A vertical diffusion furnace is a specialized piece of equipment used primarily in semiconductor manufacturing and material science. It is designed to perform diffusion processes, which involve altering the composition of materials, such as silicon wafers, by introducing impurities or dopants from the vapor phase. This process is critical for creating specific electrical properties in semiconductor devices. Vertical diffusion furnaces are characterized by their vertical orientation, which allows for uniform temperature distribution and efficient gas flow, ensuring precise and consistent results. These furnaces are essential for processes like annealing, doping, and oxidation, which are fundamental to the production of integrated circuits and other electronic components.
Key Points Explained:
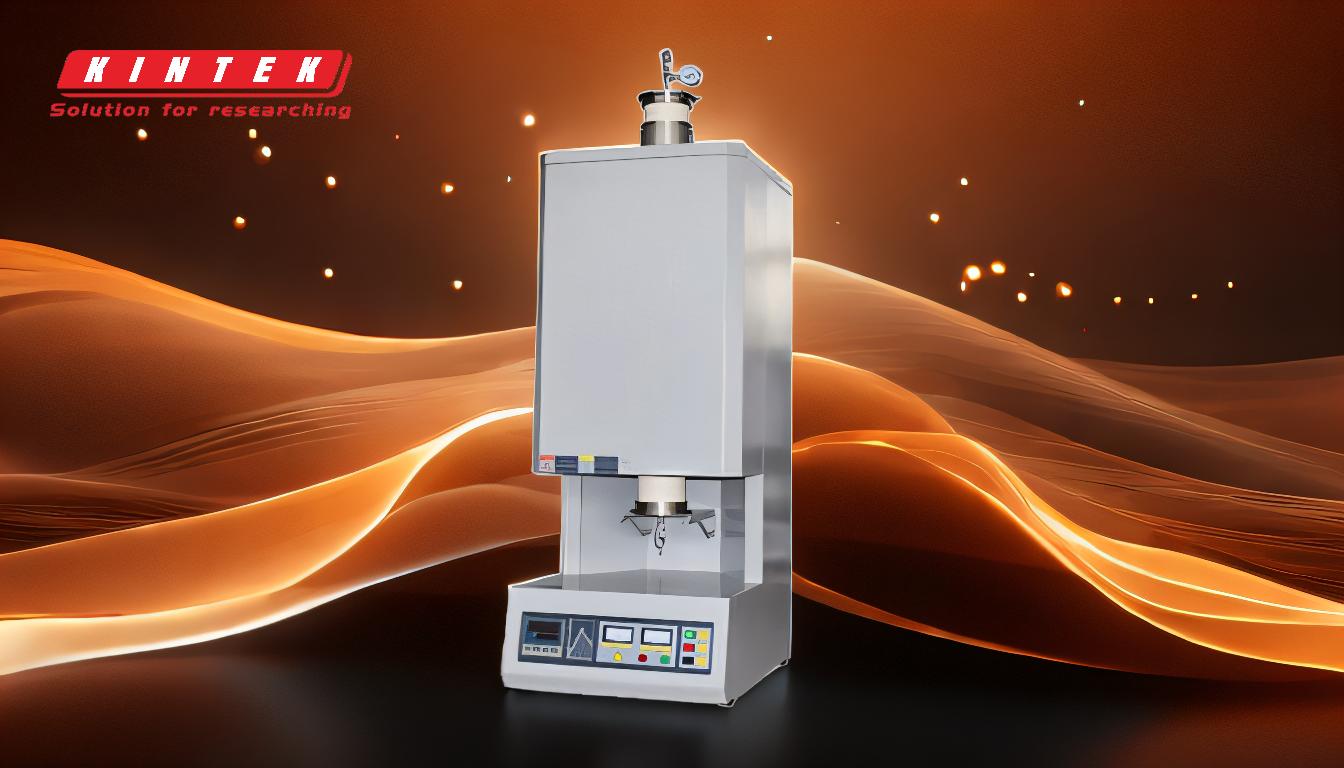
-
Definition and Purpose:
- A vertical diffusion furnace is a type of furnace used primarily in the semiconductor industry to perform diffusion processes.
- The primary purpose is to alter the composition of materials, such as silicon wafers, by introducing impurities or dopants from the vapor phase.
- This process is crucial for creating specific electrical properties in semiconductor devices, such as transistors and diodes.
-
Key Processes:
- Diffusion: The core process involves diffusing atoms from the vapor phase into the material that needs to be modified. This is typically used to electrically activate impurities introduced by ion implantation.
- Annealing: A heat treatment process that alters the physical and sometimes chemical properties of a material to increase its ductility and reduce its hardness, making it more workable.
- Oxidation: A process used to grow a thin layer of oxide on the surface of silicon wafers, which is essential for creating insulating layers in semiconductor devices.
-
Design and Features:
- Vertical Orientation: The vertical design allows for uniform temperature distribution and efficient gas flow, which are critical for achieving consistent results.
- Temperature Control: Advanced temperature control systems, often with multiple heating zones, ensure precise control over the thermal environment.
- Gas Handling: The furnace is equipped with systems to handle various gases, including dopant gases, inert gases, and reactive gases, which are essential for different diffusion processes.
-
Applications:
- Semiconductor Manufacturing: Used extensively in the production of integrated circuits, where precise control over material properties is essential.
- Material Science: Employed in research and development to study and develop new materials with specific electrical and thermal properties.
- Advanced Ceramics: Used in the processing of advanced ceramics, where controlled diffusion processes are necessary to achieve desired material properties.
-
Advantages:
- Uniformity: The vertical design ensures uniform temperature distribution, leading to consistent results across the entire batch of materials being processed.
- Efficiency: Efficient gas flow and temperature control systems reduce processing time and energy consumption.
- Precision: Advanced control systems allow for precise control over the diffusion process, ensuring that the desired material properties are achieved.
-
Comparison with Other Furnaces:
- Horizontal Furnaces: While horizontal furnaces are also used for similar processes, vertical furnaces offer better uniformity and efficiency, especially for large-scale production.
- Vacuum Furnaces: Unlike vacuum furnaces, which are used for processes requiring a controlled, non-oxidizing atmosphere, vertical diffusion furnaces are designed specifically for diffusion processes in a controlled gas environment.
-
Technological Advancements:
- Automation: Modern vertical diffusion furnaces are often equipped with automated systems for loading and unloading wafers, reducing human error and increasing throughput.
- Advanced Materials: The use of advanced materials in the construction of the furnace, such as polycrystalline alumina fiber, improves thermal efficiency and durability.
- Control Systems: Advanced control systems, including multi-segment program temperature control and phase shift trigger systems, allow for precise and repeatable processes.
In summary, a vertical diffusion furnace is an essential tool in the semiconductor industry, enabling precise control over material properties through diffusion processes. Its vertical design, advanced temperature and gas control systems, and automation capabilities make it a critical component in the production of modern electronic devices.
Summary Table:
Aspect | Details |
---|---|
Primary Use | Semiconductor manufacturing, material science, advanced ceramics |
Key Processes | Diffusion, annealing, oxidation |
Design Features | Vertical orientation, advanced temperature control, efficient gas handling |
Advantages | Uniform temperature distribution, efficiency, precision |
Applications | Integrated circuits, material research, advanced ceramics |
Technological Advancements | Automation, advanced materials, multi-segment temperature control |
Learn how a vertical diffusion furnace can optimize your semiconductor processes—contact us today!