Debinding in additive manufacturing is a critical post-processing step that involves removing the binder or carrier material from 3D-printed parts. This process ensures the structural integrity of the final product, prevents contamination during sintering, and improves the efficiency of the manufacturing process. Debinding can be achieved through thermal or chemical methods, depending on the materials and part geometry. Thermal debinding involves heating the part to evaporate the binder, while chemical debinding uses solvents to dissolve the binder. The process typically takes 24-36 hours and requires specialized equipment to avoid contamination and ensure proper binder removal.
Key Points Explained:
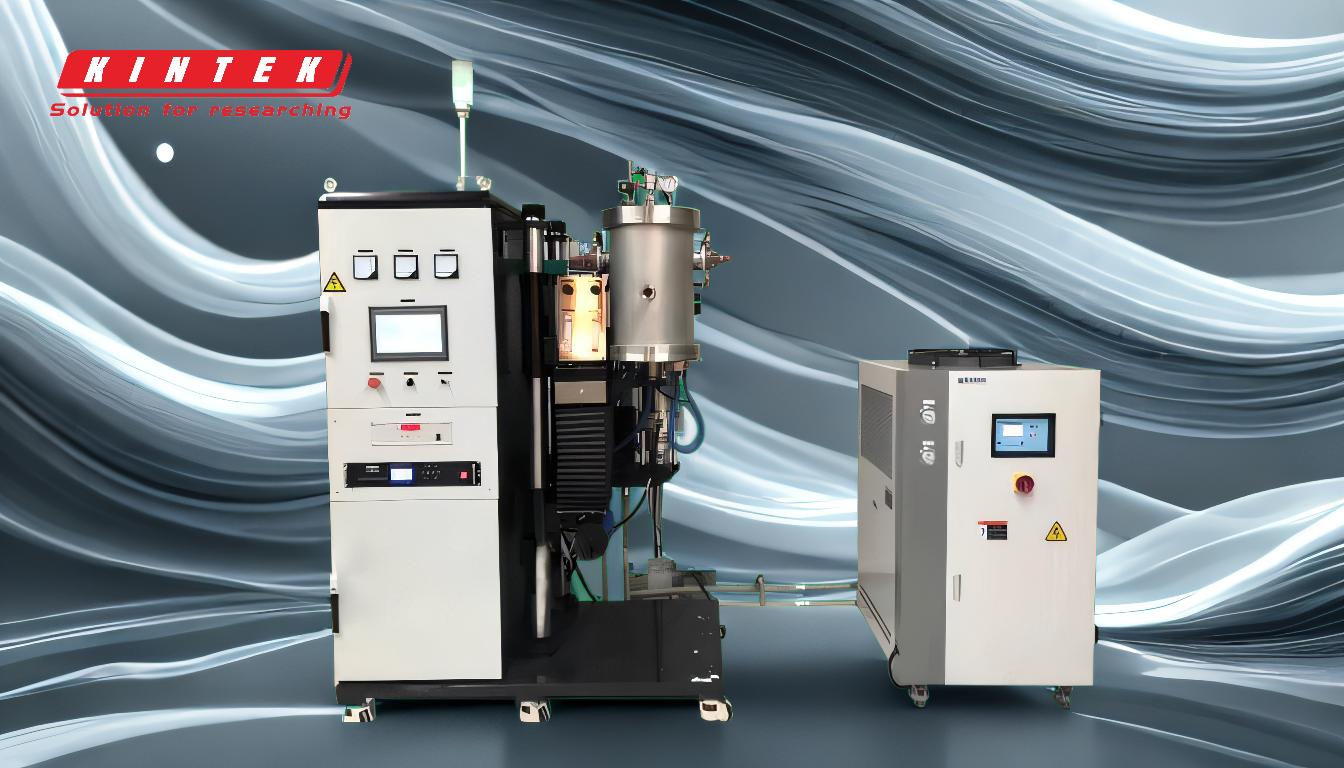
-
Definition of Debinding:
- Debinding is the removal of the binder or carrier material from 3D-printed parts after the printing process.
- It is a necessary step to prepare parts for sintering, ensuring the final product is free from impurities and structural defects.
-
Purpose of Debinding:
- Structural Integrity: Removing the binder ensures the part remains sturdy and free from weak points caused by residual binder material.
- Contamination Prevention: Binder residues can contaminate the furnace during sintering, leading to defects like blistering or pores in the final product.
- Process Efficiency: Proper debinding makes the sintering process faster and more efficient by reducing the risk of furnace clogging and improving material flow.
-
Methods of Debinding:
-
Thermal Debinding:
- Involves heating the printed part in a furnace to evaporate the binder.
- The binder is typically a mixture of organic compounds with varying melting points.
- Specialized debinding plants are used to condense and trap the evaporated polymers, preventing contamination.
-
Chemical Debinding:
- Uses solvents to dissolve the binder material.
- Suitable for parts with complex geometries where thermal debinding might be less effective.
- Requires careful handling of solvents to avoid environmental and safety hazards.
-
Thermal Debinding:
-
Factors Influencing Debinding:
- Part Geometry: Complex geometries may require longer debinding times (up to 24-36 hours) to ensure complete binder removal.
- Material Composition: The type of binder and metal powder used affects the debinding process, as different materials have varying thermal and chemical properties.
- Equipment: Specialized debinding plants are necessary to manage the evaporation and condensation of binders, ensuring a clean and efficient process.
-
Challenges in Debinding:
- Time-Consuming: The process can take up to 24-36 hours, depending on the part’s complexity and size.
- Contamination Risks: Incomplete debinding can lead to contamination during sintering, affecting the final product’s quality.
- Equipment Requirements: Thermal debinding requires precise temperature control and specialized equipment to handle the evaporation and condensation of binders.
-
Importance in Additive Manufacturing:
- Debinding is a critical step in metal additive manufacturing, especially in processes like binder jetting or metal injection molding (MIM).
- It ensures the final product meets the required mechanical and structural properties by removing unwanted binder materials.
- Proper debinding enhances the overall efficiency of the manufacturing process, reducing the risk of defects and improving product consistency.
By understanding the debinding process and its importance, manufacturers can optimize their additive manufacturing workflows to produce high-quality, defect-free parts efficiently.
Summary Table:
Aspect | Details |
---|---|
Definition | Removal of binder/carrier material from 3D-printed parts. |
Purpose | Ensures structural integrity, prevents contamination, improves efficiency. |
Methods | Thermal (heating) or chemical (solvent-based) debinding. |
Factors Influencing | Part geometry, material composition, equipment. |
Challenges | Time-consuming (24-36 hours), contamination risks, specialized equipment. |
Importance | Critical for metal additive manufacturing processes like binder jetting/MIM. |
Optimize your additive manufacturing process with expert debinding solutions—contact us today!