A muffle furnace, a specialized heating device used in laboratories and industrial settings, is known by several alternative names depending on its design, functionality, or historical context. These names include electric furnace, resistance furnace, box furnace, and retort furnace (in historical usage). The term "muffle furnace" itself refers to its unique design, which isolates the material being heated from direct contact with combustion gases and ash. This separation ensures a clean and controlled heating environment, making it ideal for processes like ashing, annealing, and heat treatment. Understanding these alternative names helps in identifying the right equipment for specific applications.
Key Points Explained:
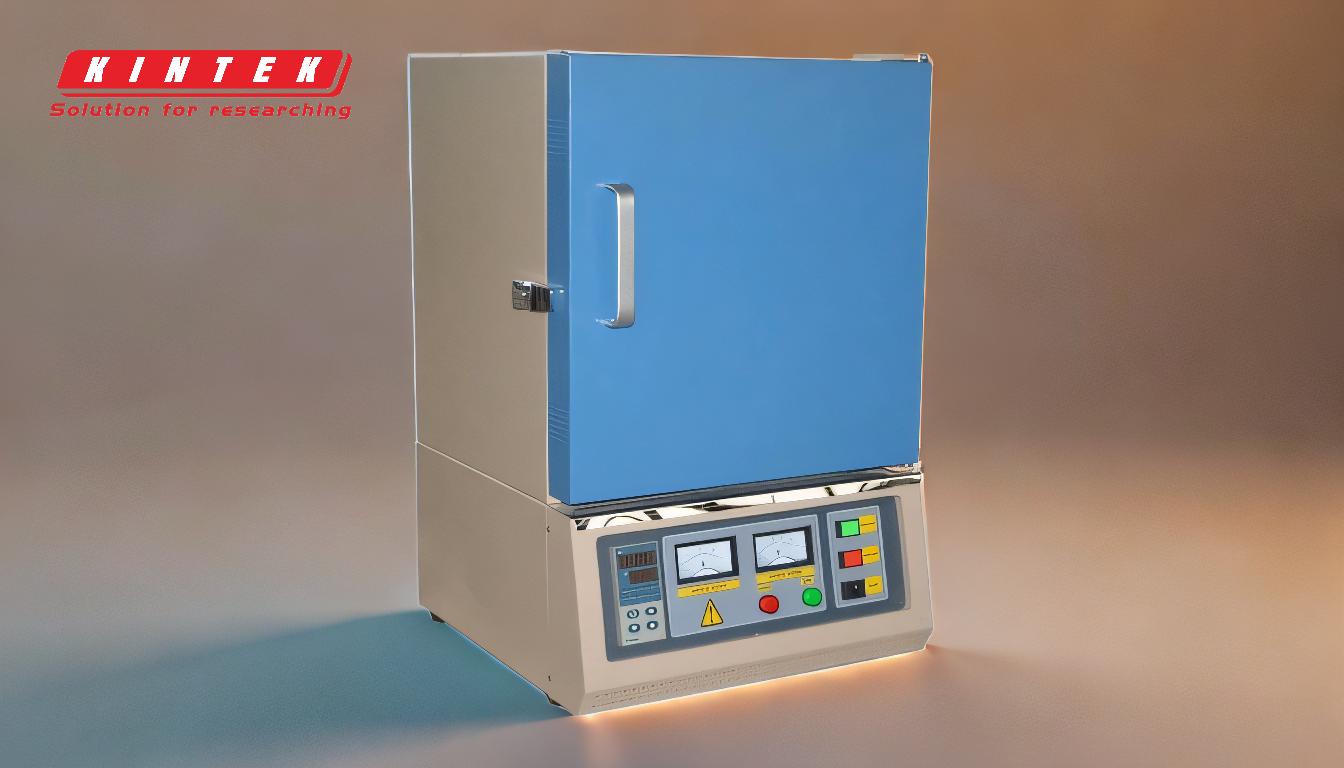
-
Electric Furnace:
- A muffle furnace is often called an electric furnace because it typically uses electric heating elements to generate heat. This distinguishes it from furnaces that rely on combustion of fuels like gas or oil.
- Electric furnaces are preferred in laboratory settings for their precise temperature control and clean operation, as they do not produce combustion byproducts.
-
Resistance Furnace:
- The term "resistance furnace" highlights the use of electrical resistance heating elements, which convert electrical energy into heat. These elements are often made of materials like nichrome or silicon carbide, which can withstand high temperatures.
- This name emphasizes the technical mechanism of heat generation, making it a useful descriptor for engineers and technicians.
-
Box Furnace:
- A muffle furnace is sometimes referred to as a box furnace due to its rectangular or box-like design. This design provides a uniform heating environment, making it suitable for batch processing of materials.
- The term "box furnace" is often used interchangeably with "muffle furnace" in industrial and laboratory contexts, especially when the furnace is used for general-purpose heating.
-
Retort Furnace (Historical Usage):
- Historically, muffle furnaces were called retort furnaces. The term "retort" refers to a vessel used for distillation or decomposition of substances, often in a sealed environment.
- While this term is less common today, it reflects the historical evolution of furnace technology and its applications in chemical processes.
-
General Heating Device:
- The muffle furnace is recognized as a general-purpose heating device, capable of performing a wide range of thermal processes such as ashing, calcination, and sintering.
- Its versatility and ability to maintain a clean heating environment make it a staple in laboratories and industrial settings.
-
Laboratory Furnace Types:
- Muffle furnaces are one of the three most common types of laboratory furnaces, alongside tube furnaces and box furnaces. Each type has specific applications, with muffle furnaces being particularly suited for processes requiring isolation from combustion byproducts.
- Other specialized furnaces, such as ashing furnaces and melting furnaces, may also incorporate muffle furnace principles for specific applications.
By understanding these alternative names and their contexts, purchasers and users can better identify the right equipment for their needs, ensuring optimal performance and results in their heating processes.
Summary Table:
Alternative Name | Key Features | Common Applications |
---|---|---|
Electric Furnace | Uses electric heating elements; precise temperature control; clean operation. | Laboratory settings, ashing, annealing. |
Resistance Furnace | Relies on electrical resistance heating elements; high-temperature materials. | Engineering, technical processes requiring high heat. |
Box Furnace | Rectangular design; uniform heating environment; batch processing. | Industrial and laboratory general-purpose heating. |
Retort Furnace (Historical) | Historical term; used for sealed distillation or decomposition processes. | Chemical processes, historical applications. |
Need help choosing the right furnace for your needs? Contact our experts today for personalized guidance!