Molding machines are specialized equipment used in the manufacturing and casting industries to create molds and cores from materials like sand, plastic, or metal. These machines utilize tools such as pattern plates and core boxes to shape the required materials into precise workpieces, including mold halves, mold parts, and cores. They are essential in processes like sand molding, where they ensure the production of high-quality, dimensionally accurate molds for casting applications. Molding machines streamline the production process, improve efficiency, and reduce manual labor, making them indispensable in industries like automotive, aerospace, and heavy machinery manufacturing.
Key Points Explained:
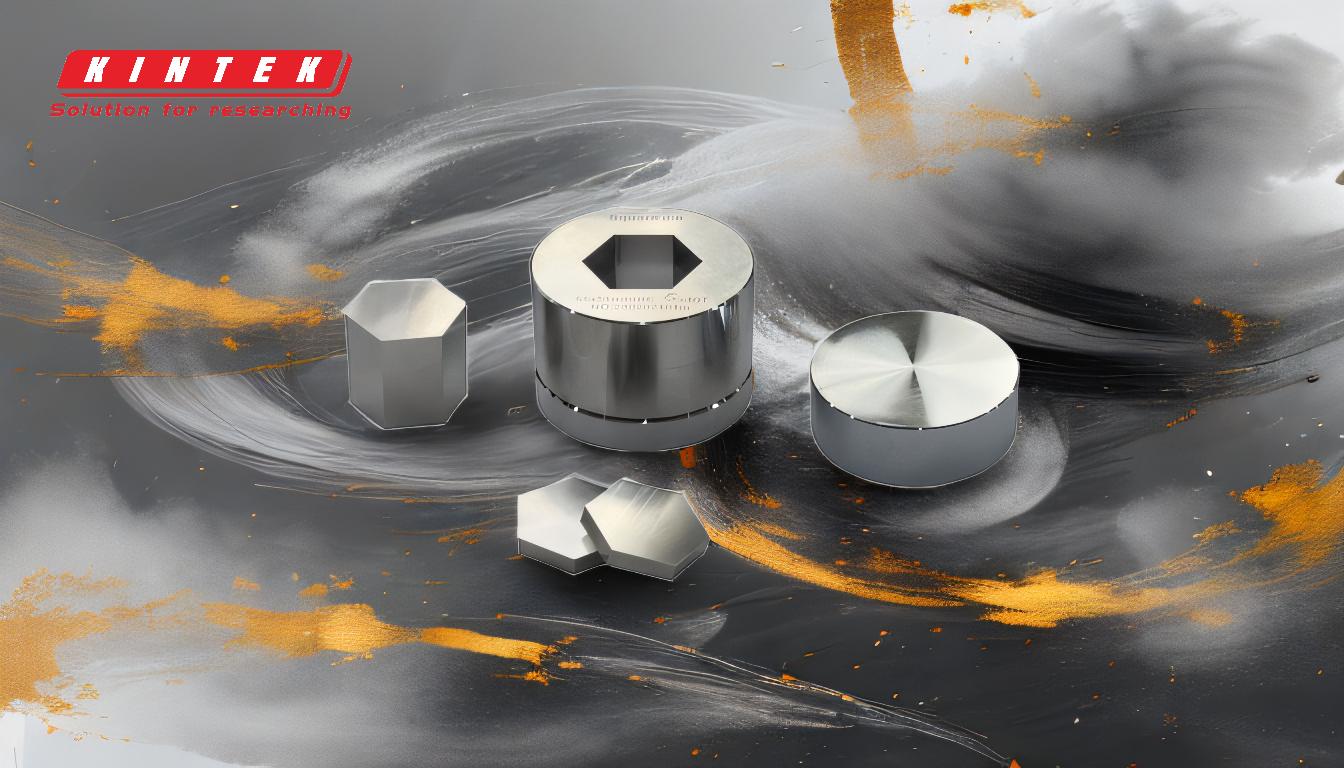
-
Primary Function of Molding Machines:
- Molding machines are designed to produce molds and cores, which are essential components in casting processes. These machines shape materials like sand, plastic, or metal into precise forms using tools such as pattern plates and core boxes.
- Example: In sand molding, the machine compacts sand around a pattern to create a mold cavity for casting metal parts.
-
Types of Workpieces Produced:
- Molding machines create various workpieces, including:
- Mold halves: Two-part molds used to form the outer shape of a cast object.
- Mold parts: Components of a mold that define specific features of the final product.
- Cores: Internal structures that create hollow sections or complex internal geometries in castings.
- Example: In automotive manufacturing, cores are used to create engine block cavities.
- Molding machines create various workpieces, including:
-
Materials Used in Molding:
- Molding machines work with materials like:
- Molding sand: A mixture of sand, clay, and water used in sand casting.
- Core molding materials: Specialized sands or resins used to form cores.
- Plastics or metals: Used in injection molding or die-casting processes.
- Example: Green sand (a mixture of sand, clay, and water) is commonly used in foundries for sand molding.
- Molding machines work with materials like:
-
Tools and Components:
- Key tools used in molding machines include:
- Pattern plates: Templates that define the shape of the mold.
- Core boxes: Containers used to form cores.
- These tools ensure the accuracy and repeatability of the molding process.
- Example: A pattern plate for a gear mold ensures that each gear produced is identical in shape and size.
- Key tools used in molding machines include:
-
Applications in Industry:
- Molding machines are widely used in industries such as:
- Automotive: For casting engine components, transmission parts, and body panels.
- Aerospace: For producing turbine blades and structural components.
- Heavy machinery: For creating large, durable parts like gears and housings.
- Example: In aerospace, molding machines produce lightweight, high-strength components for aircraft engines.
- Molding machines are widely used in industries such as:
-
Advantages of Using Molding Machines:
- Efficiency: Automates the mold-making process, reducing manual labor and production time.
- Precision: Ensures consistent and accurate molds, leading to high-quality castings.
- Versatility: Can handle a wide range of materials and complex geometries.
- Example: A foundry using molding machines can produce hundreds of identical castings with minimal variation.
-
Process Overview:
- The molding process typically involves:
- Preparing the molding material (e.g., mixing sand and binders).
- Placing the pattern plate or core box in the machine.
- Compacting the material around the pattern to form the mold or core.
- Removing the pattern and preparing the mold for casting.
- Example: In sand casting, the mold is baked to harden it before molten metal is poured in.
- The molding process typically involves:
-
Role in Modern Manufacturing:
- Molding machines are critical in modern manufacturing due to their ability to produce complex, high-precision parts at scale. They enable mass production while maintaining quality and reducing costs.
- Example: The automotive industry relies on molding machines to produce millions of engine components annually.
By understanding these key points, a purchaser can evaluate the suitability of molding machines for their specific manufacturing needs, ensuring they select the right equipment for their production goals.
Summary Table:
Aspect | Details |
---|---|
Primary Function | Produce molds and cores for casting processes. |
Workpieces Produced | Mold halves, mold parts, and cores. |
Materials Used | Molding sand, core materials, plastics, and metals. |
Key Tools | Pattern plates and core boxes. |
Applications | Automotive, aerospace, and heavy machinery manufacturing. |
Advantages | Efficiency, precision, versatility, and reduced manual labor. |
Process Overview | Prepare material, shape with tools, and prepare molds for casting. |
Role in Manufacturing | Enables mass production of high-precision parts at scale. |
Ready to enhance your manufacturing process? Contact us today to find the perfect press mold or isostatic molding solution for your needs!