A diffusion furnace is a specialized type of furnace used in semiconductor manufacturing and other high-temperature processes. It is designed to operate at sustained high temperatures under moderate vacuum conditions, making it ideal for processes like thermal oxide growth, doping, and dopant diffusion. These furnaces are typically large to accommodate a significant quantity of substrates, ensuring uniform treatment across all materials. The furnace's design includes components such as heating elements, temperature control systems, and vacuum systems, which work together to maintain precise conditions for diffusion processes. Diffusion furnaces are critical in producing high-quality semiconductor devices, as they ensure consistent and controlled diffusion of dopants into silicon wafers.
Key Points Explained:
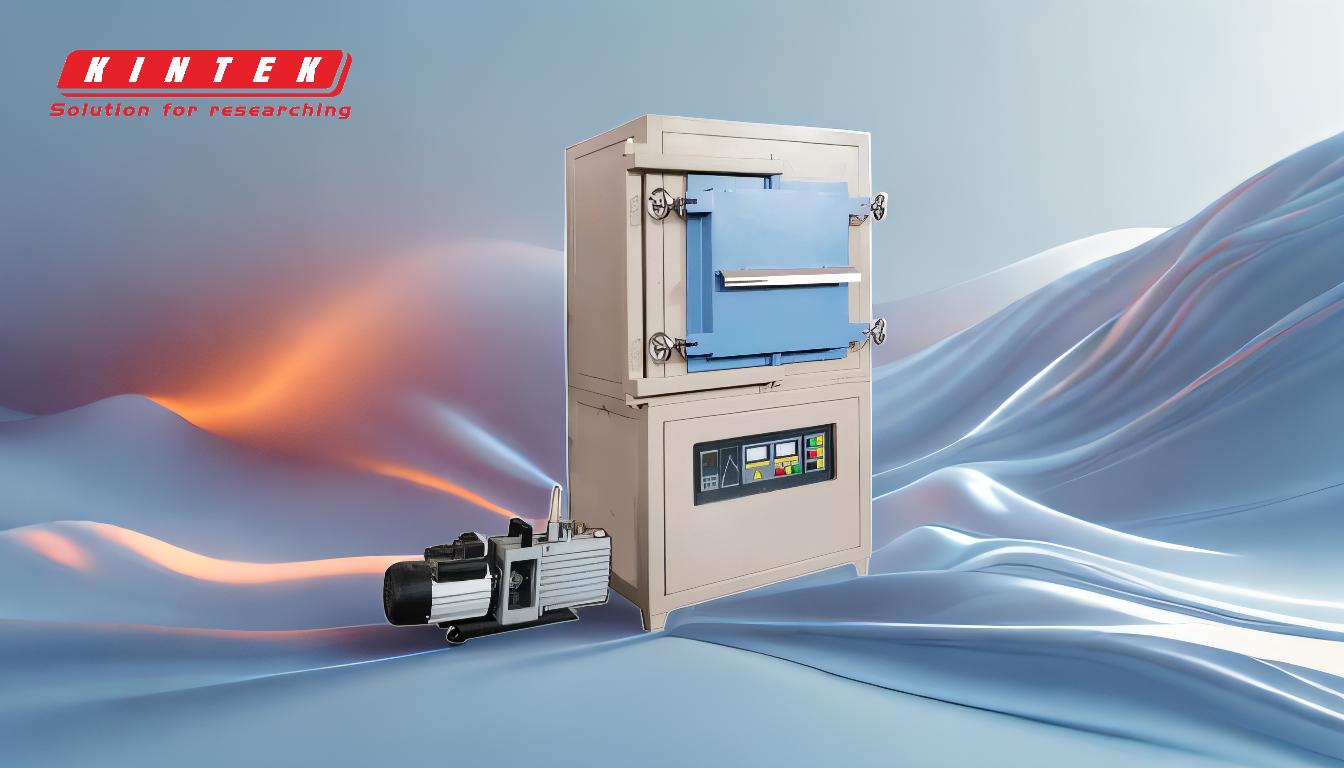
-
Purpose and Applications:
- Diffusion furnaces are primarily used in semiconductor manufacturing for processes such as thermal oxide growth, doping, and dopant diffusion.
- These processes require sustained high temperatures and moderate vacuum conditions to ensure precise and uniform treatment of substrates.
-
Key Components:
- Heating Elements: Generate the high temperatures needed for diffusion processes. These elements are typically made of materials that can withstand extreme heat, such as resistance wires or ceramics.
- Temperature Control System: Monitors and regulates the temperature within the furnace to ensure consistency and precision, which is crucial for the success of diffusion processes.
- Vacuum System: Creates and maintains a moderate vacuum environment within the furnace, which is essential for processes like dopant diffusion.
- Furnace Chamber: The insulated chamber where the substrates are placed. It is designed to maintain high temperatures and vacuum conditions.
- Control System: Manages various parameters such as temperature, vacuum level, and process timing to ensure optimal conditions for diffusion.
-
Design and Size:
- Diffusion furnaces are typically large to accommodate a large quantity of substrates. This design ensures that all substrates are treated uniformly, which is critical for producing high-quality semiconductor devices.
- The large size also allows for batch processing, increasing efficiency and throughput in semiconductor manufacturing.
-
Operational Conditions:
- High Temperatures: Diffusion furnaces operate at sustained high temperatures, often exceeding 1000°C, to facilitate the diffusion of dopants into silicon wafers.
- Moderate Vacuum: The vacuum environment helps to prevent contamination and ensures that the diffusion process occurs uniformly across all substrates.
-
Importance in Semiconductor Manufacturing:
- Diffusion furnaces play a critical role in the production of semiconductor devices. They ensure that dopants are diffused into silicon wafers in a controlled and consistent manner, which is essential for the electrical properties of the final product.
- The precision and control offered by diffusion furnaces are key to achieving the high performance and reliability required in modern semiconductor devices.
-
Maintenance and Durability:
- Given the extreme conditions under which diffusion furnaces operate, regular maintenance is essential to ensure their longevity and performance.
- Components such as heating elements, vacuum pumps, and insulation materials may need to be inspected, cleaned, or replaced periodically to maintain optimal operation.
In summary, a diffusion furnace is a complex and critical piece of equipment in semiconductor manufacturing, designed to operate under high temperatures and moderate vacuum conditions. Its key components and precise control systems ensure uniform and consistent diffusion processes, which are essential for producing high-quality semiconductor devices. The large size of these furnaces allows for efficient batch processing, further enhancing their utility in industrial applications.
Summary Table:
Key Aspect | Details |
---|---|
Purpose | Used in semiconductor manufacturing for thermal oxide growth, doping, and dopant diffusion. |
Key Components | Heating elements, temperature control system, vacuum system, furnace chamber, control system. |
Design & Size | Large size for uniform substrate treatment and efficient batch processing. |
Operational Conditions | Sustained high temperatures (>1000°C) and moderate vacuum environments. |
Importance | Ensures controlled and consistent diffusion for high-quality semiconductor devices. |
Maintenance | Regular inspection and replacement of components like heating elements and vacuum pumps. |
Discover how a diffusion furnace can optimize your semiconductor processes—contact us today!