Heating furnaces are classified based on several factors, including their application, method of heat generation, operating temperature, and specific heat treatment processes. Broadly, furnaces are categorized into combustion-type (fuel-based) and electric-type, with further subdivisions based on their use in household, industrial, or laboratory settings. Industrial furnaces, in particular, are classified by their operating temperature ranges and the specific heat treatment processes they facilitate, such as tempering, annealing, hardening, and carburizing. Additionally, resistance furnaces are categorized as low, medium, or high temperature, depending on their operational capabilities. Common types of furnaces include gas, electric, oil, and propane models, each suited for different applications and temperature requirements.
Key Points Explained:
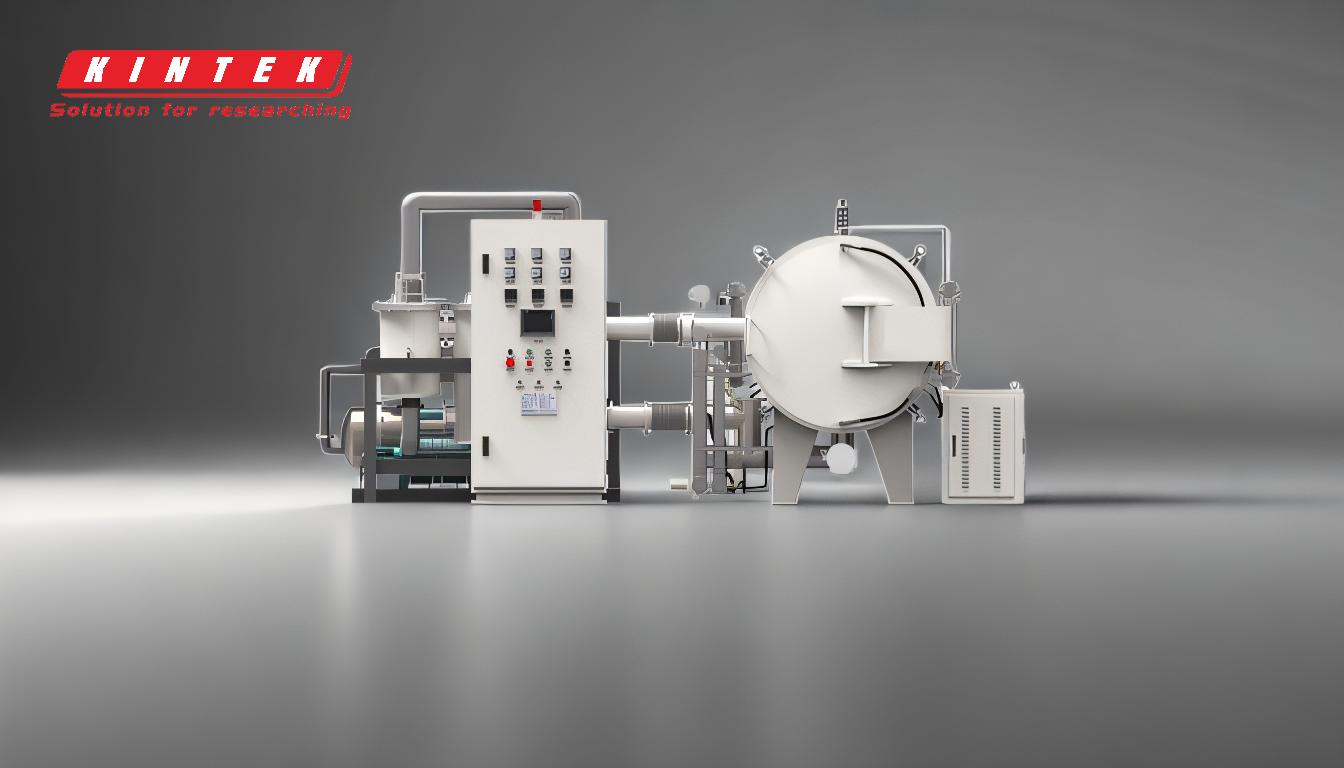
-
Classification Based on Heat Generation Method:
- Combustion-Type Furnaces: These furnaces generate heat by burning fuels such as natural gas, oil, or propane. They are widely used in industrial settings for processes like forging, rolling, and heat treatment. Examples include gas furnaces, oil furnaces, and propane furnaces.
- Electric-Type Furnaces: These furnaces use electrical energy to generate heat, making them suitable for precise temperature control. They are commonly used in laboratories and industries requiring high-temperature processes. Examples include resistance furnaces and induction furnaces.
-
Classification Based on Application:
- Household Furnaces: Designed for residential heating, these furnaces are typically smaller and operate at lower temperatures. They are commonly fueled by natural gas, oil, or electricity.
- Industrial Furnaces: Used in manufacturing and processing industries, these furnaces are designed for high-capacity operations and can handle extreme temperatures. They are classified further based on their specific industrial applications, such as metal melting, heat treatment, or material processing.
- Laboratory Furnaces: These are specialized furnaces used in research and development settings. They offer precise temperature control and are often used for experiments, material testing, and small-scale production.
-
Classification Based on Operating Temperature:
- Low-Temperature Furnaces: Operate at temperatures ranging from 0 to 700°C. They are used for processes like tempering and sub-critical annealing, often employing forced air circulation or liquid baths (oil, lead, or salt).
- Medium-Temperature Furnaces: Operate between 700 and 1050°C. These furnaces are used for processes such as hardening, normalizing, and carburizing of carbon and low alloy steels.
- High-Temperature Furnaces: Operate at temperatures ranging from 1000 to 1400°C. They are used for heat treatment of high-speed steels and other high-temperature cycles. Examples include tube furnaces and box furnaces.
-
Classification Based on Heat Treatment Processes:
- Tempering and Annealing Furnaces: Designed for processes that require lower temperatures, these furnaces are used to improve the ductility and reduce the hardness of materials.
- Hardening and Normalizing Furnaces: Used for processes that require medium to high temperatures to increase the hardness and strength of materials.
- Carburizing and Carbonitriding Furnaces: Specialized furnaces used for surface hardening processes, where carbon or nitrogen is diffused into the surface of the material to enhance its properties.
-
Common Types of Industrial Furnaces:
- Gas Furnaces: Use natural gas as a fuel source and are commonly used in industrial applications due to their efficiency and cost-effectiveness.
- Electric Furnaces: Provide precise temperature control and are used in applications requiring high temperatures and clean environments.
- Oil Furnaces: Use oil as a fuel source and are typically used in industries where gas or electric furnaces are not feasible.
- Propane Furnaces: Similar to gas furnaces but use propane as a fuel source, often used in areas where natural gas is not readily available.
By understanding these classifications, equipment and consumable purchasers can make informed decisions based on the specific requirements of their applications, ensuring optimal performance and efficiency.
Summary Table:
Classification | Key Features |
---|---|
Heat Generation Method | Combustion-Type (gas, oil, propane) and Electric-Type (resistance, induction) |
Application | Household, Industrial, Laboratory |
Operating Temperature | Low (0-700°C), Medium (700-1050°C), High (1000-1400°C) |
Heat Treatment Processes | Tempering, Annealing, Hardening, Carburizing |
Common Types | Gas, Electric, Oil, Propane Furnaces |
Need help selecting the right furnace for your application? Contact our experts today!