Microwave sintering is an advanced ceramic material preparation technique that utilizes microwave energy to heat and densify ceramic materials. This method leverages the dielectric properties of ceramics, allowing for rapid, uniform heating with minimal internal temperature gradients. The process involves several stages, including vacuuming, microwave heating, insulation, and cooling, to achieve high-density, high-performance ceramic products. Microwave sintering offers numerous advantages, such as fast heating speeds, energy efficiency, environmental friendliness, and improved product quality. It is particularly suitable for producing sub-meter or even micron-level ceramic materials, making it a promising option for industrial applications.
Key Points Explained:
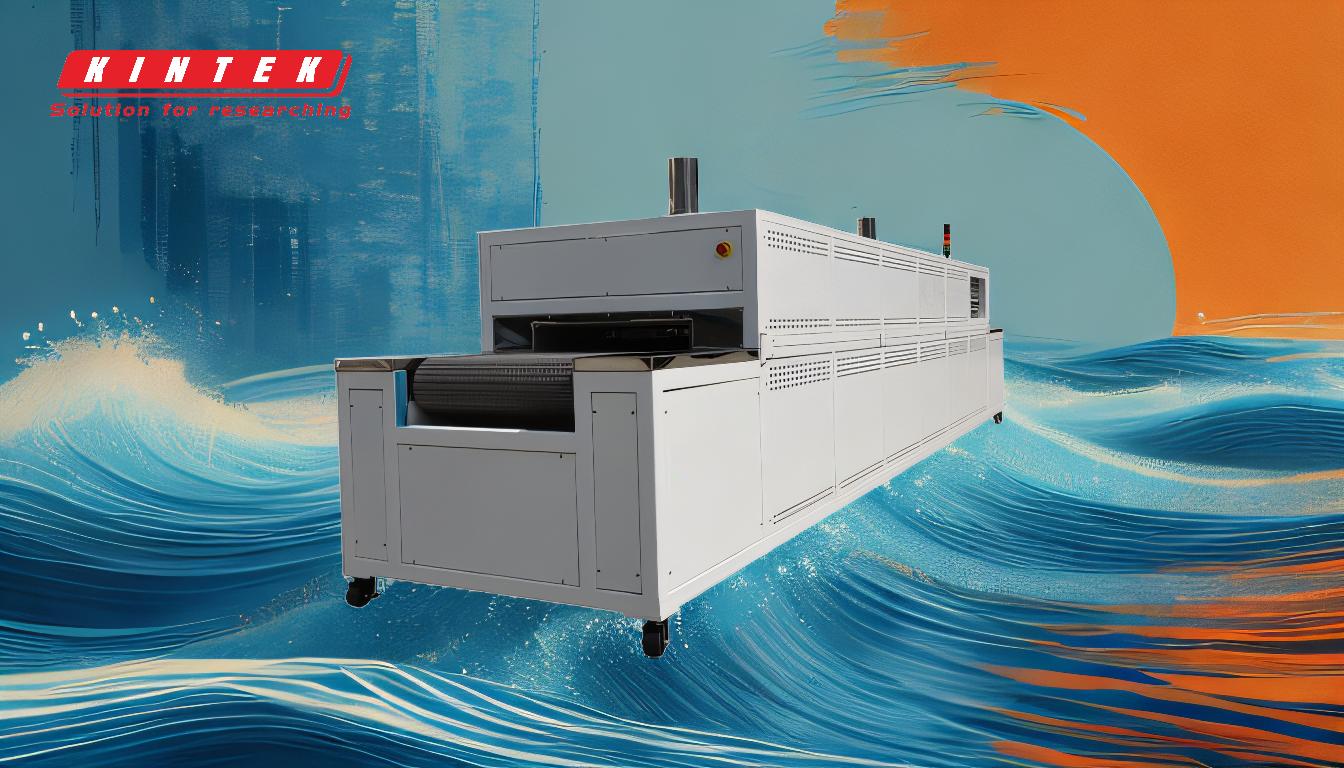
-
Definition and Mechanism of Microwave Sintering:
- Microwave sintering uses microwave energy to couple with the microstructure of ceramic materials, generating heat through dielectric loss in an electromagnetic field.
- This method heats materials uniformly, with minimal internal temperature gradients, enabling low-temperature and rapid sintering.
- The process involves a microwave source, a heating cavity, and a material transfer system.
-
Components of a Microwave Sintering Furnace:
- Microwave Source: Generates microwave energy to heat the ceramic material.
- Heating Cavity: The chamber where the ceramic material is placed and heated.
- Material Transfer System: Facilitates the movement of materials into and out of the furnace.
- Susceptor Plate and Material: Absorbs microwave energy and converts it into heat, often used in sintering trays to enhance heating efficiency.
-
Stages of the Microwave Sintering Process:
- Charging: Placing the ceramic material into the furnace.
- Vacuuming: Evacuating the furnace to remove gases and impurities, ensuring a clean environment for sintering.
- Microwave Heating: Using microwave energy to raise the material to the sintering temperature.
- Insulation: Maintaining the temperature to allow chemical reactions and crystallization, ensuring material densification.
- Cooling: Gradually cooling the material to room temperature to prevent thermal stress and cracking.
-
Advantages of Microwave Sintering:
- Fast Heating Speed: Microwave sintering heats materials much faster than conventional methods, reducing processing time.
- Uniform Temperature Distribution: Ensures consistent material properties throughout the product.
- Energy Efficiency: Uses less energy compared to traditional sintering methods.
- Environmental Friendliness: Reduces emissions and waste, making it a greener option.
- Improved Product Quality: Prevents oxidation and contamination, resulting in higher-quality ceramic materials.
-
Applications and Prospects:
- Microwave sintering is particularly effective for preparing sub-meter or even micron-level ceramic materials.
- It is widely used in the production of high-performance ceramics, such as those used in electronics, aerospace, and medical applications.
- The method is scalable for larger volume production, making it suitable for industrial applications.
-
Challenges and Solutions:
- Cooling the Operating Equipment: The rapid heating process can cause equipment to overheat. Auxiliary cooling systems are often used to address this issue.
- Material Compatibility: Not all materials are suitable for microwave sintering. Susceptor materials are often required to enhance heating efficiency.
-
Comparison with Traditional Sintering Methods:
- Speed: Microwave sintering is significantly faster than conventional methods.
- Energy Consumption: It is more energy-efficient, reducing operational costs.
- Environmental Impact: Produces fewer emissions and waste, aligning with sustainability goals.
- Product Quality: Results in higher-quality materials with fewer defects.
In summary, microwave sintering is a cutting-edge technique that offers numerous benefits over traditional sintering methods. Its ability to produce high-quality ceramic materials quickly and efficiently makes it a valuable tool for various industrial applications. However, challenges such as equipment cooling and material compatibility must be addressed to fully realize its potential.
Summary Table:
Aspect | Details |
---|---|
Definition | Uses microwave energy to heat and densify ceramic materials. |
Key Components | Microwave source, heating cavity, material transfer system, susceptor plate. |
Process Stages | Charging, vacuuming, microwave heating, insulation, cooling. |
Advantages | Fast heating, uniform temperature, energy efficiency, eco-friendly. |
Applications | Electronics, aerospace, medical, industrial ceramics. |
Challenges | Equipment cooling, material compatibility. |
Comparison with Traditional | Faster, more energy-efficient, eco-friendly, higher-quality products. |
Ready to explore the benefits of microwave sintering for your ceramic production? Contact us today to learn more!