Plasma deposition of polymers is a sophisticated manufacturing technique that utilizes a plasma state—a highly energized gas composed of ions, electrons, and neutral particles—to deposit thin polymer films onto a substrate. This process involves superheating a coating gas into an ionic form, which then reacts with the surface of the substrate at elevated pressures. The high-energy charged particles in the plasma liberate atoms from a target material, and these neutral atoms escape the plasma's electromagnetic fields to collide with the substrate, forming a thin, uniform layer. This method is highly versatile, allowing for precise control over layer thicknesses and compatibility with a wide range of materials, making it suitable for applications requiring nanometer-scale precision.
Key Points Explained:
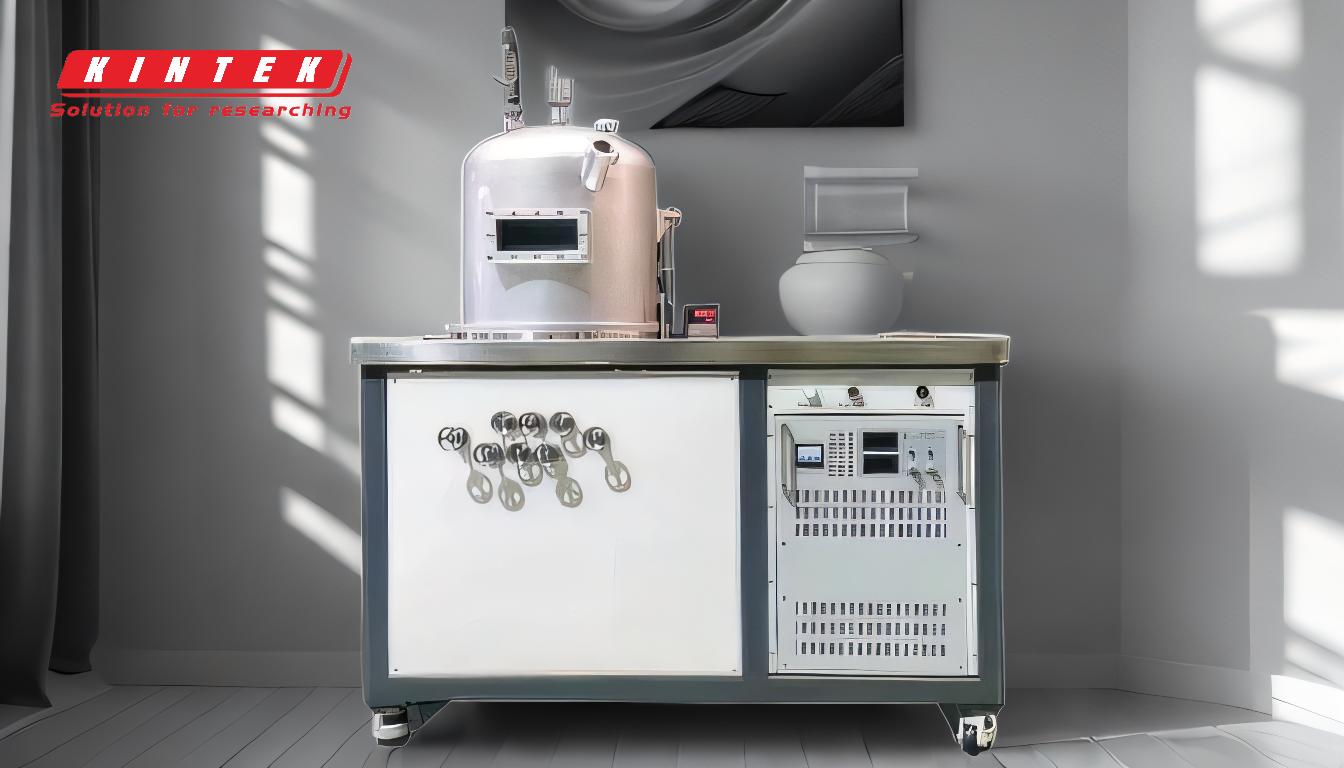
-
Definition of Plasma Deposition of Polymers:
- Plasma deposition is a process where a polymer coating is applied to a substrate using a plasma state. The plasma is created by superheating a gas into an ionic form, which then interacts with the substrate to form a thin film.
-
Mechanism of Plasma Deposition:
- Ionization of Gas: The coating gas is superheated to form a plasma, which consists of ions, electrons, and neutral particles.
- Liberation of Atoms: High-energy charged particles in the plasma liberate atoms from a target material.
- Deposition on Substrate: These neutral atoms escape the plasma's electromagnetic fields and collide with the substrate, where they are deposited to form a thin film.
-
Versatility of Plasma Deposition:
- Material Compatibility: Plasma deposition can be used with a wide range of materials, including various polymers, metals, and ceramics.
- Precision Control: The technique allows for precise control over the thickness of the deposited layer, often down to a few nanometers, making it ideal for applications requiring high precision.
-
Applications of Plasma Deposition:
- Microelectronics: Used for depositing thin films in the fabrication of semiconductors and other electronic components.
- Biomedical Devices: Applied in the coating of medical implants and devices to enhance biocompatibility and performance.
- Optical Coatings: Utilized in the production of anti-reflective and protective coatings for lenses and other optical components.
-
Advantages of Plasma Deposition:
- Uniformity: The process ensures a uniform coating over complex geometries and large surface areas.
- Adhesion: The high-energy nature of the plasma improves the adhesion of the coating to the substrate.
- Environmental Benefits: Plasma deposition is a clean process that produces minimal waste and does not require the use of solvents.
-
Challenges and Considerations:
- Cost: The equipment and operational costs for plasma deposition can be high, making it less accessible for small-scale applications.
- Complexity: The process requires precise control of various parameters, such as pressure, temperature, and plasma composition, which can be challenging to manage.
In summary, plasma deposition of polymers is a highly advanced and versatile technique that leverages the unique properties of plasma to deposit thin, uniform polymer films on various substrates. Its ability to work with a wide range of materials and achieve precise control over layer thicknesses makes it invaluable in industries requiring high-performance coatings. However, the complexity and cost of the process are important factors to consider when selecting this method for specific applications.
Summary Table:
Aspect | Details |
---|---|
Definition | Coating process using plasma to deposit thin polymer films on substrates. |
Mechanism | Ionization of gas → Liberation of atoms → Deposition on substrate. |
Versatility | Works with polymers, metals, ceramics; precise thickness control. |
Applications | Microelectronics, biomedical devices, optical coatings. |
Advantages | Uniformity, strong adhesion, environmentally friendly. |
Challenges | High cost, complex parameter control. |
Ready to explore plasma deposition for your project? Contact our experts today to get started!