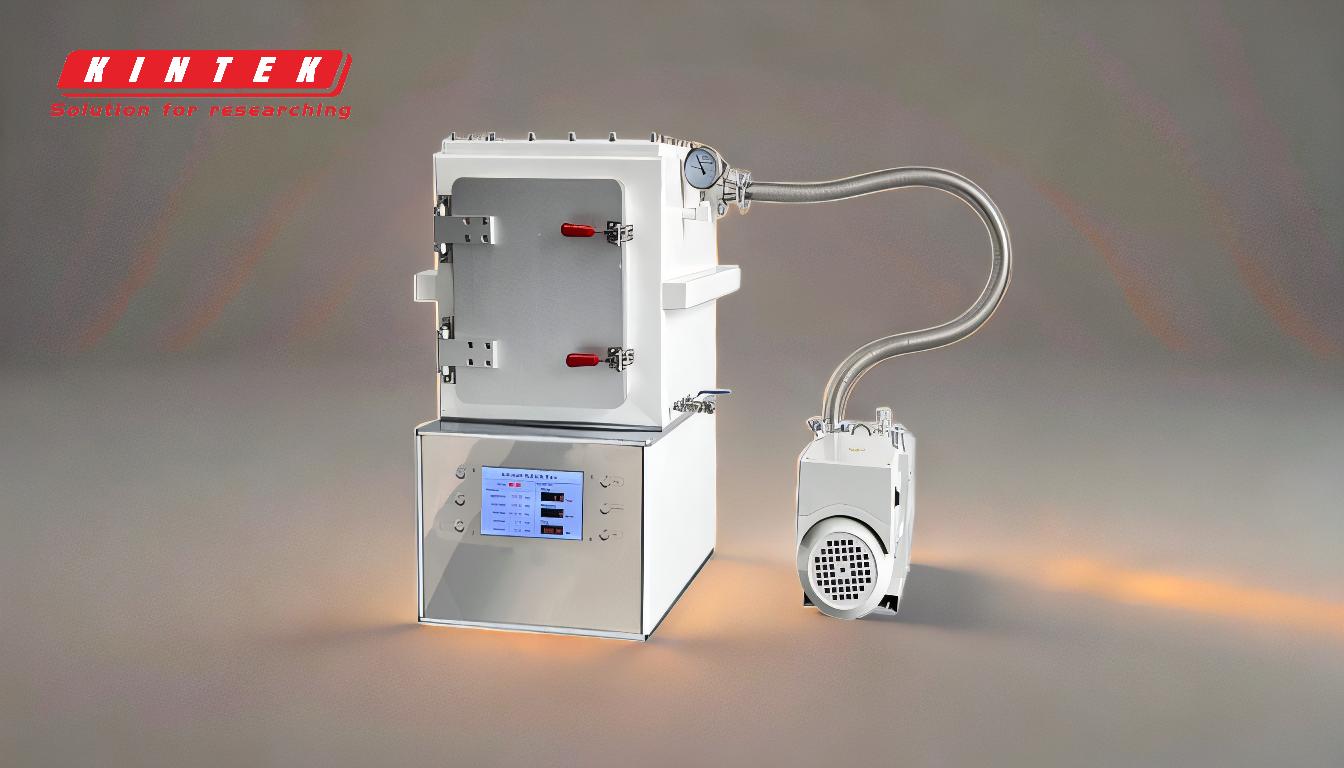
-
Box Furnaces:
- Description: Box furnaces are versatile and widely used for heat treating steels. They consist of an insulated chamber with heating elements on the sides, top, and bottom.
- Applications: Ideal for processes like annealing, normalizing, and tempering. They are suitable for small to medium-sized batches.
- Advantages: Uniform heating, ease of operation, and flexibility in handling various steel types.
- Limitations: Limited to batch processing, which can be less efficient for large-scale production.
-
Continuous Furnaces:
- Description: Continuous furnaces are designed for high-volume production. Steel parts move through the furnace on a conveyor or roller system, undergoing different heat treatment zones.
- Applications: Commonly used for processes like annealing, hardening, and tempering in large-scale manufacturing.
- Advantages: High throughput, consistent quality, and reduced labor costs.
- Limitations: Higher initial investment and less flexibility for small batches.
-
Pit Furnaces:
- Description: Pit furnaces are vertical furnaces where steel parts are loaded from the top. They are typically used for long or heavy components.
- Applications: Suitable for processes like annealing, hardening, and stress relieving of large steel parts.
- Advantages: Efficient for handling large or heavy components, good temperature uniformity.
- Limitations: Limited to specific shapes and sizes, and slower heating and cooling rates.
-
Vacuum Furnaces:
- Description: Vacuum furnaces operate in a low-pressure environment, preventing oxidation and contamination of the steel.
- Applications: Used for high-precision processes like hardening, brazing, and annealing of high-alloy steels and tool steels.
- Advantages: Superior surface finish, reduced oxidation, and precise temperature control.
- Limitations: High cost, complex operation, and slower processing times.
-
Atmosphere-Controlled Furnaces:
- Description: These furnaces use controlled atmospheres (e.g., nitrogen, hydrogen, or argon) to prevent oxidation and decarburization of steel.
- Applications: Essential for processes like carburizing, nitriding, and annealing of high-quality steels.
- Advantages: Enhanced material properties, improved surface quality, and reduced scaling.
- Limitations: Requires specialized equipment and gases, higher operational costs.
-
Induction Furnaces:
- Description: Induction furnaces use electromagnetic induction to heat steel rapidly and uniformly.
- Applications: Suitable for localized heat treatment, hardening, and tempering of specific areas of steel parts.
- Advantages: Fast heating, energy efficiency, and precise control over the heated area.
- Limitations: Limited to specific geometries, and not suitable for large or complex parts.
-
Salt Bath Furnaces:
- Description: These furnaces use molten salts as the heating medium, providing rapid and uniform heating.
- Applications: Used for processes like hardening, tempering, and annealing, especially for tool steels.
- Advantages: Fast heating rates, excellent temperature uniformity, and reduced oxidation.
- Limitations: Requires careful handling of molten salts, and limited to smaller parts.
In summary, the selection of a furnace for heat treating steels depends on the specific requirements of the process, the type of steel, and the scale of production. Each type of furnace offers unique advantages and limitations, making it crucial to choose the right one to achieve the desired material properties efficiently and cost-effectively.
Summary Table:
Furnace Type | Applications | Advantages | Limitations |
---|---|---|---|
Box Furnaces | Annealing, normalizing, tempering | Uniform heating, ease of operation | Limited to batch processing |
Continuous Furnaces | High-volume annealing, hardening | High throughput, consistent quality | Higher initial investment |
Pit Furnaces | Annealing, hardening of large parts | Efficient for heavy components | Limited to specific shapes, slower heating |
Vacuum Furnaces | Hardening, brazing, annealing | Superior finish, reduced oxidation | High cost, complex operation |
Atmosphere-Controlled | Carburizing, nitriding, annealing | Enhanced material properties | Higher operational costs |
Induction Furnaces | Localized hardening, tempering | Fast heating, energy efficient | Limited to specific geometries |
Salt Bath Furnaces | Hardening, tempering, annealing | Fast heating, excellent uniformity | Limited to smaller parts |
Need help choosing the right furnace for your steel heat treatment? Contact our experts today!