Heat treatment for small parts is a controlled process of heating and cooling metals to alter their physical and chemical properties, making them more suitable for specific applications. This process enhances properties like strength, ductility, hardness, and wear resistance, while also relieving internal stresses and improving machinability. Heat treatment is widely used in industries such as aerospace, automotive, and manufacturing to ensure small parts meet performance and durability requirements. The process involves precise temperature control and cooling rates to achieve desired material characteristics, making it a critical step in the production of high-quality components.
Key Points Explained:
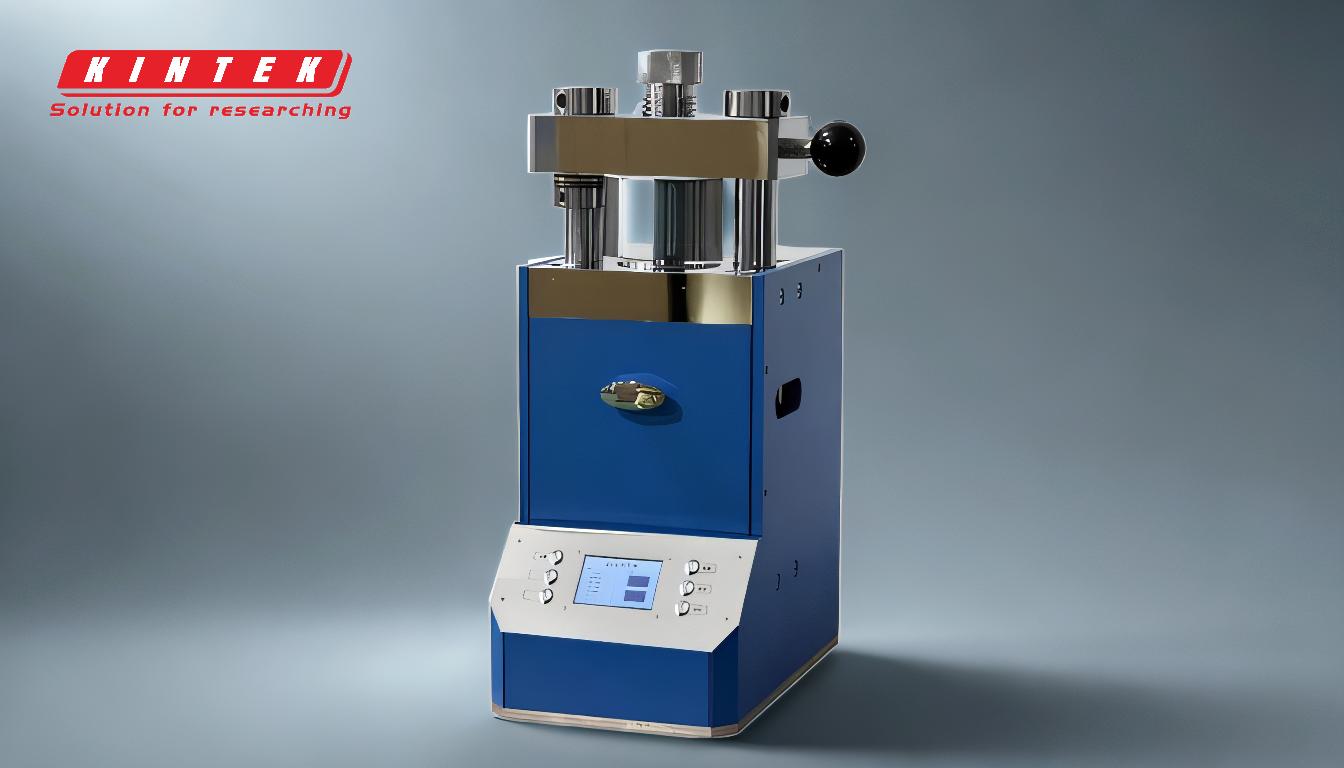
-
Definition and Purpose of Heat Treatment:
- Heat treatment involves controlled heating and cooling of metals to modify their physical and chemical properties.
- The primary purpose is to enhance properties such as strength, ductility, hardness, and wear resistance, making the material more suitable for specific applications.
-
Applications in Small Parts Manufacturing:
- Heat treatment is particularly beneficial for small parts used in industries like aerospace, automotive, and general manufacturing.
- It ensures that small components, such as gears, fasteners, and bearings, meet the required performance standards and have a longer service life.
-
Types of Heat Treatment Processes:
- Annealing: Involves heating the metal to a specific temperature and then slowly cooling it to soften the material, improve ductility, and relieve internal stresses.
- Quenching: Rapid cooling of the metal after heating to increase hardness and strength, often followed by tempering to reduce brittleness.
- Tempering: Reheating quenched metal to a lower temperature to reduce brittleness while maintaining hardness.
- Case Hardening: Adding a hard surface layer to a softer metal core to improve wear resistance while maintaining toughness.
- Normalizing: Heating the metal to a high temperature and then cooling it in air to refine the grain structure and improve mechanical properties.
-
Benefits of Heat Treatment for Small Parts:
- Enhanced Mechanical Properties: Improves strength, toughness, and wear resistance, making parts more durable.
- Stress Relief: Reduces internal stresses, making parts easier to machine or weld.
- Improved Machinability: Softens the material, making it easier to cut, shape, or form.
- Surface Hardness: Increases surface hardness to resist abrasion and wear, extending the life of the part.
- Corrosion Resistance: Forms a corrosion-resistant layer, enhancing the part's longevity in harsh environments.
-
Considerations for Heat Treating Small Parts:
- Material Selection: Different metals and alloys respond differently to heat treatment, so the material must be chosen based on the desired properties.
- Precision Control: Small parts require precise temperature control and uniform heating to avoid distortion or uneven properties.
- Cooling Rates: The rate of cooling significantly affects the final properties, so it must be carefully controlled.
- Post-Treatment Processing: Additional processes like machining or surface finishing may be required after heat treatment to achieve the final dimensions and surface quality.
-
Challenges in Heat Treating Small Parts:
- Size and Geometry: Small parts with complex geometries can be challenging to heat treat uniformly.
- Distortion: Rapid heating and cooling can cause distortion, requiring careful handling and sometimes additional straightening processes.
- Surface Oxidation: Exposure to high temperatures can lead to surface oxidation, necessitating protective atmospheres or post-treatment cleaning.
-
Industry Standards and Quality Control:
- Heat treatment processes must adhere to industry standards (e.g., ASTM, ISO) to ensure consistency and quality.
- Quality control measures, such as hardness testing, microstructure analysis, and dimensional checks, are essential to verify that the parts meet the required specifications.
By understanding these key points, manufacturers and purchasers can make informed decisions about the heat treatment processes needed for small parts, ensuring they meet the desired performance and durability requirements.
Summary Table:
Aspect | Details |
---|---|
Purpose | Enhances strength, ductility, hardness, and wear resistance. |
Applications | Aerospace, automotive, manufacturing (gears, fasteners, bearings). |
Processes | Annealing, quenching, tempering, case hardening, normalizing. |
Benefits | Improved mechanical properties, stress relief, machinability, corrosion resistance. |
Challenges | Size/geometry, distortion, surface oxidation. |
Standards | Adherence to ASTM, ISO, and quality control measures. |
Optimize your small parts with expert heat treatment solutions—contact us today!