Sintering is a critical process in powder metallurgy where metal powders are heated to temperatures below their melting point, causing particles to bond and form a coherent shape. This process involves several physical and chemical changes, including the removal of water, organic matter, and adsorbed gases, as well as stress relief, reduction of surface oxides, material migration, recrystallization, and grain growth. These changes lead to improved material properties such as reduced porosity, enhanced strength, durability, conductivity, and corrosion resistance. Sintering also allows for greater control over the manufacturing process, resulting in more consistent products while being energy-efficient and environmentally friendly.
Key Points Explained:
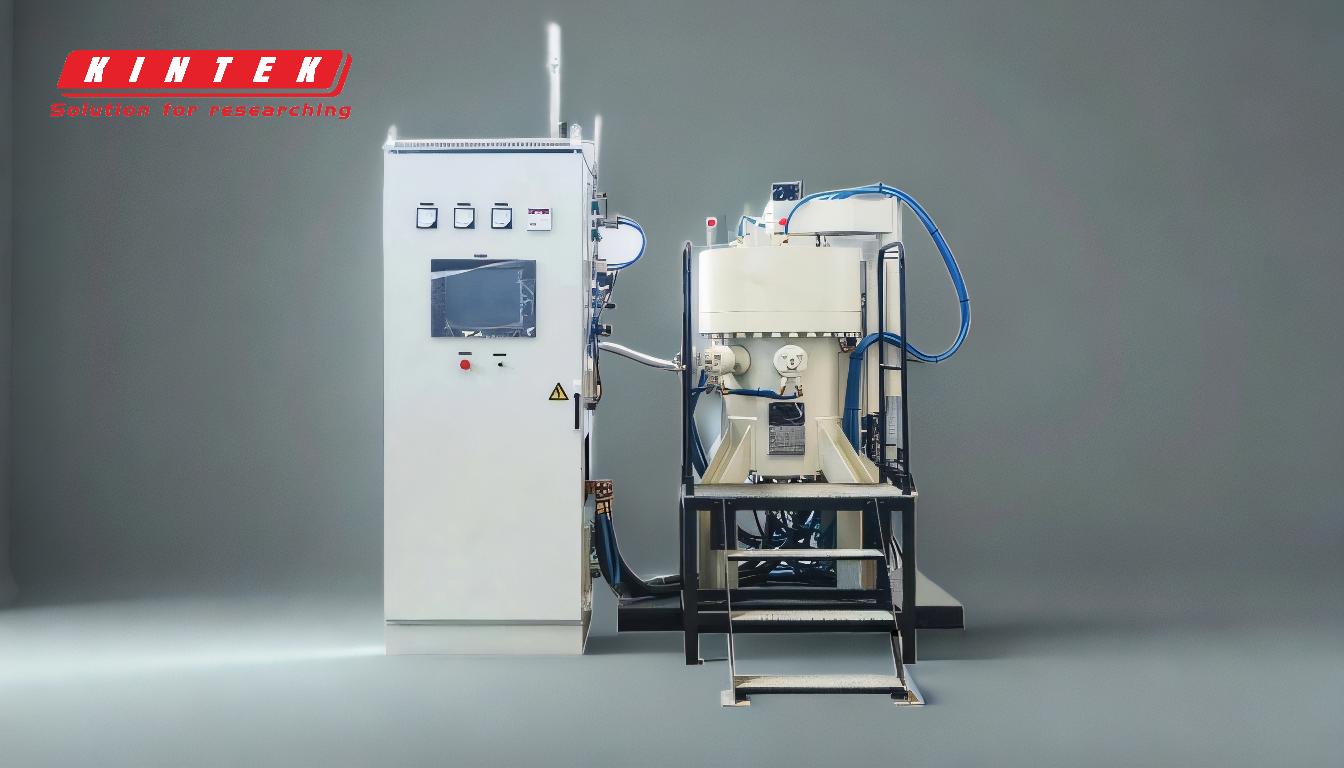
-
Bonding of Particles:
- During sintering, metal powder particles are heated to a temperature below their melting point, causing them to bond chemically. This bonding forms a coherent shape, which is essential for creating solid metal parts from powders.
- The process is driven by the reduction of surface energy, which encourages particles to coalesce and form stronger bonds.
-
Physical and Chemical Changes:
- Evaporation of Water and Organic Matter: Any moisture or organic substances present in the powder are evaporated or burned off during the initial stages of sintering.
- Removal of Adsorbed Gases: Gases adsorbed on the surface of the powder particles are released, which helps in achieving a denser material.
- Stress Relief: Internal stresses within the powder particles are relieved, leading to a more stable and uniform structure.
- Reduction of Surface Oxides: Surface oxides on the powder particles are reduced, which improves the bonding between particles.
- Material Migration: Atoms migrate across particle boundaries, leading to densification and the formation of a solid structure.
- Recrystallization and Grain Growth: New grains form and grow, which can significantly alter the microstructure and properties of the material.
-
Microstructural Changes:
- Grain Size and Shape: The sintering process affects the size and shape of grains within the material. Larger grains can form, which may influence the mechanical properties.
- Pore Size and Distribution: Porosity is reduced as pores diminish or close up, leading to a higher-density material. This reduction in porosity enhances properties such as strength, conductivity, and corrosion resistance.
- Grain Boundary Shape and Distribution: The shape and distribution of grain boundaries are altered, which can affect the material's mechanical and thermal properties.
-
Improvement in Material Properties:
- Strength and Durability: By minimizing porosity, sintering enhances the strength and durability of the material. The reduced porosity also leads to better mechanical properties.
- Conductivity and Corrosion Resistance: The reduction in surface porosity improves electrical conductivity and resistance to corrosion.
- Tensile Strength: The material's tensile strength is improved due to the densification and bonding of particles.
-
Environmental and Manufacturing Advantages:
- Energy Efficiency: Sintering requires less energy compared to melting the same metal, making it a more environmentally friendly option.
- Process Control: The sintering process allows for greater control over the manufacturing process, resulting in more consistent and reliable products.
-
Coalescence and Reversion:
- Under certain external conditions, metal powder particles may exhibit coalescence, where they temporarily merge. However, once these conditions are removed, the particles return to their normal behavior, maintaining the integrity of the sintered material.
In summary, sintering transforms metal powders into solid, durable materials with enhanced properties through a series of physical and chemical changes. This process is not only efficient and controllable but also environmentally friendly, making it a preferred method in powder metallurgy.
Summary Table:
Key Aspect | Description |
---|---|
Bonding of Particles | Metal powders bond chemically below melting point, forming a solid structure. |
Physical & Chemical Changes | Evaporates water, removes gases, reduces oxides, and migrates material. |
Microstructural Changes | Reduces porosity, alters grain size, and improves grain boundary distribution. |
Material Property Improvement | Enhances strength, durability, conductivity, and corrosion resistance. |
Environmental Benefits | Energy-efficient and allows precise control over manufacturing processes. |
Learn how sintering can optimize your manufacturing process—contact our experts today!