A furnace reline refers to the process of reconditioning a blast furnace to restore its operational efficiency and extend its lifespan. This process involves replacing or refurbishing critical components of the furnace that have deteriorated over time due to high temperatures, chemical reactions, and mechanical stress. While the primary goal is to restore functionality, a reline may also include limited modifications or modernizations to adapt the furnace to new operational requirements or technological advancements. However, due to spatial constraints and the complexity of the furnace structure, significant modifications are often restricted during a reline.
Key Points Explained:
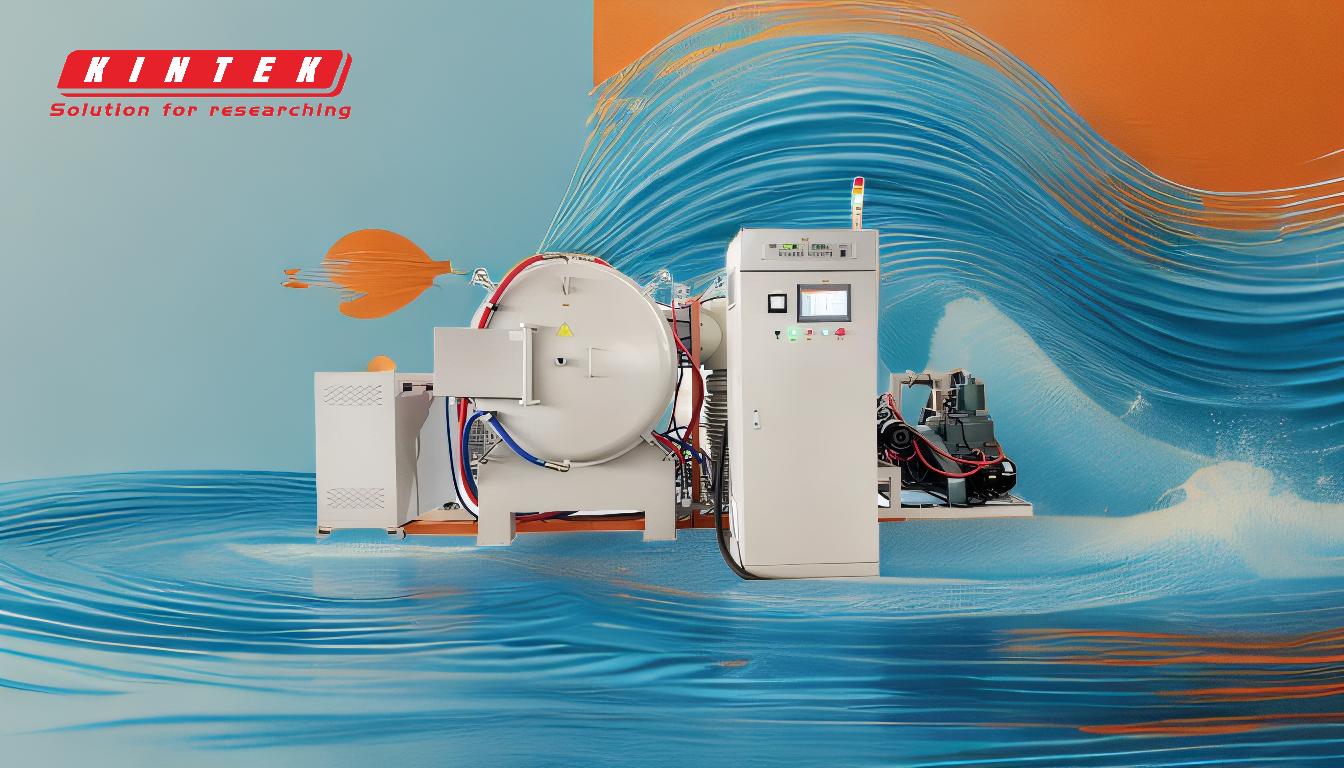
-
Definition of a Furnace Reline:
- A furnace reline is a maintenance procedure aimed at reconditioning a blast furnace.
- It involves replacing or refurbishing worn-out or damaged components to restore the furnace's operational efficiency.
-
Purpose of a Furnace Reline:
- Restoration of Functionality: Over time, the internal lining of the furnace, known as the refractory lining, degrades due to exposure to extreme heat, chemical reactions, and mechanical wear. A reline replaces this lining to ensure the furnace can operate at optimal levels.
- Extending Lifespan: By addressing wear and tear, a reline helps prolong the operational life of the furnace, delaying the need for a complete replacement.
- Limited Modernization: While the primary focus is on restoration, a reline may also include minor upgrades or modifications to improve efficiency or adapt to new operational requirements.
-
Components Involved in a Furnace Reline:
- Refractory Lining: The most critical component replaced during a reline. This lining protects the furnace structure from extreme temperatures and chemical corrosion.
- Tuyeres and Bosh Plates: These components, which are involved in the injection of air and the containment of molten materials, may also be replaced or refurbished.
- Cooling Systems: The cooling elements, which prevent overheating of the furnace shell, may be inspected and replaced if necessary.
-
Challenges and Constraints:
- Spatial Limitations: The existing structure of the furnace and surrounding plant may limit the extent of modifications that can be made during a reline.
- Time Constraints: A reline is typically a time-sensitive operation, as prolonged downtime can significantly impact production.
- Cost Considerations: While a reline is less expensive than building a new furnace, it still involves significant costs, including materials, labor, and lost production time.
-
Process of a Furnace Reline:
- Planning and Assessment: The first step involves a thorough inspection of the furnace to identify areas that need repair or replacement. This assessment helps in planning the scope of the reline.
- Shutdown and Cooling: The furnace is shut down and allowed to cool to a safe temperature before any work begins.
- Demolition and Removal: The old refractory lining and other worn-out components are removed.
- Installation of New Components: New refractory materials and other components are installed according to the design specifications.
- Testing and Commissioning: After the reline, the furnace is tested to ensure it operates correctly before being brought back into full production.
-
Benefits of a Furnace Reline:
- Cost-Effectiveness: Compared to building a new furnace, a reline is a more economical way to maintain production capacity.
- Improved Efficiency: A well-executed reline can improve the furnace's thermal efficiency and reduce energy consumption.
- Reduced Downtime: While a reline does require downtime, it is typically shorter than the time required to construct a new furnace.
-
Considerations for Purchasers:
- Quality of Materials: The longevity and performance of the reline depend heavily on the quality of the refractory materials and other components used.
- Expertise of Contractors: The success of a reline project also depends on the expertise of the contractors performing the work. Experienced contractors are more likely to deliver a high-quality reline.
- Future-Proofing: Purchasers should consider whether the reline includes any upgrades that will make the furnace more adaptable to future technological advancements or changes in production requirements.
In summary, a furnace reline is a critical maintenance procedure that restores the functionality of a blast furnace, extends its lifespan, and may include limited modernizations. It involves replacing key components like the refractory lining and cooling systems, and while it presents challenges such as spatial and time constraints, it offers significant benefits in terms of cost-effectiveness and improved efficiency. For purchasers, the quality of materials and the expertise of contractors are crucial factors to consider when planning a furnace reline.
Summary Table:
Aspect | Details |
---|---|
Definition | Reconditioning a blast furnace by replacing or refurbishing critical components. |
Purpose | Restores functionality, extends lifespan, and may include minor upgrades. |
Key Components | Refractory lining, tuyeres, bosh plates, and cooling systems. |
Challenges | Spatial limitations, time constraints, and cost considerations. |
Process | Planning, shutdown, demolition, installation, and testing. |
Benefits | Cost-effectiveness, improved efficiency, and reduced downtime. |
Considerations | Quality of materials, contractor expertise, and future-proofing upgrades. |
Ensure your blast furnace operates at peak efficiency—contact our experts today for a professional furnace reline!