Brazing is a metal-joining process that relies on the use of a filler metal with a melting point above 840°F (450°C) but below the melting point of the base metals being joined. The brazing atmosphere plays a critical role in ensuring the quality of the joint, as certain gases can interfere with the process, leading to defects such as oxidation, porosity, or poor wetting. The most undesirable gas in a brazing atmosphere is oxygen, as it promotes oxidation of the metal surfaces and filler material, which can prevent proper bonding. Other gases, such as hydrogen and nitrogen, can also be problematic depending on the specific materials and brazing conditions. Understanding the role of these gases and how to control the atmosphere is essential for achieving strong, reliable brazed joints.
Key Points Explained:
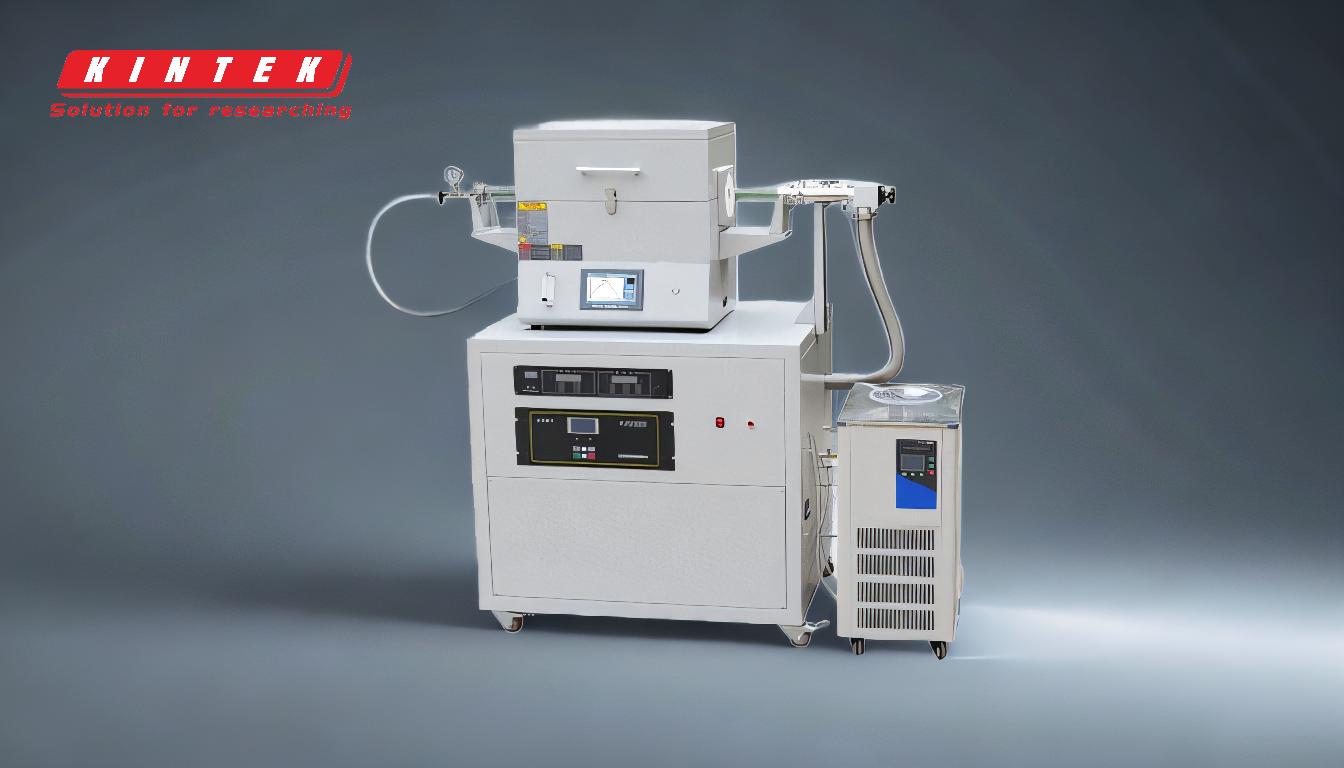
-
Oxygen is the most undesirable gas in a brazing atmosphere:
- Oxygen reacts with metal surfaces and the filler material, forming oxides that prevent proper wetting and bonding.
- Oxides can also lead to porosity and weak joints, as they create barriers between the base metal and the filler material.
- To mitigate oxygen's effects, brazing is often performed in a controlled atmosphere, such as a vacuum or an inert gas environment (e.g., argon or helium).
-
Hydrogen can be problematic in certain brazing applications:
- While hydrogen is often used as a reducing gas to remove oxides, it can also cause embrittlement in some metals, particularly those containing copper or nickel.
- Hydrogen embrittlement can lead to cracking or failure of the brazed joint over time.
- Careful selection of brazing conditions and materials is necessary when using hydrogen to avoid these issues.
-
Nitrogen may interfere with brazing in specific scenarios:
- Nitrogen is generally inert and safe for most brazing processes, but it can react with certain metals (e.g., titanium or zirconium) at high temperatures, forming nitrides that degrade joint quality.
- In applications involving reactive metals, nitrogen should be avoided or carefully controlled.
-
Moisture and other contaminants are also undesirable:
- Water vapor (moisture) in the brazing atmosphere can contribute to oxidation and hydrogen embrittlement.
- Contaminants such as hydrocarbons or sulfur compounds can react with the metals or filler material, leading to defects.
- Proper cleaning of parts and use of high-purity gases are essential to minimize these risks.
-
Controlled atmospheres are critical for successful brazing:
- Common methods for controlling the brazing atmosphere include vacuum brazing, inert gas shielding, and the use of flux to prevent oxidation.
- The choice of atmosphere depends on the materials being joined, the filler metal, and the specific requirements of the application.
By understanding the effects of different gases and maintaining a controlled brazing atmosphere, manufacturers can ensure high-quality, defect-free joints. Proper material selection, cleaning, and process control are key to achieving optimal results in brazing operations.
Summary Table:
Gas | Impact on Brazing | Mitigation Strategies |
---|---|---|
Oxygen | Promotes oxidation, leading to poor wetting, porosity, and weak joints. | Use vacuum or inert gases (e.g., argon, helium) to eliminate oxygen. |
Hydrogen | Can cause embrittlement in metals like copper or nickel, leading to cracking. | Avoid hydrogen in sensitive materials or carefully control brazing conditions. |
Nitrogen | Forms nitrides with reactive metals (e.g., titanium, zirconium), degrading joint quality. | Avoid nitrogen or use it cautiously in reactive metal applications. |
Moisture | Contributes to oxidation and hydrogen embrittlement. | Use high-purity gases and ensure parts are clean and dry before brazing. |
Contaminants | Hydrocarbons or sulfur compounds can react with metals, causing defects. | Clean parts thoroughly and use controlled atmospheres to minimize contamination. |
Ensure your brazing process achieves optimal results—contact our experts today for tailored solutions!