Chemical Vapor Deposition (CVD) is a sophisticated chemical process used to produce high-purity, high-performance solid materials. It involves the reaction or decomposition of gas molecules on a heated substrate within a reaction chamber, resulting in the formation of a thin film on the substrate's surface. This method is widely utilized across various industries, including electronics, where it deposits thin films on semiconductors, and manufacturing, where it enhances the durability of cutting tools and creates thin-film solar cells. The process requires a high level of expertise and is conducted under specific conditions, such as high temperatures and sometimes in a vacuum, to ensure the quality and integrity of the deposited materials.
Key Points Explained:
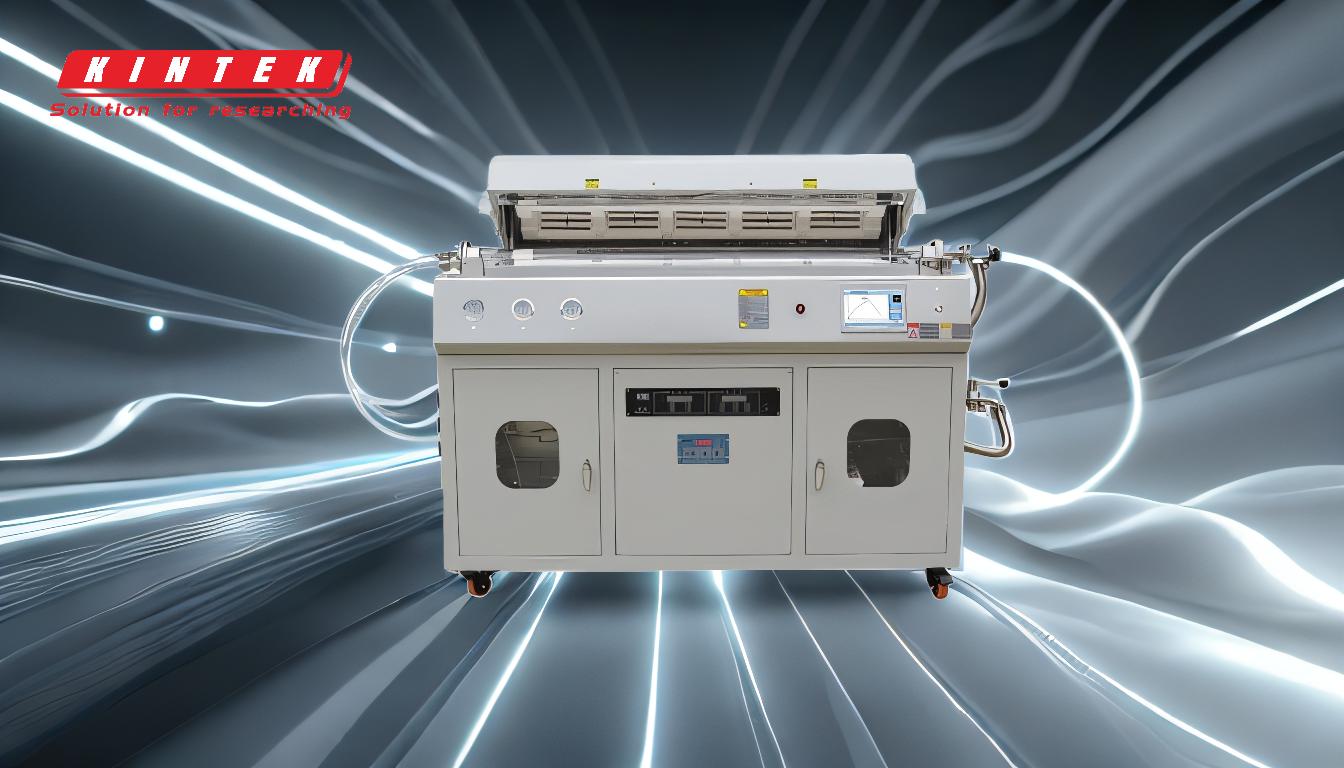
-
Definition and Process of CVD:
- Chemical Vapor Deposition (CVD) is a method where gas molecules are introduced into a reaction chamber containing a heated substrate. The interaction between these gases and the heated surface leads to a chemical reaction or decomposition, forming a solid material film on the substrate. This process is crucial for creating materials that are highly pure and possess strong performance characteristics.
-
Applications of CVD:
- Electronics: CVD is extensively used in the electronics industry for depositing thin films on semiconductors, which are essential for the fabrication of microelectronic devices.
- Cutting Tools: In the manufacturing of cutting tools, CVD is employed to apply coatings that prevent corrosion and wear, thereby extending the tools' lifespan.
- Solar Cells: The method is also pivotal in the production of thin-film solar cells, where photovoltaic materials are deposited onto substrates to convert sunlight into electricity efficiently.
-
Thermal Vapor Deposition:
- A variant of CVD, thermal vapor deposition, involves heating a solid material in a high vacuum chamber to produce vapor pressure. The material is heated to temperatures between 250 to 350 degrees Celsius, transforming it from solid to vapor. This vapor then condenses on the substrate, forming a thin film. This technique is particularly useful for materials that require precise temperature control to achieve the desired deposition.
-
Aerosol Deposition Method:
- Unlike traditional CVD, the aerosol deposition method uses fine ceramic particles that collide with the substrate at high speeds. The kinetic energy from these collisions is converted into binding energy, resulting in a dense, continuous coating layer without the need for additional heat treatment. This method is advantageous for applications requiring robust and durable coatings.
-
Sputtering:
- Sputtering is another deposition technique where high-energy ions bombard a solid metal target, ejecting atoms into a gas phase. These atoms are then deposited onto a part within a vacuum chamber. While distinct from CVD, sputtering is often mentioned in the context of thin film deposition technologies.
-
Industrial Use and Skill Requirement:
- CVD is versatile and can be applied to a wide range of base materials, including glass, metals, and ceramics. However, the process demands a high level of skill and precision, as the conditions under which the deposition occurs (such as temperature and pressure) must be meticulously controlled to ensure the quality of the final product.
-
CVD in Coating Formation:
- In the context of coating formation, CVD involves generating gaseous species containing the coating element within a chamber. These species interact with the surfaces to be coated, facilitated by high temperatures (typically above 500°C) and a reducing atmosphere. This setup ensures the decomposition of molecules and their subsequent deposition onto the substrate, forming a uniform and adherent coating.
-
Vacuum Environment in CVD:
- The use of a vacuum environment in CVD processes, such as pulling particulate chemicals to the workpiece's surface, is crucial for ensuring that the chemical reactions occur efficiently and that the resulting coatings are of high quality. This environment helps in controlling the deposition rate and the properties of the thin film.
In summary, Chemical Vapor Deposition is a critical technology in modern manufacturing and electronics, enabling the creation of high-performance materials and coatings through precise chemical reactions and controlled environmental conditions. Its applications are vast, ranging from enhancing the durability of industrial tools to advancing the efficiency of renewable energy technologies.
Summary Table:
Key Aspect | Description |
---|---|
Definition | A process where gas molecules react on a heated substrate to form a thin film. |
Applications | Electronics (semiconductors), cutting tools, thin-film solar cells. |
Thermal Vapor Deposition | Heats solid materials to produce vapor, condensing into a thin film. |
Aerosol Deposition Method | Uses high-speed ceramic particles to create dense coatings without heat. |
Industrial Use | Requires high skill and precise control of temperature and pressure. |
Vacuum Environment | Ensures efficient chemical reactions and high-quality coatings. |
Discover how CVD can revolutionize your manufacturing process—contact us today for expert guidance!