A vacuum system in sputtering is a critical component that creates and maintains a low-pressure environment within a vacuum chamber. This environment is essential for the sputtering process, a Physical Vapor Deposition (PVD) technique used to deposit thin films onto substrates. The vacuum system ensures that the deposition process is free from contamination, allows sputtered atoms to travel unimpeded from the target to the substrate, and facilitates the formation of plasma. By controlling the pressure, the vacuum system enables precise and repeatable deposition, ensuring high-quality, uniform, and contamination-free thin films.
Key Points Explained:
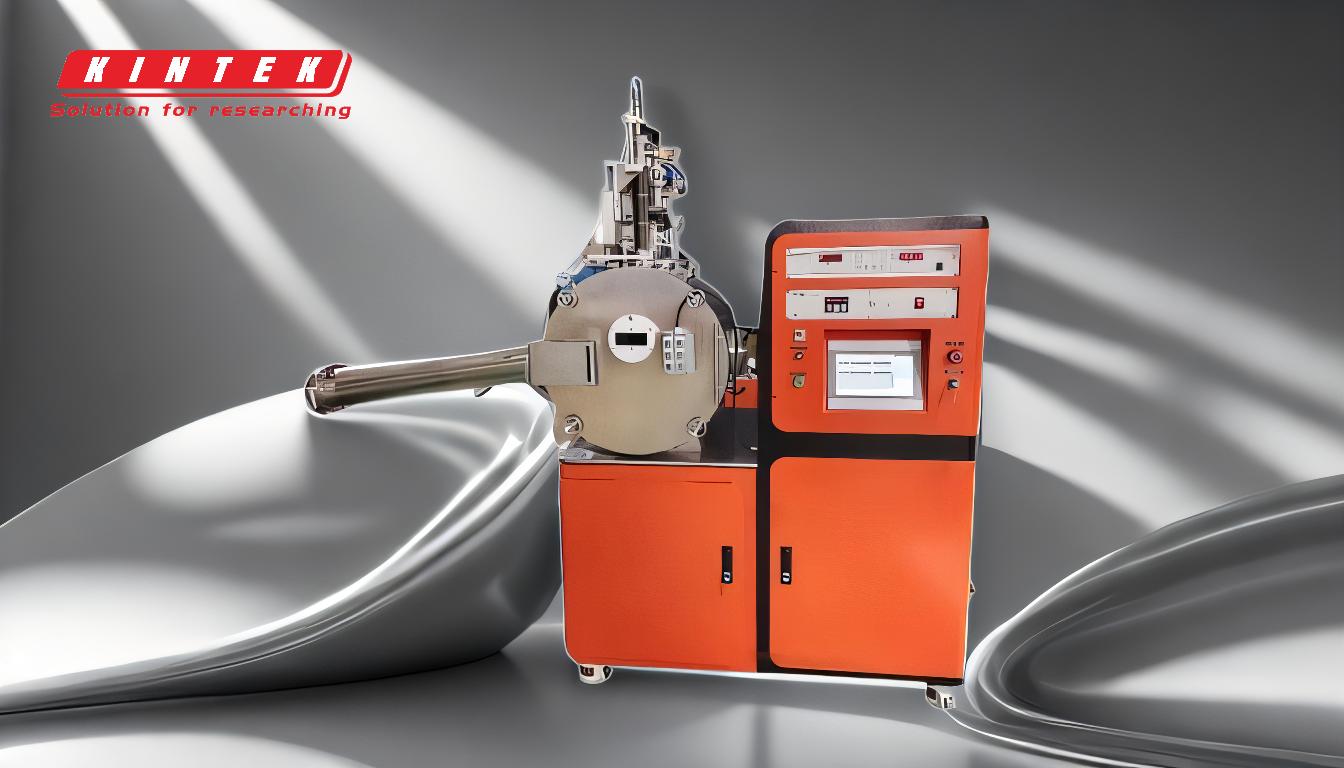
-
Purpose of a Vacuum System in Sputtering:
- The vacuum system creates a low-pressure environment in the chamber, which is necessary for the sputtering process to occur effectively.
- It ensures that the material being deposited is not slowed down by air or other gases, allowing it to reach the substrate with sufficient energy for strong adhesion.
- A vacuum minimizes contamination from external particles, ensuring the purity and quality of the deposited film.
-
Role of Vacuum in Plasma Formation:
- Sputtering relies on the formation of plasma, which is a gas of ionized atoms and electrons.
- The vacuum system maintains the optimal pressure range for plasma formation. At too low pressures, there are insufficient collisions to sustain plasma, while at too high pressures, excessive collisions prevent electrons from gaining enough energy to ionize atoms effectively.
-
Preventing Contamination:
- A vacuum environment ensures that the sputtering process remains sterile and free from impurities.
- Contaminants such as dust, moisture, or residual gases can compromise the quality of the thin film, leading to defects like rough surfaces, target arcing, or film failure.
- Maintaining a clean vacuum chamber and sputtering system is crucial to avoid these issues.
-
Lengthening the Mean Free Path:
- The mean free path is the average distance a particle can travel before colliding with another particle.
- In a vacuum, the mean free path of sputtered atoms is significantly lengthened, allowing them to travel from the target to the substrate without interference.
- This results in a more uniform and smoother deposition of the thin film.
-
Controlled and Repeatable Deposition:
- The vacuum system provides a controlled environment, enabling precise regulation of the sputtering process.
- By maintaining consistent pressure levels, the system ensures repeatable results, which is critical for industrial applications requiring high-quality thin films.
-
Components of a Vacuum System:
- Vacuum Pump: Removes air and other gases from the chamber to achieve the desired low-pressure environment.
- Vacuum Chamber: Houses the sputtering process and maintains the vacuum environment.
- Pressure Gauges and Controllers: Monitor and regulate the pressure within the chamber to ensure optimal conditions for sputtering.
- Inert Gas Supply: Introduces inert gases like argon into the chamber to facilitate plasma formation and material transfer.
-
Importance of Cleanliness:
- Any residue, such as lubricating oil, dust, or pre-coating materials, can accumulate moisture and contaminants, increasing the risk of film failure.
- Regular cleaning of the vacuum chamber, sputter guns, and targets is essential to prevent short circuits, target arcing, and surface defects.
-
Applications of Sputtering in Vacuum:
- Sputtering is widely used in industries such as semiconductor manufacturing, optics, and decorative coatings.
- The vacuum system ensures that the deposited films meet the stringent purity and quality requirements of these applications.
In summary, a vacuum system is indispensable in sputtering, as it provides the controlled, low-pressure environment necessary for efficient material transfer, plasma formation, and contamination-free deposition. By maintaining the vacuum at specific levels and ensuring system cleanliness, high-quality thin films with uniform properties can be reliably produced.
Summary Table:
Key Aspect | Description |
---|---|
Purpose | Creates a low-pressure environment for effective sputtering and material transfer. |
Plasma Formation | Maintains optimal pressure for stable plasma, essential for ionizing atoms. |
Contamination Prevention | Ensures a sterile environment, minimizing impurities like dust and moisture. |
Mean Free Path | Lengthens particle travel distance, ensuring uniform and smooth film deposition. |
Controlled Deposition | Enables precise and repeatable results for high-quality thin films. |
Components | Includes vacuum pump, chamber, pressure gauges, and inert gas supply. |
Cleanliness Importance | Regular cleaning prevents defects like target arcing and film failure. |
Applications | Used in semiconductor manufacturing, optics, and decorative coatings. |
Discover how a vacuum system can optimize your sputtering process—contact our experts today!